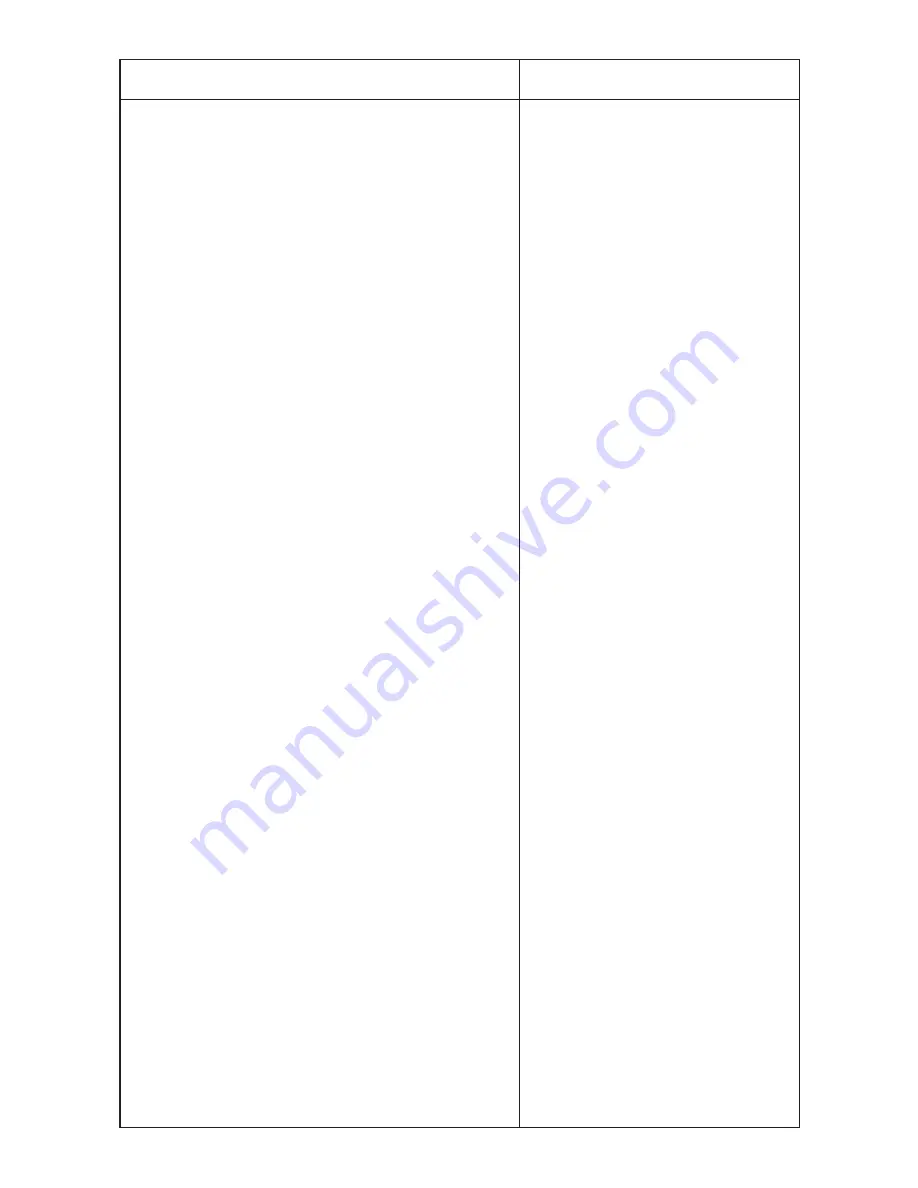
−
23
−
Disassembling and assembling of the driving shaft
(Note)
Do not disassemble the driving shaft except
when it has broken since since the motor is
built in.
Disassembling
**
Prepare before disassembling a clean board which is
not affected by magnetism and a piece of clean cloth so
that the rotor is not directly touched by hand.
1) Remove the circuit board. See the item “Circuit board”
P.16.
Tilt the sewing machine, remove the base cover and
remove the setscrews in the crank rod.
2) Loosen setscrews in the bushing, setscrews in the stator
and loosen the hand pulley.
3) Assemble again the studs and the rubber base, and raise
the sewing machine.
4) Remove setscrews in the motor cover and draw out the
whole driving shaft.
5) Put the driving shaft which has been drawn out on a clean
board which is not affected by magnetism.
**
Once again pay attention to the following matters before
disassembling the driving shaft which has been drawn
out.
1
Chech whether there is anything such as iron powder
or the like which is attracted by the magnet in the
neighbourhood.
2
Check whether there is any electronic apparatus
which is easily affected by the magnetism.
3
Prepare a piece of clean cloth to wrap the rotor.
4
Wash the hands to make them clean.
6) Loosen setscrews and draw out the encoder together with
the motor cover.
7) Draw out the stator from the driving shaft. Pressing the
driving shaft, slowly draw out the stator with force on the
board since the stator is pulled by the strong magnetism
from the rotor located inside the stator.
(Note)
If the force is quickly applied, the stator and the
rotor come off suddenly at the position where
the magnetism is lost. As a result, the parts may
be dropped. So, be careful.
8) Hold the rotor so that it is wrapped in a piece of clean
cloth, loosen the setscrew, and draw it out from the driving
shaft.
Wrap the rotor which has been drawn out in a piece of
cloth.
(Note)
The black section of the rotor is a strong
magnet.
If there is a screwdriver or a screw in the
neibourhood, it is attracted to the manet with
force. As a result, it may be broken by the shock.
So, be careful.
9) Loosen the setscrew in the screw gear, and remove
bushings, right and left, thrust bearing and hand pulley.
Assembling
1) Install the screw gear.
(Clearance : 4 to 4.2 mm)
2) Enter the thrust bearing and the
bushings, and install the hand pulley.
3) Install the rotor. Hold it so that the
screw section comes out and install it
so that there is no clearance in the
thrust direction.
4) In this state, enter the rotor in the
machine bed.
Do not take the cloth covering the rotor.
5) Next, enter the stator. Set the direction
of the cord as shown in the figure and
slowly enter the stator while pressing
the driving shaft. When the magnetism
of the rotor works, the stator enters
with force as if it is absorbed. On the
contrary, the driving shaft tries to jump
out. Accordingly, hold the driving shaft
by hand.
6) Install the motor cover.
Keep the setscrew in the encoder held
loosened.
7) Tilt the sewing machine.
8) First, determine the position of the
bushing on the right-hand side.
Fix it so that the dimension from the
end face of the machine bed is 7.7 mm.
9) Next, fix the bushing on the left-hand
side while making the driving shaft
come in contact with the bushing on
the right-hand side.
10) Fix the crank rod.
11) Remove the studs and the rubber base
and again assemble them together
with the base cover and the packing.
At this time, move the sensor slit attached
to to the stepping motor.
For the position of the sensor slit, refer
to the figure on P.19.
Cautions in disassembling
Cautions in assembling