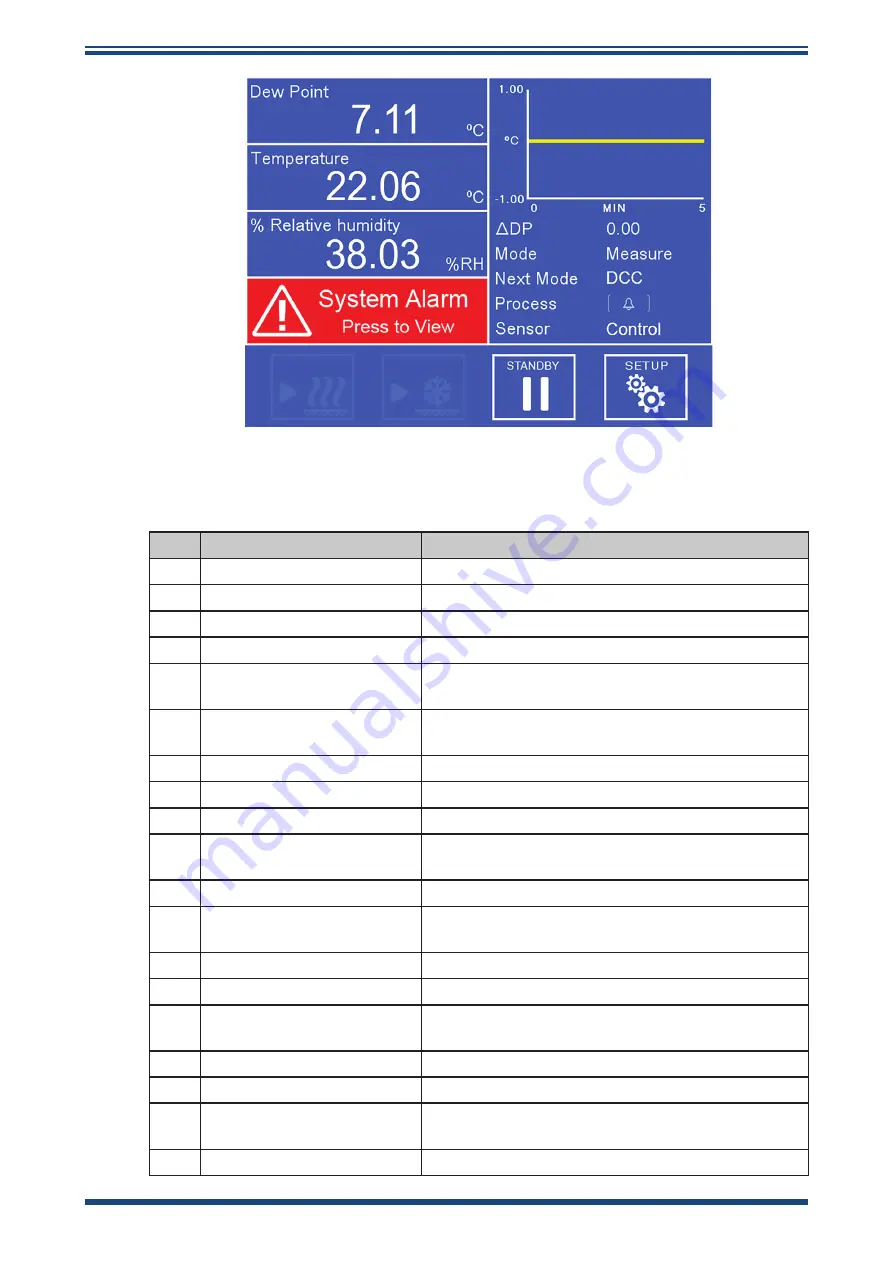
Optidew User’s Manual
Kahn Instruments
41
MAINTENANCE
Figure 30
System alarm
Possible Fault Codes
No.
Name
Description
06
Mirror Overheat
Mirror Temperature above 266°F/130°C
02
Optics Fault (Search Fail)
Unable to establish clean mirror condition
03
Optics Fault (< Min Limit)
Signal below allowable limit
04
Optics Fault (> Max Limit)
Signal above allowable limit
08
Heating Saturation
TEC drive saturated in heating mode beyond
allowable time limit
09
Cooling Saturation
TEC drive saturated in cooling mode beyond
allowable time limit
01
Mirror Pt1000 Fault
Chilled Mirror sensor internal Pt1000 fault
04
Temp. Probe Fault
External temperature probe fault
07
Pressure Tx. Fault
External pressure transmitter fault
17
Mirror Contaminated
Mirror requires cleaning followed by Optics
Calibration
11
Mirror Pt1000 Fault (Open)
Chilled Mirror sensor Pt1000 open circuit
12
Mirror Pt1000 Fault (Low)
Chilled Mirror sensor Pt1000 short circuit/below
lower limit
13
Mirror Pt1000 Fault (High)
Chilled Mirror sensor Pt1000 above upper limit
08
Temp. Probe Fault (Open)
External temperature probe open circuit
09
Temp. Probe Fault (Low)
External temperature probe short circuit/below
lower limit
10
Temp. Probe Fault (High)
External temperature probe above upper limit
14
Pressure Tx. Fault (Open)
Pressure transmitter signal < 0.2mA (open circuit)
15
Pressure Tx. Fault (Alarm)
Pressure transmitter signal 3.6-3.8mA OR 20.5-
21mA
16
Pressure Tx. Fault (Fail)
Pressure transmitter signal > 21mA, or < 3.6mA
Summary of Contents for Optidew Series
Page 2: ...Optidew For Kahn Instruments contact information please go to www kahn com...
Page 13: ...Optidew User s Manual 4 October 2019 INSTALLATION This page is intentially left blank...
Page 53: ...Optidew User s Manual 44 October 2019 APPENDIX A Appendix A Technical Specifications...
Page 56: ...Optidew User s Manual Kahn Instruments 47 APPENDIX B Appendix B Modbus Register Map...
Page 65: ...Optidew User s Manual 56 October 2019 APPENDIX C Appendix C Dimensional Drawings...
Page 70: ...Optidew User s Manual Kahn Instruments 61 APPENDIX C Dual Stage Dewpoint Sensor...
Page 71: ...Optidew User s Manual 62 October 2019 APPENDIX C Sample Block...
Page 74: ...Optidew User s Manual Kahn Instruments 65 APPENDIX C...
Page 75: ...Optidew User s Manual 66 October 2019 APPENDIX C...
Page 76: ...Optidew User s Manual Kahn Instruments 67 APPENDIX C...
Page 77: ...Optidew User s Manual 68 October 2019 APPENDIX C...
Page 78: ...Optidew User s Manual Kahn Instruments 69 APPENDIX C...
Page 79: ...Optidew User s Manual 70 October 2019 APPENDIX C...
Page 80: ...Optidew User s Manual Kahn Instruments 71 APPENDIX C...
Page 81: ...Optidew User s Manual 72 October 2019 APPENDIX C...
Page 82: ...Optidew User s Manual Kahn Instruments 73 APPENDIX C...
Page 83: ...Optidew User s Manual 74 October 2019 APPENDIX C...
Page 84: ...Optidew User s Manual Kahn Instruments 75 APPENDIX C...
Page 85: ...Optidew User s Manual 76 October 2019 APPENDIX C...
Page 86: ...Optidew User s Manual Kahn Instruments 77 APPENDIX C...
Page 87: ...Optidew User s Manual 78 October 2019 APPENDIX C...
Page 88: ...Optidew User s Manual Kahn Instruments 79 APPENDIX C...