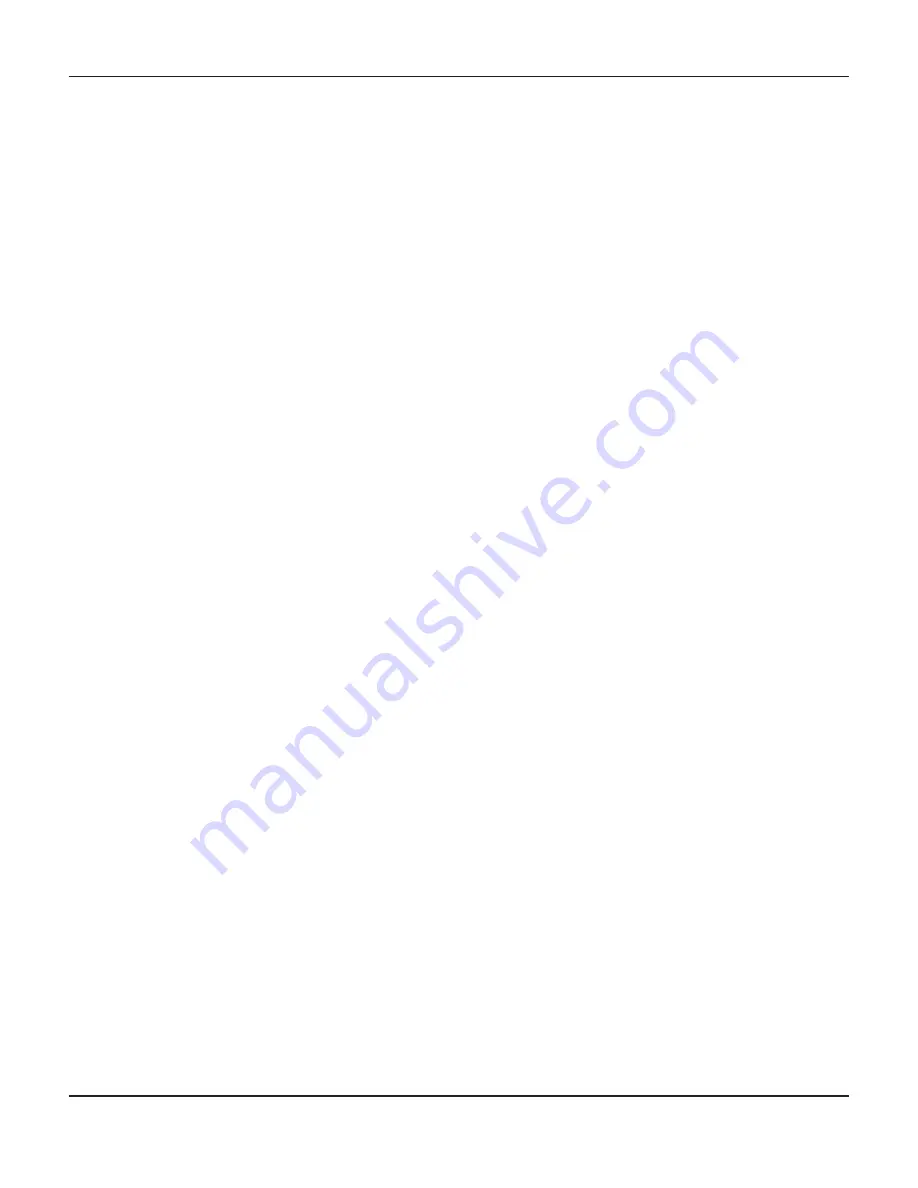
-3-
Adding Packing Rings Continued,
5.
After replacing the packing flange and packing
follower, tighten the packing flange nuts
(Figure 2, Key 16) just far enough to prevent
leakage under operating conditions.
6.
If the valve-actuator stem connection was
disassembled during this process, refer
to the actuator manual for reassembly
instructions.
7.
While returning the valve to service, monitor for
leakage around the packing follower. If required,
retighten the packing flange nuts.
Replacing Packing
Note: Prior to performing this procedure, isolate
the control valve from all line pressure and release
the pressure from both sides of the valve. Drain the
process media and release all pressure from the
actuator. Practice lockout procedures during the
operation.
1.
Remove the operating lines from the actuator as
well as any leak-off piping from the bonnet.
2.
Disconnect the stem connector and unscrew the
yoke locknut (Figure 2, Key 17) to remove the
actuator from the valve body.
3.
Loosen the packing on the valve stem by
unscrewing the packing flange nuts (Figure 2,
Key 16). Remove all travel indicator parts and
stem locknuts from the valve stem threads.
Note: When lifting the bonnet (Figure 2, Key 18), it is
very important to ensure that the valve plug and stem
assembly remain in the valve and on the seat. If the
assembly were to drop out after being partially lifted,
damage to the seating surfaces would result. Parts
are also easier to handle in this way.
4.
Remove the hex nuts (Figure 4, Key 39) holding
the bonnet and body together, and lift
the bonnet off of the valve stem.
5.
When lifting the bonnet, if the valve plug and
stem assembly begin to lift as well, use a brass
or
lead
hammer
and lightly tap on the end of the stem to
release them.
6.
Place the bonnet on a protective surface to pre-
vent damage to the surface of the bonnet
gasket.
7.
Remove the bonnet gasket (Figures 3 and 4,
Key 33) and cover the valve body opening in or
der to prevent debris from entering the
body cavity and to protect the gasket surface.
8. Remove the following parts (Figure 2):
a.
packing flange nuts (Key 16)
b.
packing flange (Key 20)
c.
upper wiper (Key 2)
d.
packing follower (Key 3)
9.
Use a rounded rod to push out the remaining
packing parts from the body side of the
bonnet. Be careful not to scratch the packing
box wall. Clean the packing box and metal
packing parts.
10.
Inspect the valve stem threads and packing
box surfaces for any edges which might
cut the packing. Any defects could create leak
ing in the packing box and damage to
the new packing. If any surface nicks or
burrs cannot be improved by light sanding
replace the damaged parts.
11.
Remove the covering which protects the body
covering and install a new bonnet
gasket (Figures 3 and 4, Key 33). Ensure that
the gasket seating surfaces are clean
and smooth.
Note: When the tightening procedures in Step 13 are
completed properly, the spiral wound gasket (Figures
3 and 4, Key 35) will be compressed enough to load
and seal the seat ring gasket (Figures 3 and 4, Key
36) and compress the edge of the bonnet gasket
(Figures 3 and 4, Key 33) and seal the body-to-bonnet
joint.
The lubricated stud bolt nuts (Figure 4, Key 39) can be
identified by the black film that coats the nut threads.
The bolting procedures in Step 13 will ensure that the
bolting threads are clean, and will evenly tighten the nuts
onto the studs in a crisscross pattern. Be sure to follow
the crisscross pattern since the tightening of one spiral
wound gasket may loosen an adjacent nut. Continue
repeating the pattern until each nut is tight, creating the
body-to-bonnet seal. Repeat this torquing procedure
once the operating temperature has been reached.
M
ark
EW S
EriES
G
lobE
S
tylE
C
ontrol
V
alVES