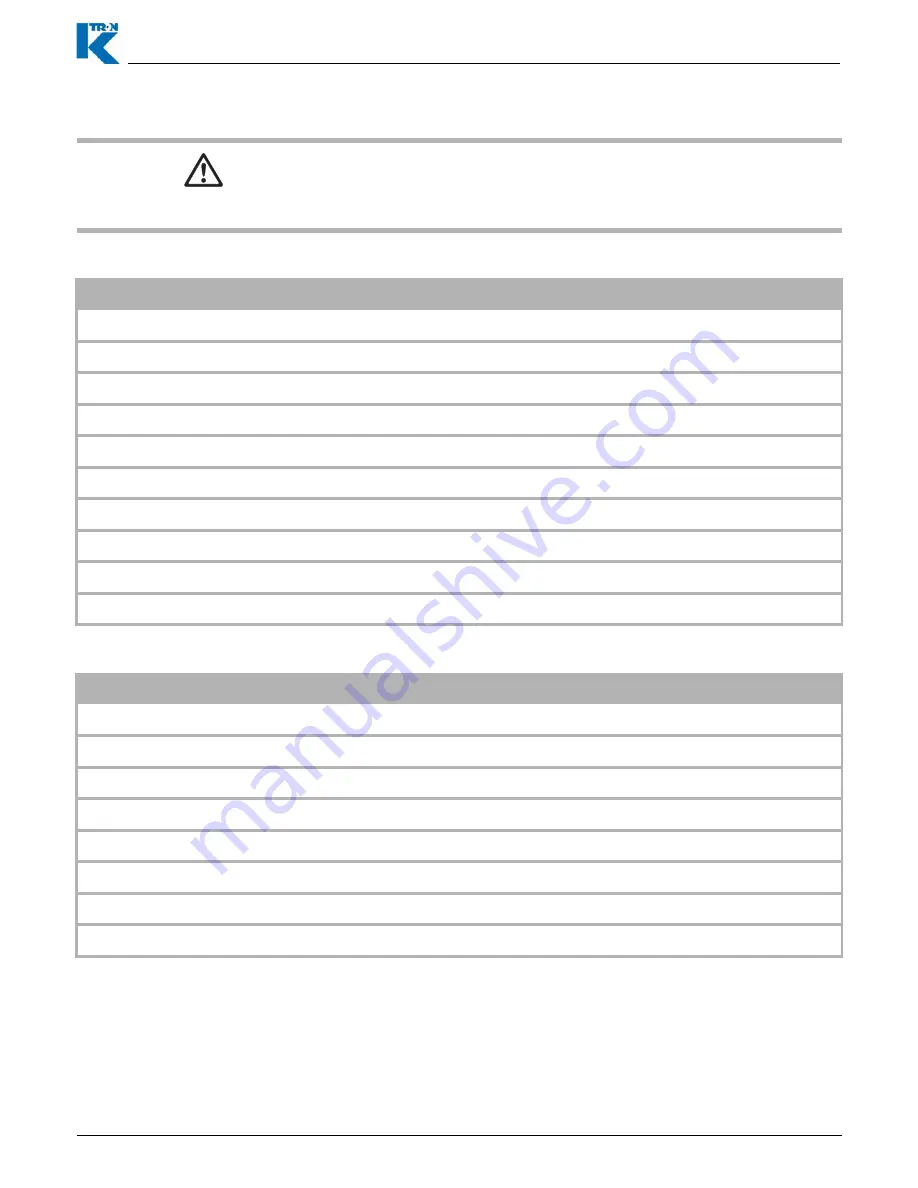
Docu-No.: 1090020601-EN Rev. 1.2.1
Page 41
Installation 4
Drive connection summary 4.10
4.10.9
Stepper drive specific connections
4.10.10 Universal stepper motor drive power - J6
4.10.11 LoPo/HiPo stepper motor drive power - J6
▲
Two stepper drive wiring configurations for J6 are used. The
Universal Stepper drive, 0000005987 is described in table
. The LoPo and HiPo stepper drives, 0000001430 and
0000004568 are described in table
Terminal
Function
Notes
J6-1
Stepper drive Phase 1(+)
Phase 1 of the stepper drive
J6-2
Stepper drive Phase 1(-)
Phase 1 of the stepper drive
J6-3
Stepper drive Phase 2(+)
Phase 2 of the stepper drive
J6-4
Stepper drive Phase 2(-)
Phase 2 of the stepper drive
J6-5
PE/GRD
Earth/ground
J6-6
PE/GRD
Earth/ground
J6-7
PE/GRD
Earth/ground
J6-8
Neutral
Neutral leg of a 115 Vac line or 230 Vac
J6-9
L2
Second leg of a 230 Vac line
J6-10
L1
Line input (hot) either 115 Vac or 230 Vac
Terminal
Function
Notes
J6-1
Stepper drive Phase 1(+)
Phase 1 of the stepper drive
J6-2
Stepper drive Phase 1(-)
Phase 1 of the stepper drive
J6-3
Stepper drive Phase 2(+)
Phase 2 of the stepper drive
J6-4
Stepper drive Phase 2(-)
Phase 2 of the stepper drive
J6-5
PE/GRD
Earth/ground
J6-6
PE/GRD
Earth/ground
J6-7
Neutral(L2)
Neutral leg of a 115 Vac line or 230 Vac
J6-8
L1
Line input (hot) either 115 Vac or 230 Vac