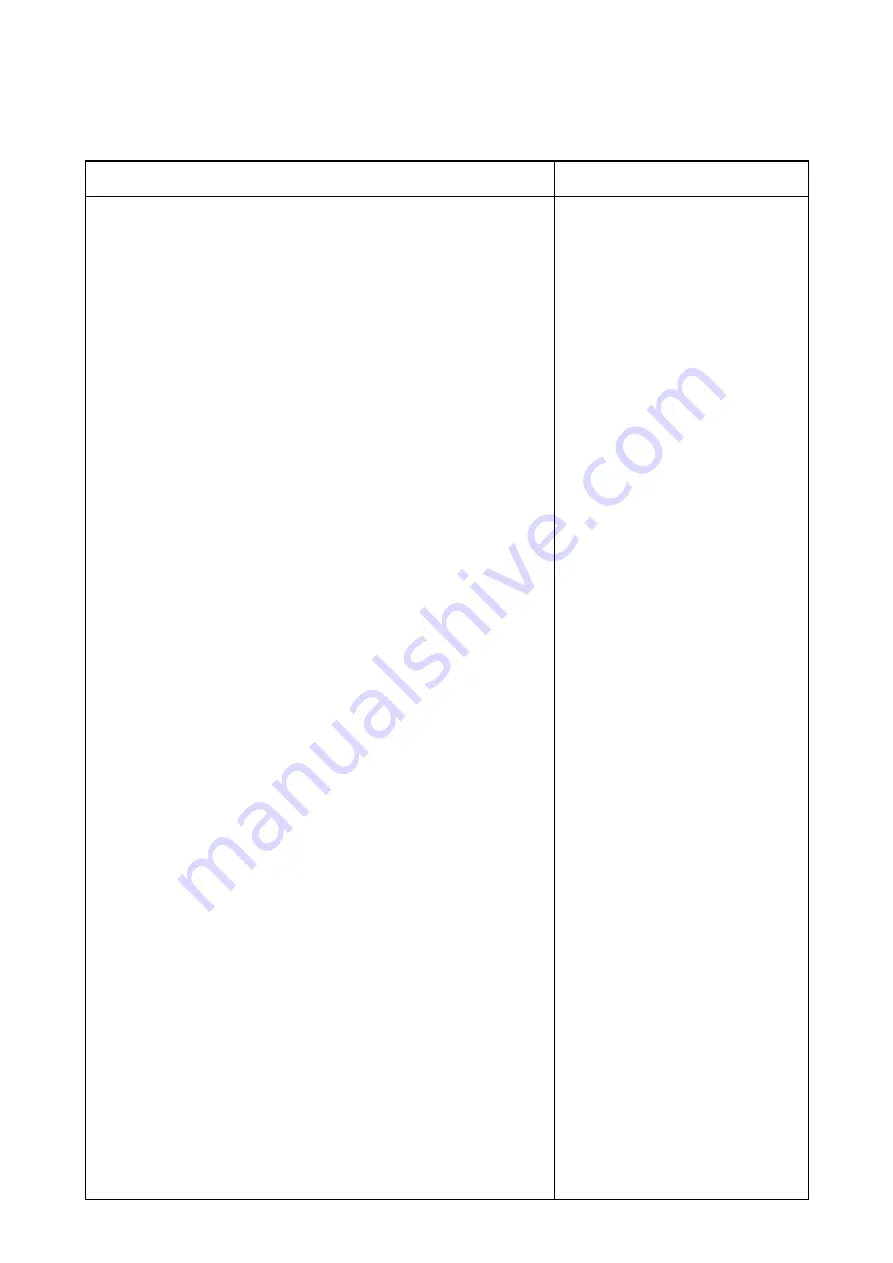
– 9 –
Adjustment procedures
Results of Improper adjustment
1) Height of the needle bar
1. Set the stitch dial to “0”.
2. Loosen setscrews
1
of the face plate to remove the face plate
2
.
3. Turn the handwheel to bring so that needle bar
3
is raised
from the lowest dead point of its stroke to dimension A.
4. Loosen clamping screw
4
of the needle bar holder.
At this time, loosen the screw to such an extent that needle bar
3
moves up and down by hand since needle bar
3
drops if
the screw is fully loosened.
5. Move needle bar
3
to adjust so that the distance from the top
end of the needle eyelet to blade point of the hook
7
becomes
dimension B. Then tighten clamping screw
4
of the needle bar
holder.
2) Needle-to-blade point of hook timing
1. Set the stitch dial to “0”.
2. Loosen clamping screw
5
of the lower shaft set collar.
3. Turn the handwheel and when dimensions A and B are approx
-
imately obtained, loosen two setscrews
8
of the hook shaft
base. Then move the hook shaft base
9
to the right or left
to adjust so that the clearance between needle
6
and blade
point of the hook
7
is dimension C. Then securely tighten two
setscrews
8
of the hook shaft base.
4. Turn the handwheel to bring so that needle bar
3
is raised
from the lowest dead point of its stroke to dimension A. At this
time, turn the hook
7
in its normal rotational direction so that
center of the needle
6
aligns with blade point of the hook
7
.
5. Tighten clamping screw
5
of the lower shaft set collar.
6. Turn the handwheel to bring so that needle bar
3
is raised
from the lowest dead point of its stroke to dimension A. At this
time, loosen clamping screw
4
of the needle bar holder to ad-
just so that the distance from the top end of the needle eyelet
to blade point of the hook
7
is dimension B. Then tighten again
the clamping screw
4
of the needle bar holder.
7. Set the stitch dial to the maximum and check that needle
6
does not come in contact with blade point of the hook
7
. (For
the dimension, refer to the respective models in the list.)
3) Adjusting the hook needle guard
When a hook has been replaced, be sure to check the position of
the hook needle guard
!0
.
1. As the standard position of the hook needle guard
!0
, the hook
needle guard
!0
must push the side face of needle
6
to lean
the needle by 0.05 to 0.2 mm away from its straight position.
2. If the state of the hook is not as shown above, fit the hexagon
wrench
!2
into the needle guard adjusting screw
!1
and adjust
as follows:
1) To bend the hook needle guard
!0
in direction
d
, turn the
needle guard adjusting screw
!1
in direction
D
.
2) To bend the hook needle guard
!0
in direction
e
, turn the
needle guard adjusting screw
!1
in direction
E
.
o
Stitch skipping or thread break-
age will result.
o
Loose stitches will result.
海外講習会用121122 LU-2810(-7)̲EM
Summary of Contents for LU-2810 Series
Page 57: ... 45 1 1 1 1 1 2 NEEDLE BAR COMPONENTS 海外講習会用121122 LU 2810 7 EM ...
Page 58: ... 46 1 1 3 HOOK OPENNER COMPONENTS 海外講習会用121122 LU 2810 7 EM ...
Page 64: ... 52 1 1 1 1 1 1 1 11 THREAD TRIMMING COMPONENTS FOR LU 2810 7 海外講習会用121122 LU 2810 7 EM ...
Page 65: ... 53 3 3 3 3 2 2 12 THREAD TENSION COMPONENTS 海外講習会用121122 LU 2810 7 EM ...
Page 66: ... 54 3 2 2 3 2 2 13 TENSION RELEASE COMPONENTS FOR LU 2810 7 海外講習会用121122 LU 2810 7 EM ...
Page 67: ... 55 3 3 3 3 14 BOBBIN WINDER COMPONENTS 海外講習会用121122 LU 2810 7 EM ...
Page 83: ...海外講習会用121122 LU 2810 7 EM ...