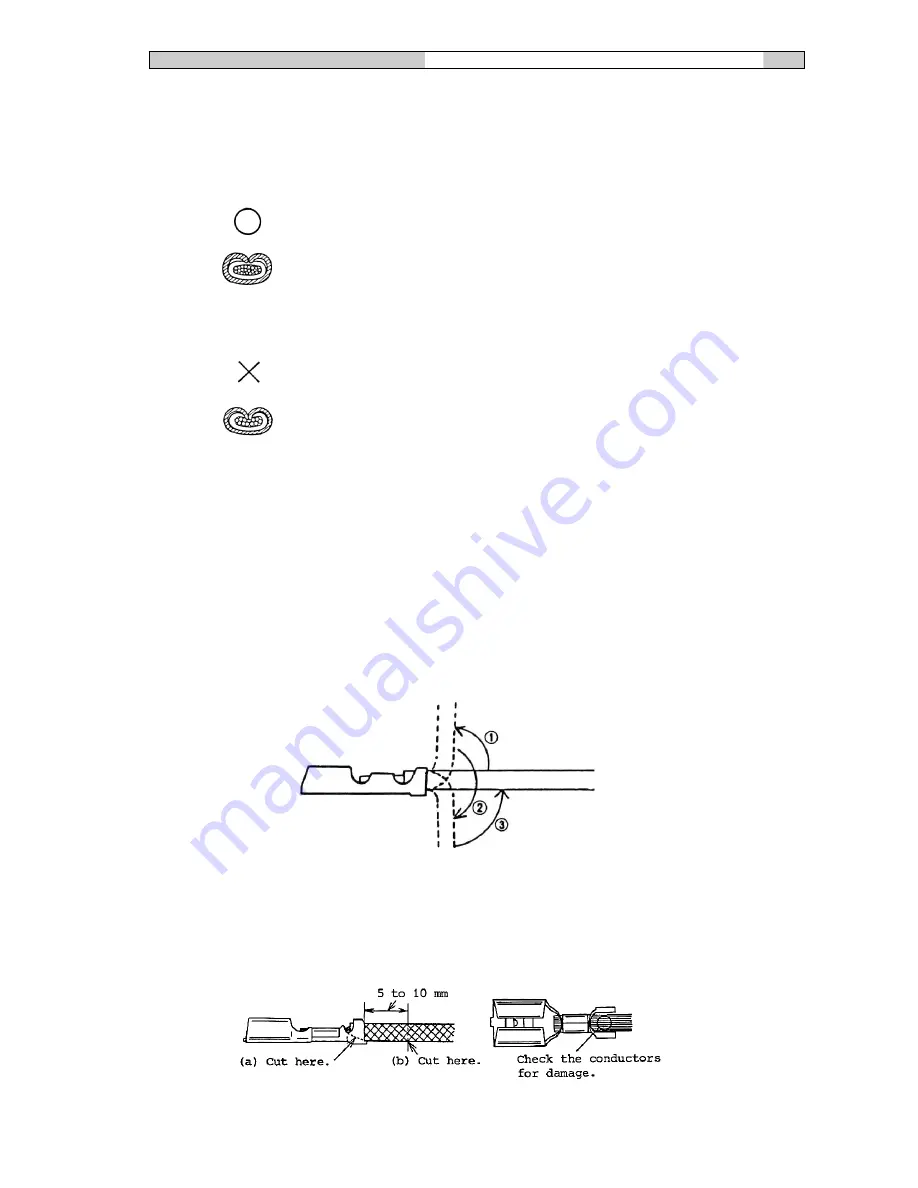
JST
CMK-R INDUSTRY STANDARD APPLICATOR
H:\0 - Quality Documents\2 Department\Tech Serv\Application tooling\Applicators and Die sets\TS142-01
CMK-R Manual.doc
24
999
Checking for correct crimping:
Following the items described below to check that the insulation barrel is correctly
crimped.
(1) Check that the wire insulation does not slip when the wire is bent in the order (1, 2
and 3) shown the right.
(2) Cut off the insulation barrel at the (a) portion and cut off the wire at the (b)
portion. Remove the wire insulation and check the wire conductors for damage.
Correct
- The barrel edges firmly grip the insulation.
Excessive crimping
- The barrel edges cut into the strands.