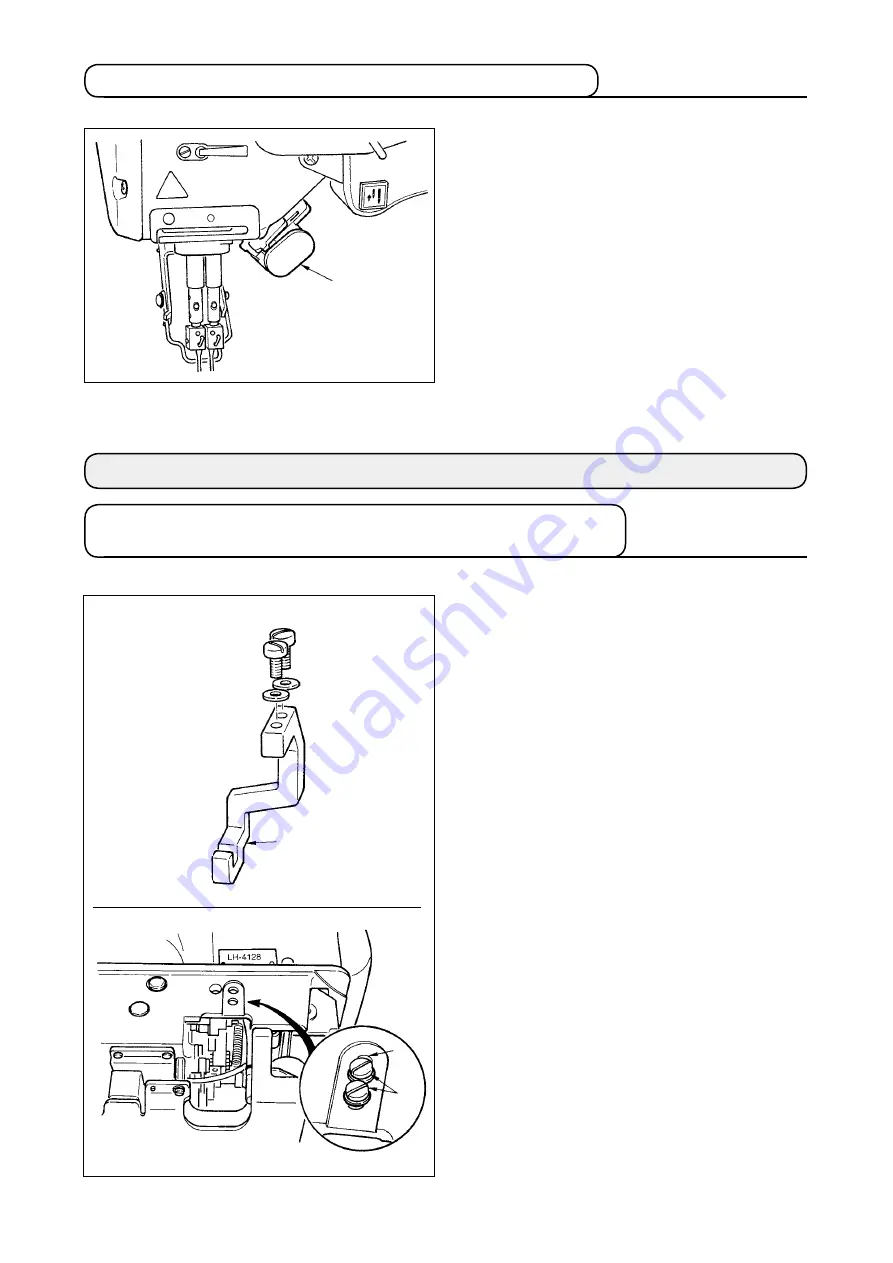
– 25 –
) Prepare the gauge for bottom feed.
Temporarily set needle rocking rod fixing
base
1
contaned n the accessores to hole
2
of the machne frame wth washers
3
and
setscrews
4
.
(1) How to use
) Depress swtch
1
, and the machne wll
mmedately run n the reverse drecton.
2) Reverse sttch s made as long as you keep
depressng the swtch lever.
3) Release the swtch lever for forwatd sewng.
5-6. One-touch reverse feed switch lever (for touch-back)
6. MAINTENANCE
6-1. Changing procedure to bottom feed and the adjustment
(LH-4128 without thread trimmer only)
1
1
2
34