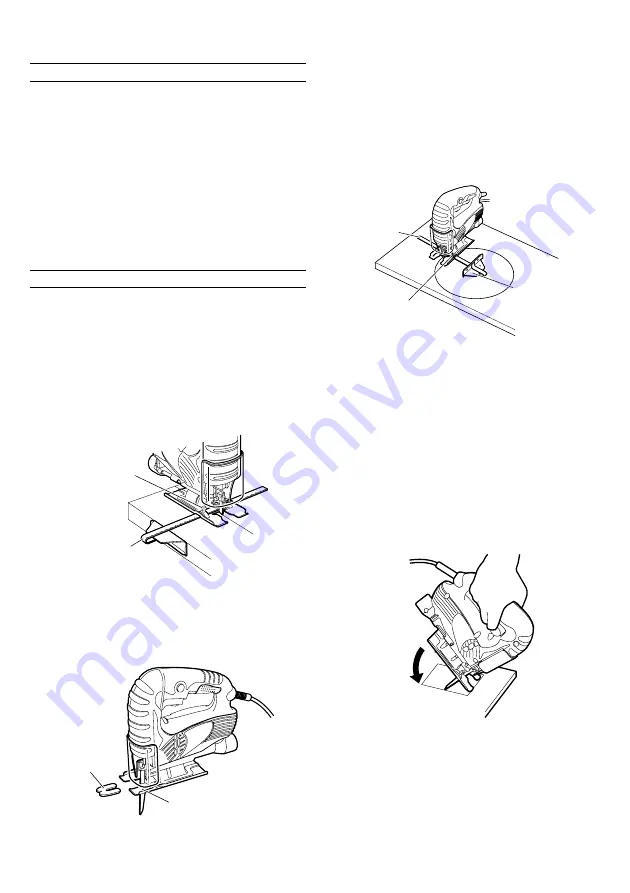
4
ADJUSTING THE BLADE OPERATING SPEED
The blade operating speed can be adjusted within a
range of 0 to 3000 min
–1
according to the degree that the
trigger switch is depressed. Select the speed appropriate
to the material being worked and/or the working
conditions.
To achieve continuous operation, pull the trigger switch
all the way back and depress the stopper. Then, turn the
speed adjustment knob to adjust the blade operating
speed as desired.
NOTE
The speed adjustment knob rotates approximately 1.5
turns. To turn the switch OFF, pull the trigger switch
again to disengage the stopper, and release the trigger
switch.
CUTTING
CAUTION
䡬
While sawing, the base must be firmly in contact with
the material surface, and the blade must be held at a
right angle. If the base becomes separated from the
material, it could cause the blade to break.
䡬
When cutting while holding the front surface, be
careful of the moving blade and hold the upper part
firmly.
1. Rectilinear cutting
(1) To ensure accurate rectilinear cutting, employ the
optional accessory guide as shown in Fig. 6.
(2) Use the splinter guard to reduce roughness of the
cutting surface of wooden materials. Attach the
splinter guard by inserting it from the front section of
the base until it clicks into place. (Fig. 7)
CAUTION
Set the base in the front position when using the
splinter guard.
2. Cutting a circle or a circular arc
To ensure efficient cutting, employ the optional
accessory guide and nail or wood screw as shown in
Fig. 8.
When mounting the guide, loosen the base bottom
screw, and shift the base as far forward as it will go.
3. Sawing curved lines
When sawing a small circular arc, reduce the feeding
speed of the machine. If the machine is fed too fast, it
could cause the blade to break.
4. Cutting metallic materials
Always use an appropriate cutting agent (spindle oil,
soapy water, etc.). When a liquid cutting agent is not
available, apply grease to the back surface of the
material to be cut.
5. Pocket cutting
(1) In lumber
Aligning the blade direction with the grain of the
wood, cut step by step until a window hole is cut in
the center of the lumber. (Fig. 9)
(2) In other materials
When cutting a window hole in materials other than
lumber, initially bore a hole with a drill or similar tool
from which to start cutting.
Fig. 6
Fig. 7
Fig. 8
Fig. 9
4mm screw (8mm)
Guide
Splinter guard
Base
Guide
4mm screw (8mm)
Nail or wood
screw