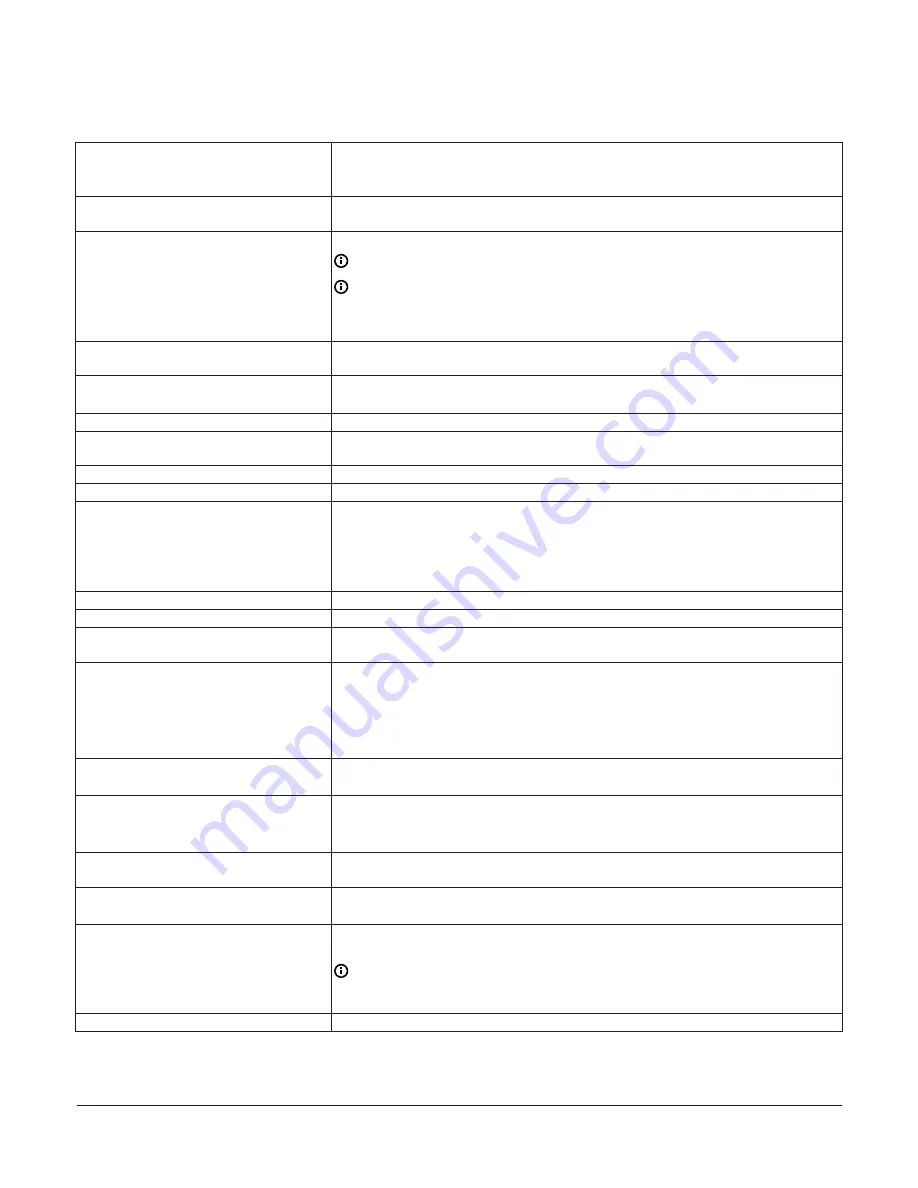
Technical specifications
Table 14: Technical specifications
Product Code Numbers
M4-CGM09090-0
General Purpose Application Controller
Includes: MS/TP (and N2) communication; 18 points (7 UI, 2 BI, 4 CO, 2 AO, 3 BO); real-
time clock; 32-bit microprocessor; 24VAC input
Power Requirement
24 VAC (nominal, 20 VAC minimum/30 VAC maximum), 50/60 Hz, Power Supply Class 2
(North America), Safety Extra-Low Voltage (SELV) (Europe)
Power Consumption
14 VA maximum
Note:
The USB feature is not currently supported.
Note:
The VA rating does
not
include any power supplied to the peripheral devices
connected to Binary Outputs (BOs) or Configurable Outputs (COs), which can
consume up to 12 VA for each BO or CO; for a possible total consumption of an
additional 84 VA (maximum).
Power Source
+15 VDC power source terminals provide 100 mA total current. Quantity 2 located in
Universal IN terminals - for active (3-wire) input devices
Ambient Conditions
Operating:
0°C to 50°C (32°F to 122°F); 10% to 90% RH noncondensing
Storage:
-40°C to 80°C (-40°F to 176°F); 5% to 95% RH noncondensing
Network Engines
All network engine model types
Communications Protocol
BACnet MS/TP; N2. Wireless also supported (at FC Bus and for Sensors) with additional
hardware.
Device Addressing for BACnet MS/TP
Decimal address set via three rotary switches; valid controller device addresses 4-127
Device Addressing for N2
Decimal address set via three rotary switches: valid controller device addresses 1-254
Communications Bus
BACnet MS/TP (default); N2
3-wire FC Bus between the supervisory controller and equipment controllers
4-wire SA Bus between equipment controller, network sensors and other sensor/actuator
devices, includes a lead to source 15 VDC supply power (from equipment controller) to
bus devices.
Processor
RX64M Renesas
®
32-Bit microcontroller
Memory
16 MB flash memory and 8 MB SDRAM
Real-Time Clock Backup Power Supply
Super capacitor maintains power to the onboard real-time clock for a minimum of 72
hours when supply power to the controller is disconnected.
Input and Output Capabilities
Universal Inputs:
Defined as 0–10 VDC, 4–20 mA, 0–600k ohms, or Binary Dry Contact
Binary Inputs:
Defined as Dry Contact Maintained or Pulse Counter/Accumulator Mode
Configurable Outputs
Defined as 0-10 VDC or 24 VAC Triac BO
Analog Outputs:
Defined as 0–10 VDC or 4–20 mA
Binary Outputs:
Defined as 24 VAC Triac (external power source only)
Universal Input (UI) Resolution/ Analog
Output (AO) Accuracy
Input:
24-bit Analog to Digital converter
Output:
+/- 200 mV accuracy in 0–10 VDC applications
Terminations
Input/Output:
Pluggable Screw Terminal Blocks
SA/FC Bus and Supply Power:
4-Wire and 2-Wire Pluggable Screw Terminal Blocks
SA/FC Bus Port:
RJ-12 6-Pin Modular Jacks
Mounting
Horizontal on single 35 mm DIN rail mount (recommended), or screw mount on flat
surface with three integral mounting clips on controller
Housing
Enclosure material:
ABS and polycarbonate UL94 5VB; Self-extinguishing
Protection Class: IP20 (IEC529)
Dimensions (Height x Width x Depth)
150 mm x 190 mm x 44.5 mm (5-7/8 in. x 7-1/2 in. x 2-1/8 in.) including terminals and
mounting clips
Note:
Mounting space requires an additional 50 mm (2 in.) space on top,
bottom, and front face of controller for easy cover removal, ventilation, and wire
terminations.
Weight
0.5 kg (1.1 lb)
M4-CGM General Purpose Application Controllers Installation Guide
25