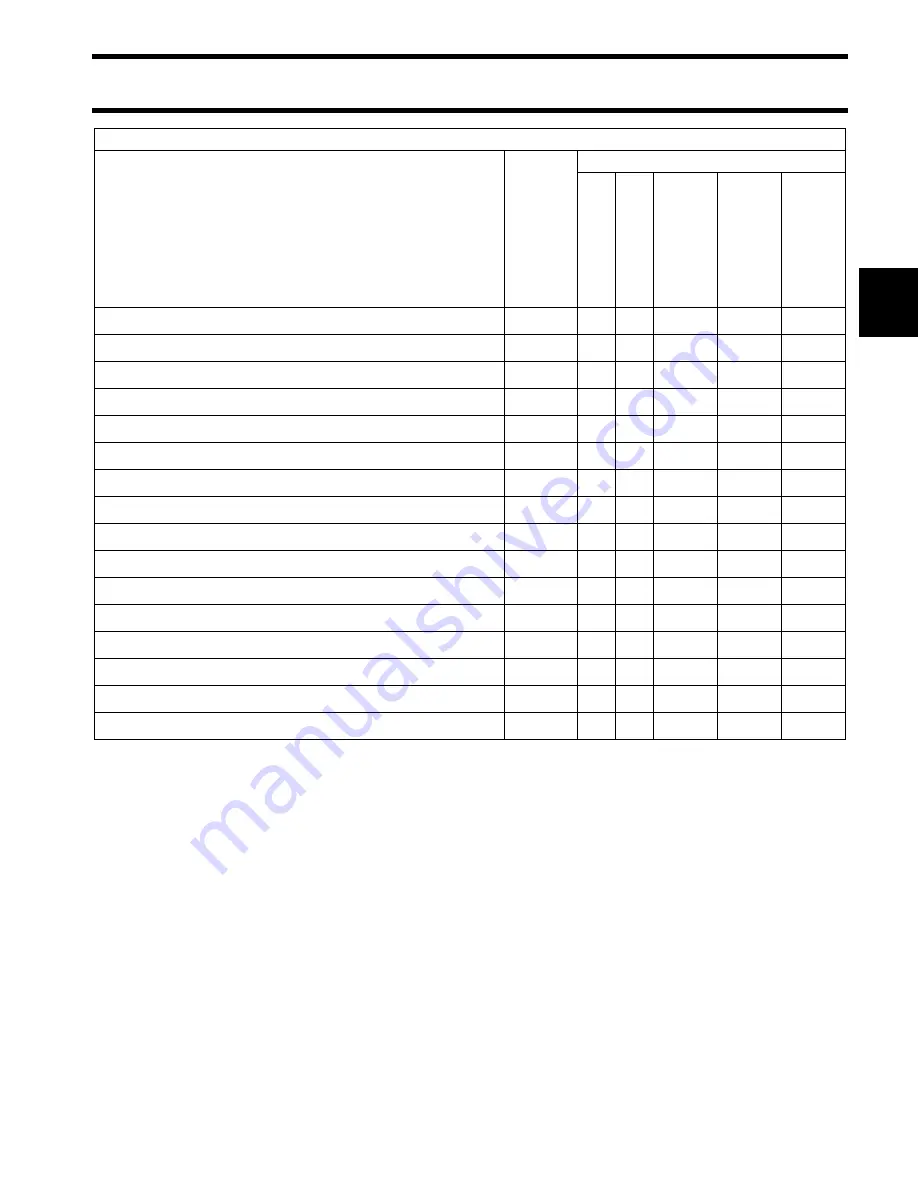
MAINTENANCE
INSPECTION AND MAINTENANCE SCHEDULE
39
3
Crankcase oil, replace
(2)
H
3
3
Oil filter, replace
3
3
Valve tappet clearance, inspect
(3)
3
3
Engine upper and lower motor covers, clean and wax
3
Starter pinion shaft, inspect and lubricate
F
3
Gearcase lubricant, inspect fill level and condition of lube
B
3
Propeller shaft, inspect and lubricate
D
3
Spark plugs, replace
(3)
3
Decarbonize
G
3
Operator’s Guide, review
3
Breather and fuel line, replace
3
Carburetor, inspect
3
Driveshaft splines, inspect and lubricate
E
3
Fuel filter, replace
3
Ignition timing, inspect
3
Water pump, inspect and replace
3
(1) Also recommended at 10-Hour Inspection
(2) Replace every 100 hours or annually if
Ultra 4-Stroke
oil is not used.
(3) Emission-related component
A
Evinrude/Johnson
Anti-Corrosion Spray or
Evinrude/Johnson
“6 in 1” Multi-Purpose Lubricant
B
HPF XR
Gearcase Lubricant
C
Power Trim/Tilt and Power Steering Fluid
D
Triple-Guard
Grease
E
Evinrude/Johnson Moly Lube
F
Starter Bendix Lube Only
G
Evinrude/Johnson
Engine Tuner
H
Evinrude/Johnson Ultra 4-Stroke
synthetic blend oil
Engine Maintenance and Inspection Schedule
Description
Engine
Care
Product
Frequency
Each Use
10-Hour
Inspection
Every 50 Hours
or 6
mon
ths
Every 100 Hours
or An
nually
Every 200 Hours
or Bian
nually