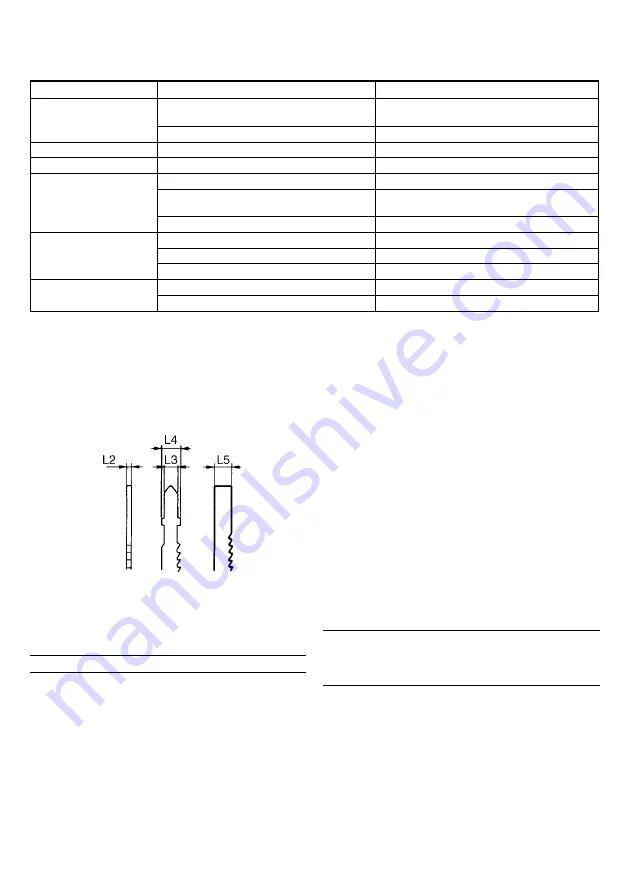
6
2. Acceptable commercial blades (Fig. 14)
This machine is designed to accept most blades
available on the open market. As illustrated in
Fig. 14, blade dimension restrictions are as follows:
䡬
Thickness : L2 ..... Less than 1.6mm
䡬
Width
: L3 ..... 6.3mm
L4 ..... 8mm
L5 ..... 7mm
NOTE
When cutting thick materials, use K-EIKO genuine blades
which have an inclination as shown in Fig. 4-A or B.
MAINTENANCE AND INSPECTION
1. Inspecting the blade
Continued use of a dull or damaged blade will result
in reduced cutting efficiency and may cause
overloading of the motor. Replace the blade with a
new one as soon as excessive abrasion is noted.
2. Inspecting the mounting screws
Regularly inspect all mounting screws and ensure
that they are properly tightened. Should any of the
screws be loose, retighten them immediately. Failure
to do so could result in serious hazard.
3. Maintenance of the motor
The motor unit winding is the very “heart” of the
power tool. Exercise due care to ensure the winding
does not become damaged and/or wet with oil or
water.
Table 1 List of Appropriate Blades
Material to be cut
Material quality
Blade No.
Lumber
General lumber
No.1 or No.31 (thick plate) or No.41 (thick
plate) or No.2 (thin plate)
Plywood
No.3 or No.6
Iron plate
Mild steel plate
No.6
Nonferrous metal
Aluminum, copper, brass
No.6
Phenol resin, melamine resin, etc.
No.4 (thick plate) or No.6 (thin plate)
Synthetic resin
Vinyl chloride, acryl resin, etc.
No.2 or No.4 (thick plate) or No.6
(thin plate)
Foamed styrol, etc.
No.2
Pulp
Cardboard, corrugated paper
No.2
Hardboard
No.5 or No.6
Fiberboard
No.6
Others
Hard rubber
No.2
Slate
No.5
4. Replacing supply cord
If the supply cord of Tool is damaged, the Tool must
be returned to K-EIKO Authorized Service Center for
the cord to be replaced.
5. Servicing
Consult an authorized Service Agent in the event of
power tool failure.
6. Service parts list
CAUTION
Repair, modification and inspection of K-EIKO Power
Tools must be carried out by an K-EIKO Authorized
Service Center.
This Parts List will be helpful if presented with the
tool to the K-EIKO Authorized Service Center when
requesting repair or other maintenance.
In the operation and maintenance of power tools, the
safety regulations and standards prescribed in each
country must be observed.
MODIFICATIONS
K-EIKO Power Tools are constantly being improved
and modified to incorporate the latest technological
advancements.
Accordingly, some parts may be changed without
prior notice.
NOTE
Due to K-EIKO’s continuing program of research and
development, the specifications herein are subject to
change without prior notice.
Fig. 14
Acceptable blades