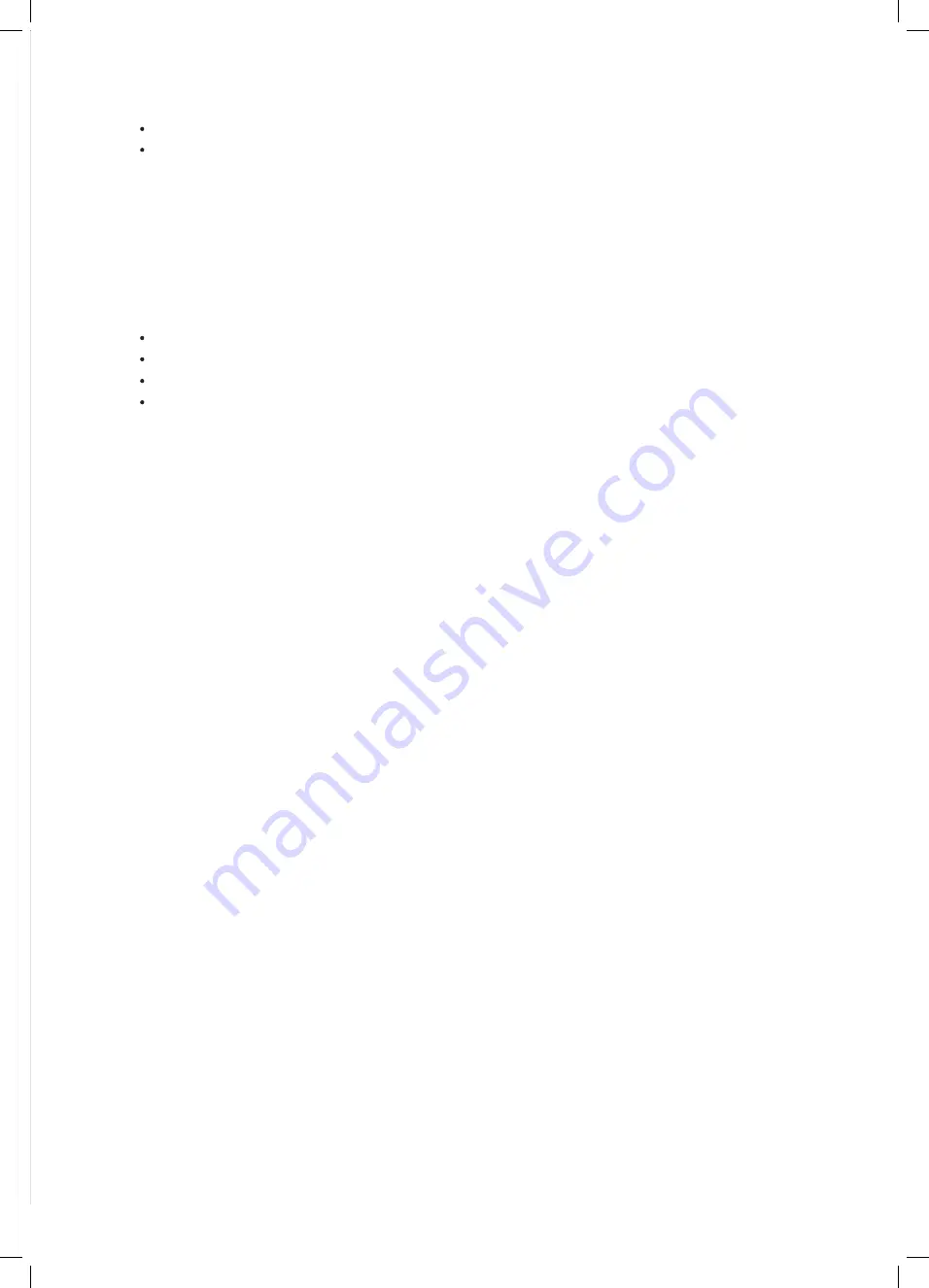
71
b) Particular attention shall be paid to the following to ensure that by working on electrical components, the casing is not altered
in such a way that the level of protection is affected. This shall include damage to cables, excessive number of connections,
terminals not made to original specification, damage to seals, incorrect fitting of glands, etc.
Ensure that apparatus is mounted securely.
Ensure that seals or sealing materials have not degraded such that they no longer serve the purpose of preventing the
ingress of flammable atmospheres. Replacement parts shall be in accordance with the manufacturer s specifications.
11) Repair to intrinsically safe components
Do not apply any permanent inductive or capacitance loads to the circuit without ensuring that this will not exceed the permissi-
ble voltage and current permitted for the equipment in use. Intrinscially safe components are the only types that can be worked
on while live in the presence of a flammable atmosphere. The test apparatus shall be at the correct rating. Replace components
only with parts specified by the manufacturer. Other parts may result in the ignition of refrigerant in the atmosphere from a leak.
12) Cabling
Check that cabling will not be subject to wear, corrosion, excessive pressure, vibration, sharp edges or any other adverse
environmental effects. The check shall also take into account the effects of aging or continual vibration from sources such as
compressors or fans.
13) Detection of flammable refrigerants
Under no circumstances shall potential sources of ignition be used in the searching for or detection of refrigerant leaks. A halide
torch (or any other detector using a naked flame) shall not be used.
The refrigerant charge shall be recovered into the correct recovery cylinders. The system shall be flushed with OFN to render
the unit safe. This process may need to be repeated several times.
Compressed air or oxygen shall not be used for this task.
Flushing shall be achieved by breaking the vacuum in the system with OFN and continuing to fill until the working pressure is
achieved, then venting to atmosphere, and finally pulling down to a vacuum. This process shall be repeated until no refrigerant
is within the system.
When the final OFN charge is used, the system shall be vented down to atmospheric pressure to enable work to take place.
This operation is absolutely vital if brazing operations on the pipe-work are to take place.
Ensure that the outlet for the vacuum pump is not closed to any ignition sources and there is ventilation available.
16) Charging procedures
In addition to conventional charging procedures, the following requirements shall be followed:
14) Leak detection methods
The following leak detection methods are deemed acceptable for systems containing flammable refrigerants. Electronic leak
detectors shall be used to detect flammable refrigerants, but the sensitivity may not be adequate, or may need re-calibration.(-
Detection equipment shall be calibrated in a refrigerant-free area.) Ensure that the detector is not a potential source of ignition
and is suitable for the refrigerant. Leak detection equipment shall be set at a percentage of the LFL of the refrigerant and shall
be calibrated to the refrigerant employed and the appropriate percentage of gas (25% maximum) is confirmed. Leak detection
fluids are suitable for use with most refrigerants but the use of detergents containing chlorine shall be avoided as the chlorine
may react with the refrigerant and corrode the copper pipe-work. If a leak is suspected ,all naked flames shall be removed or
extinguished. If a leakage of refrigernat is found which requires brazing, all of the refrigerant shall be recovered from the system,
or isolated(by means of shut off valves) in a part of the system remote from the leak . Oxygen free nitrogen(OFN) shall then be
purged through the system both before and during the brazing process.
15) Removal and evacuation
When breaking into the refrigerant circuit to make repairs of for any other purpose conventional procedures shall be used,
However, it is important that best practice is followed since flammability is a consideration. The following procedure shall be
adhered to:
Ensure that contamination of different refrigerants does not occur when using charging equipment. Hoses or lines shall be
as short as possible to minimize the amount of refrigerant contained in them.
Cylinders shall be kept upright.
Ensure that the refrigeration system is earthed prior to charging the system with refrigerant.
Label the system when charging is complete(if not already).
Remove refrigerant;
Purge the circuit with inert gas;
Evacuate;
Purge again with inert gas;
Open the circuit by cutting or brazing.
The use of silicon sealant may inhibit the effectiveness of some types of leak detection equipment. Instrinsically safe
components do not have to be isolated prior to working on them.
NOTE
72
18) Labelling
Equipment shall be labelled stating that it has been de-commissioned and emptied of refrigerant. The label shall be dated and
signed. Ensure that there are labels on the equipment stating the equipment contains flammable refrigerant.
19) Recovery
When removing refrigerant from a system, either for service or decommissioning, it is recommended good practice that all
refrigerants are removed safely.
When tranferring refrigerant into cylinders, ensure that only appropriate refrigerant recovery cylinders are employed. Ensure
that the correct numbers of cylinders for holding the total system charge are available. All cylinders to be used are designated
for the recovered refrigerant and labelled for that refrigerant(i.e special cylinders for the recovery of refrigerant). Cylinders shall
be complete with pressure relief valve and associated shut-off valves in good working order.
Empty recovery cylinders are evacuated and, if possible, cooled before recovery occurs.
The recovery equipment shall be in good working order with a set of instructions concerning the equipment that is at hand and
shall be suitable for the recovery of flammable refrigerants. In addition, a set of calibrated weighing scales shall be available and
in good working order.
Hoses shall be complete with leak-free disconnect couplings and in good condition. Before using the recovery machine, check
that it is in satisfactory working order, has been properly maintained and that any associated electrical components are sealed
to prevent ignition in the event of a refrigerant release. Consult manufacturer if in doubt.
The recovered refrigerant shall be returned to the refrigerant supplier in the correct recovery cylinder, and the relevant Waste
Transfer Note arranged. Do not mix refrigerants in recovery units and especially not in cylinders.
If compressors or compressor oils are to be removed, ensure that they have been evacuated to an acceptable level to make
certain that flammable refrigerant does not remain within the lubricant. The evacuation process shall be carried out prior to
retruning the compressor to the suppliers. Only electric heating to the compressor body shall be employed to accelerate this
process. When oil is drained from a system, it shall be carried out safely.
20) Transportation, marking and storage for units
Transport of equipment containing flammable refrigerants Compliance with the transport regulations
Marking of equipment using signs Compliance with local regulations
Disposal of equipment using flammable refrigerants Compliance with national regulations
Storage of equipment/appliances
The storage of equipment should be in accordance with the manufacturer’s instructions.
Storage of packed (unsold) equipment
Storage package protection should be constructed such that mechanical damage to the equipment inside the package will not
cause a leak of the refrigerant charge.
The maximum number of pieces of equipment permitted to be stored together will be determined by local regulations.
17) Decommissioning
Before carrying out this procedure, it is essential that the technician is completely familiar with the equipment and all its detail.
It is recommended good practice that all refrigerants are recovered safely. Prior to the task being carried out, an oil and refriger-
ant sample shall be taken.
In case analysis is required prior to re-use of reclaimed refrigerant. It is essential that electrical power is available before the
task is commenced.
a) Become familiar with the equipment and its operation.
b) Isolate system electrically
c) Before attempting the procedure ensure that:
Mechanical handling equipment is available, if required, for handling refrigerant cylinders;
All personal protetive equipment is available and being used correctly;
The recovery process is supervised at all times by a competent person;
Recovery equipment and cylinders conform to the appropriate standards.
Extreme care shall be taken not to overfill the refrigeration system.
Prior to recharging the system it shall be pressure tested with OFN. The system shall be leak tested on completion of
charging but prior to commissioning. A follow up leak test shall be carried out prior to leaving the site.
d) Pump down refrigerant system, if possible.
e) If a vacuum is not possible, make a manifold so that refrigerant can be removed from various parts of the system.
f) Make sure that cylinder is situated on the scales before recovery takes place.
g) Start the recovery machine and operate in accordance with manufacturer s instructions.
h) Do not overfill cylinders. (No more than 80% volume liquid charge).
i) Do not exceed the maximum working pressure of the cylinder, even temporarily.
j) When the cylinders have been filled correctly and the process completed, make sure that the cylinders and the equipment are
removed from site promptly and all isolation valves on the equipment are closed off.
k) Recovered refrigerant shall not be charged into another refrigeration system unless it has been cleaned and checked.
77
76
Summary of Contents for KHC-22RY3
Page 1: ...INSTALATIONMANUAL MONO TYPE HEAT PUMP EN...
Page 2: ......
Page 79: ...16125300002403 V C 79...
Page 80: ...kaisai com...