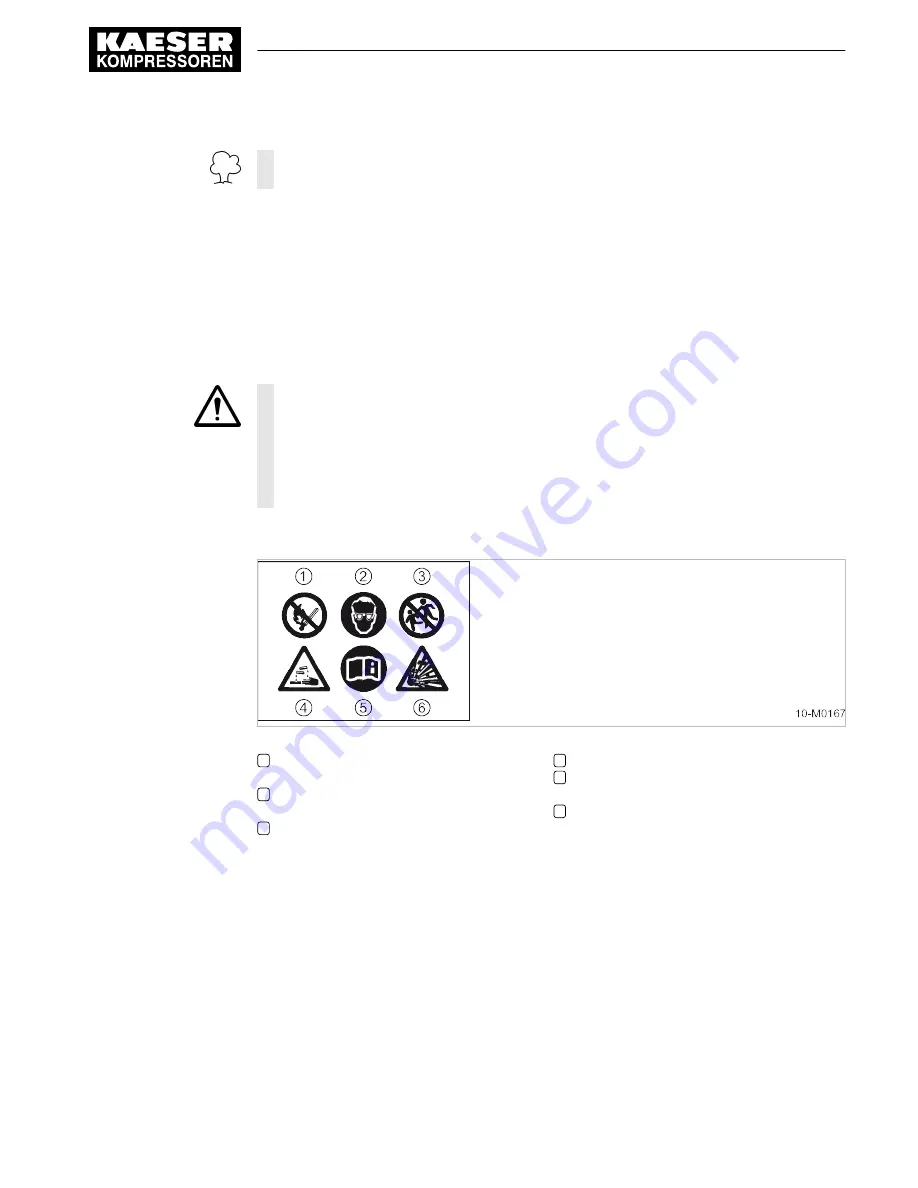
Dispose of old oil filters, old oil and materials contaminated with oil according to environmen‐
tal protection regulations.
10.3.5 Motor belt maintenance
➤ See the engine service manual.
10.3.6 Battery maintenance
➤ Check the charging system if the battery discharges without reason.
10.3.6.1 Safety
WARNING
Danger of acid burns from escaping electrolyte.
➤ Wear appropriate protective clothing including acid-proof rubber gloves.
➤ Always wear eye and face protection.
➤ Do not tip the battery. Electrolyte may run out of the vent holes.
➤ Work with caution.
Observe the following points when working on the batteries:
Fig. 31 Warning stickers on the battery
1
Fire, sparks, open flame and smoking are
forbidden.
2
Wear eye and face protection. Danger of
acid burn
3
Keep children well away from batteries
and acid.
4
Batteries are filled with caustic electrolyte.
5
Observe the battery manufacturer's instruc‐
tions.
6
Explosion hazard
➤ Take heed of any safety symbols on the battery labels.
Further instructions on working with batteries:
1. Do not remove battery terminal covers unnecessarily.
2. Do not lay tools on the battery. These can lead to short circuiting, overheating and battery
bursting.
3. Take particular care when the battery has been in service for a long time or has just been
charged as highly explosive gas is emitted.
Ensure adequate ventilation.
10 Maintenance
10.3 Engine
No.: 9_9432 02 E
Service Manual Screw Compressor
M43
85
RAMIRENT