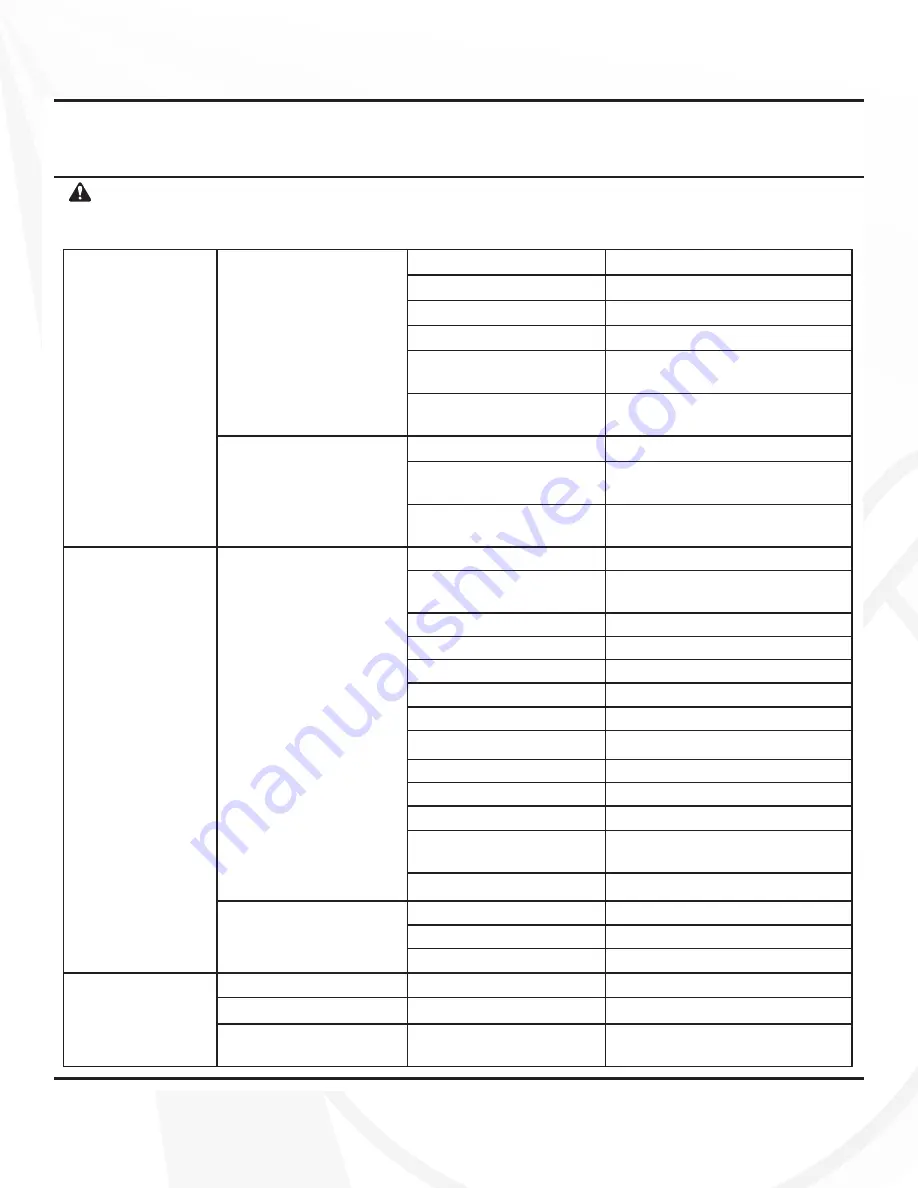
kaivac
cleaning
systems
TM
P a g e ǀ
2 2
1-800-287-1136
Customer/Technical Support
4.1 t
RoUbLeshooting
4.0 Troubleshooting and Upkeep
Electrical
No Power to pump or
vac motor
Machine not plugged in
Plug machine in
Switch not “on”
Check switches for “on”
GFCI tripped
Test and reset GFCI
Building circuit overloaded
Check and reset circuit
Switch wires loose
Disconnect power and check for
loose wire
Connections loose
Disconnect power and check for
loose wire under panel
Electrical burning smell
Vac motor brushes worn
Remove vac motor and repair
Vac motor hung up
Release pressure on hose and jog
vac switch, or replace
Pump motor hung up
Release pressure on hose and jog
pump switch, or replace
Vacuum System
No/Weak vacuum
Vac tank full
Empty vac tank
Squeegee blades or wheels
worn
Replace wheels or blades and
check periodically
Float shutoff screen dirty
Spray off float screen to clean
Float ball stuck
Tap float and release/clean
Damaged hose
Cut and repair/replace
Dump hose plug missing
Contact dealer and replace
Access lid not right
Tighten lid hand tight
Vacuum hose plugged
Flush hose to remove debris
Too much liquid in vac hose Allow air in when vacuuming
Vac hose still wrapped
Unwrap vac hose fully
Exhaust plugged
Remove HEPA filter and clean
Leak in vac tank
If repairable, clean and dry affected
area and seal with silicone
HEPA filter clogged
Remove HEPA filter and clean
Moisture from exhaust
Vac tank full
Dump vac tank
Float shutoff missing
Replace
Excessive foam in vac tank
Use defoamer
Blow Dry System
No air flow
Hose disconnected
Reconnect hose
Moisture from exhaust
Water in blow hose
Dry blow line
Suction, not blow action
Vacuum hose connected to
vac tank
Reconnect to vac motor exhaust
hose
CAUTION
:
Always unplug machine before lifting electric cover assembly.
AREA
PROBLEM
POSSIBLE CAUSE
SOLUTION
High Pressure
System
No water from pump
or low pressure
Out of water
Fill water tank
Gun nozzle plugged
Remove orifice with Allen wrench
and clean
Air in pump (vapor lock)
Use power prime technique
Gun orifice missing
Replace orifice
Water tank filter plugged
Clean tank and filter
In-line bowl filter plugged
Remove filter cover and clean
Bowl filter lid loose
Gently tighten bowl cover
Pressure hose damaged
Repair or replace
Quick disconnect leaking
Tighten or replace
Injector plugged
Remove safety cap from chemical
and blow small amounts of
compressed air into line
Pulse hose damaged
Repair or replace
Regulator failed
Replace
Hose kinked
Unkink and check for damage
Seals in pump need replaced
Remove and replace seals
Bad fan pattern or
pinpoint pattern on
gun
Debris in nozzle
Remove orifice with Allen wrench
and clean
Orifice damaged
Remove and replace
Chemical Injection
System
No chemical flow
Out of chemical
Refill chemical
Safety cap not secure
Check safety cap/tighten
Chemical valve “off”
Check on/off valve
Safety cap plugged
Replace cap
Spray gun in wrong mode
Make sure gun nozzle is pulled out
away from gun chemical mode
Metering tip plugged
Check metering tip for clog
Injector plugged
Remove safety cap from chemical and blow
small amounts of compressed air into line
Air entering system
Check for air entering system
around chemical lines or injector
Injector installed backwards
If fluttering or pulsing sound can be
heard while spraying or when machine
is running, it is possible that your injec-
tor is in backwards. Remove; reinstall.
Kink in chemical line
Replace chemical line