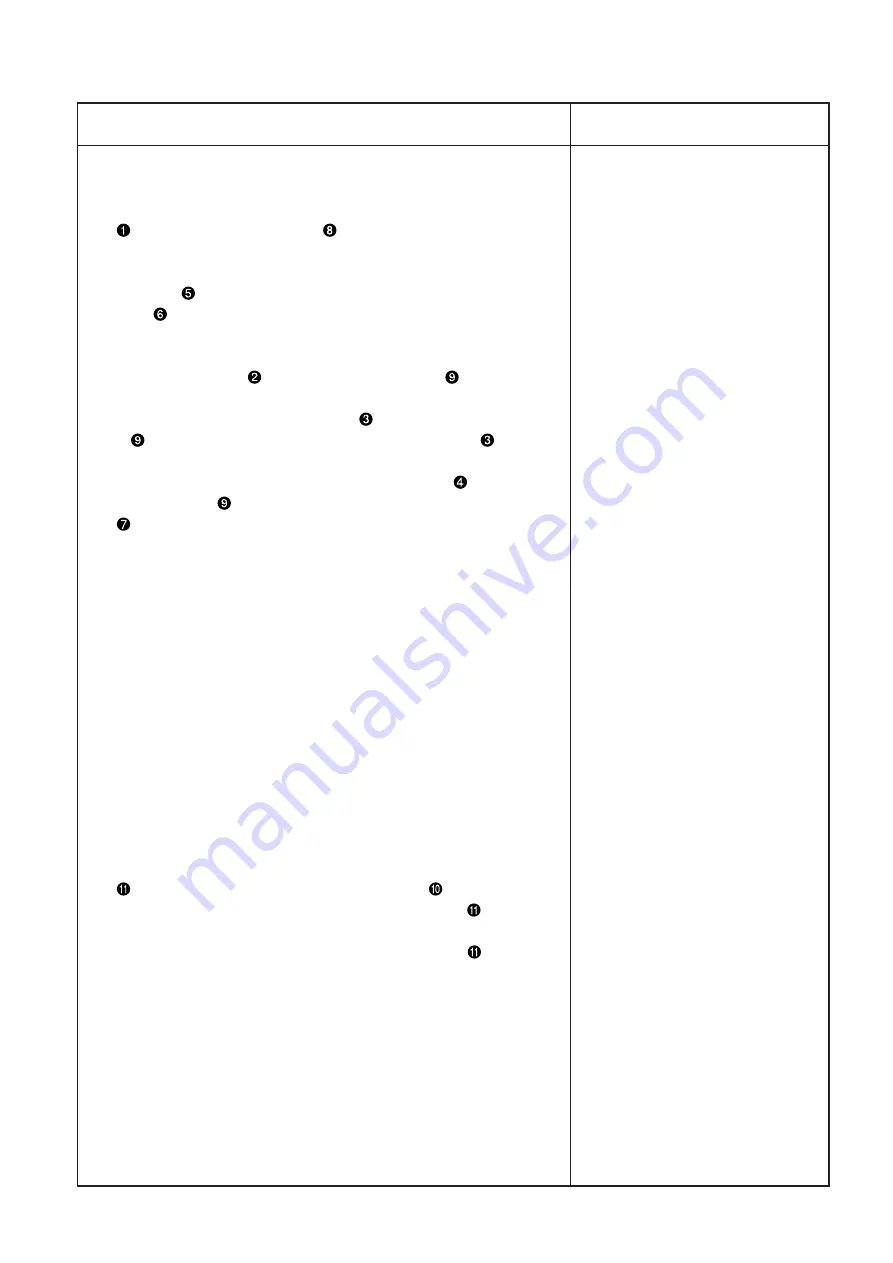
– 58 –
1. Adjustment of laser beam parallelism of the marking light
(1) Adjustment of the horizontal line
o
If parallelism of the laser beam is not secured, loosen the setscrew
and turn the marking light A
for adjustment.
o
In the case of adjustments at the panel beyond the range of origin
correction (
±
25mm), dislodge the marking light cover and loosen the
setscrew
of the rear sensor plate. In this state, turn the sensor
plate
for adjustment.
(2) Adjustment of vertical line position
o
If parallelism of the vertical laser beam is not secured (See Fig. A),
loosen the setscrew
and turn the marking light B
for adjustment.
o
If the vertical laser beam has deviated in the right or left direction
(See Fig. B), loosen the hinge screw
and adjust the marking light
B
by turning it around the center of the hinge screw
.
o
If the radiation range (300mm from the needle center) of the vertical
laser beam is not secured, loosen the setscrew
and turn the
marking light B
for adjustment around the center of the fixed shaft
.
2. Adjustment of the light value of the marking light
(1) The light value of the marking light is adjusted with the volume control
located on the rear side of the marking light
.
o
The laser beam is lightened when the volume control
is turned to
the right.
o
The laser beam is darkened when the volume control
is turned to
the left.
Adjustment Procedures
Results of Improper Adjustment
Summary of Contents for APW-895
Page 14: ...7 Adjusting the bobbin thread trimming knife 9 A B Standard Adjustment ...
Page 22: ...15 Wiper adjustment 17 A B C D E F 5 1mm 21 1mm Standard Adjustment 1 mm 0 0 5 ...
Page 60: ...20 Pedal and related sections 55 A B Standard Adjustment B A ...
Page 66: ... 61 1 Installation of the shim bracket 2 SA 118 shim unit Standard Adjustment ...
Page 68: ... 63 Adjustment of interlining clamp parallelism Standard Adjustment ...
Page 70: ...3 SA 119 suction unit 65 Standard Adjustment ...
Page 72: ... 67 Section A Standard Adjustment ...
Page 74: ... 69 Section A Standard Adjustment Section B ...
Page 151: ... 146 ...
Page 152: ... 147 ...
Page 153: ... 148 ...
Page 154: ... 149 ...
Page 155: ... 150 ...
Page 158: ... 153 3 Spots where grease adhesive agents are used EXTERIORS A JUKI Grease A A A ...
Page 160: ... 155 NEEDLE THREAD TRIMMER COMPONENTS A JUKI Grease A C Locktight 242 A A C A ...
Page 161: ... 156 THREAD TENSION WIPER COMPONENTS A JUKI Grease A A A ...
Page 162: ... 157 LOWER THREAD COMPONENTS A A C A A A C A JUKI Grease A C Locktight 242 A ...
Page 163: ... 158 CENTER KNIFE COMPONENTS A A A A A C A A A C C A A JUKI Grease A C Locktight 242 ...
Page 164: ... 159 LOWER SHAFT COMPONENTS A JUKI Grease A G Three Bond 1373N G A A A A ...
Page 165: ... 160 HOOK DRIVING SHAFT LEFT COMPONENTS A JUKI Grease A A A A A A ...
Page 166: ... 161 HOOK DRIVING SHAFT RIGHT COMPONENTS A JUKI Grease A A A A A A ...
Page 167: ... 162 BACK TUCK COMPONENTS A JUKI Grease A G Three Bond 1373N G A ...
Page 168: ... 163 CLAMP FOOT UNIT 1 B B B C B B B B C B JUKI Grease B C Locktight 242 ...
Page 169: ... 164 CLAMP FOOT UNIT 2 B JUKI Grease B C Locktight 242 B B B B B C B B B ...
Page 170: ... 165 CLAMP FOOT UNIT 3 B JUKI Grease B C Locktight 242 B C B B B B B B ...
Page 171: ... 166 CLAMP FOOT FEED UNIT B JUKI Grease B D Locktight 243 D D B B B ...
Page 173: ... 168 BINDER UNIT B JUKI Grease B D Locktight 243 D B B B B B B ...
Page 174: ... 169 MARKING LIGHT UNIT D B D B F B B JUKI Grease B D Locktight 243 F Locktight 641 ...
Page 176: ... 171 FRAME AND COVER COMPONENTS 2 B JUKI Grease B B ...
Page 179: ... 174 B JUKI Grease B G Three Bond 1373N AUTOMATIC INTERLINING FEEDER UNIT SA 120 B B G B B G ...
Page 180: ... 175 ROLLER STACKER UNIT SP 47 B JUKI Grease B G Three Bond 1373N B B B B B G B G G B B ...
Page 206: ... 201 MEMO ...