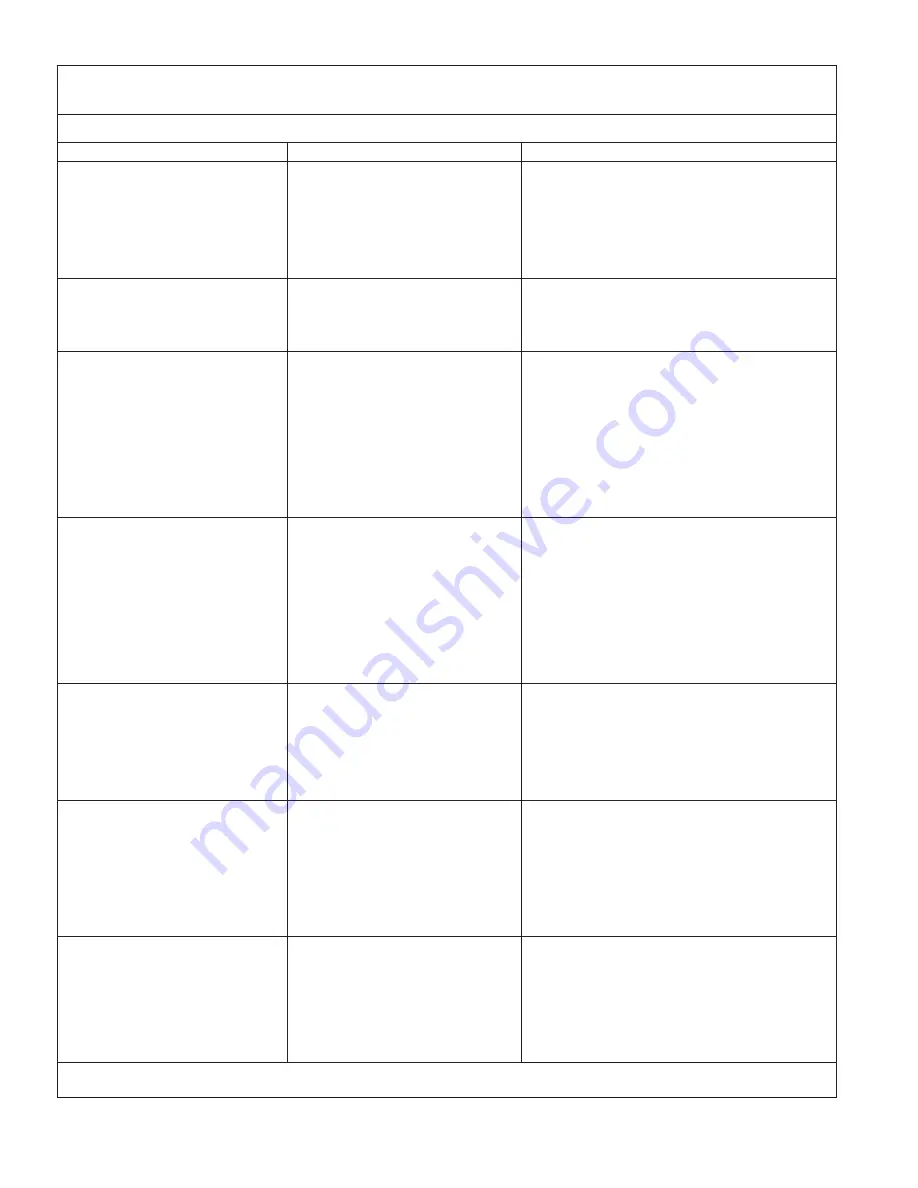
Troubleshooting Procedures (cont.)
Troubleshooting the Whirlpool System
Symptoms
Probable Causes
Recommended Action
C.
Wiring harness from user
keypad to control is loose,
disconnected or damaged.
C.
Check wiring for proper connections
Replace wiring harness if necessary.
Refer to installer/dealer.
D.
Keypad doesn’t work.
D.
Replace user keypad. Refer to
installer/dealer.
E.
Control doesn’t work.
E.
Replace control. Refer to
installer/dealer.
2.
Motor starts, but all jets
are not functioning.
A.
Jet is closed.
A.
Rotate jet trim ring counterclockwise to
open.
B.
Jet not installed correctly.
B.
Reinstall jet; check for O-ring damage.
C.
Jets are blocked.
C.
Remove blockage.
3.
User keypad is
illuminated but does not
respond to buttons.
A.
Control program is locked.
A.
Reset GFCI or RCD.
B.
Wiring harness from user
keypad to control is loose,
disconnected or damaged.
B.
Check wiring for proper connections.
Replace wiring harness if necessary.
Refer to installer/dealer.
C.
Keypad doesn’t work.
C.
Replace user keypad. Refer to
installer/dealer.
D.
Control doesn’t work.
D.
Replace control. Refer to
installer/dealer.
4.
User keypad indicator bar
keeps scanning at
power-up.
A.
Control program is locked.
A.
Reset GFCI or RCD.
B.
Wiring harness from user
keypad to control is loose,
disconnected or damaged.
B.
Check wiring for proper connections.
Replace wiring harness if necessary.
Refer to installer/dealer.
C.
Keypad doesn’t work.
C.
Replace user keypad. Refer to
installer/dealer.
D.
Control doesn’t work.
D.
Replace control. Refer to
installer/dealer.
5.
User keypad is
illuminated, but pump
won’t start.
A.
Power cord from pump to
control is loose,
disconnected or damaged.
A.
Check wiring for proper connections. If
problem persists, refer to
installer/dealer.
B.
Pump doesn’t work.
B.
Replace pump. Refer to
installer/dealer.
C.
Control doesn’t work.
C.
Replace control. Refer to
installer/dealer.
6.
Motor runs but pump
won’t prime (cavitates).
A.
Pump is shimmed too high.
A.
Lower pump/control to subfloor level.
B.
Small air leak at pump inlet.
B.
Securely tighten nuts(s) on intake side
of pump.
C.
Motor/pump doesn’t work.
C.
Replace motor/pump. Refer to
installer/dealer.
D.
Control doesn’t work.
D.
Replace control. Refer to
installer/dealer.
7.
Pump stops before 18
minutes.
A.
GFCI or RCD tripped.
A.
Identify source of fault, and correct.
Reset GFCI or RCD.
B.
Suction is blocked.
B.
Remove obstruction.
C.
Jets are blocked.
C.
Remove blockage.
D.
Motor overheated and
protection device activated.
D.
Check for blockage at suction and/or
jets. Remove blockage and allow motor
to cool.
Kallista
9
1034059-5-C
Summary of Contents for P50016
Page 11: ...Service Parts Finish color code must be specified when ordering Kallista 11 1034059 5 C...
Page 28: ...Proc dures de d pannage cont 1034059 5 C Fran ais 12 Kallista...
Page 53: ...1034059 5 C...
Page 54: ...1034059 5 C...
Page 55: ...1034059 5 C...
Page 56: ...USA Canada 1 888 4 KALLISTA Fax 1 888 272 3094 kallista com 2007 KALLISTA 1034059 5 C...