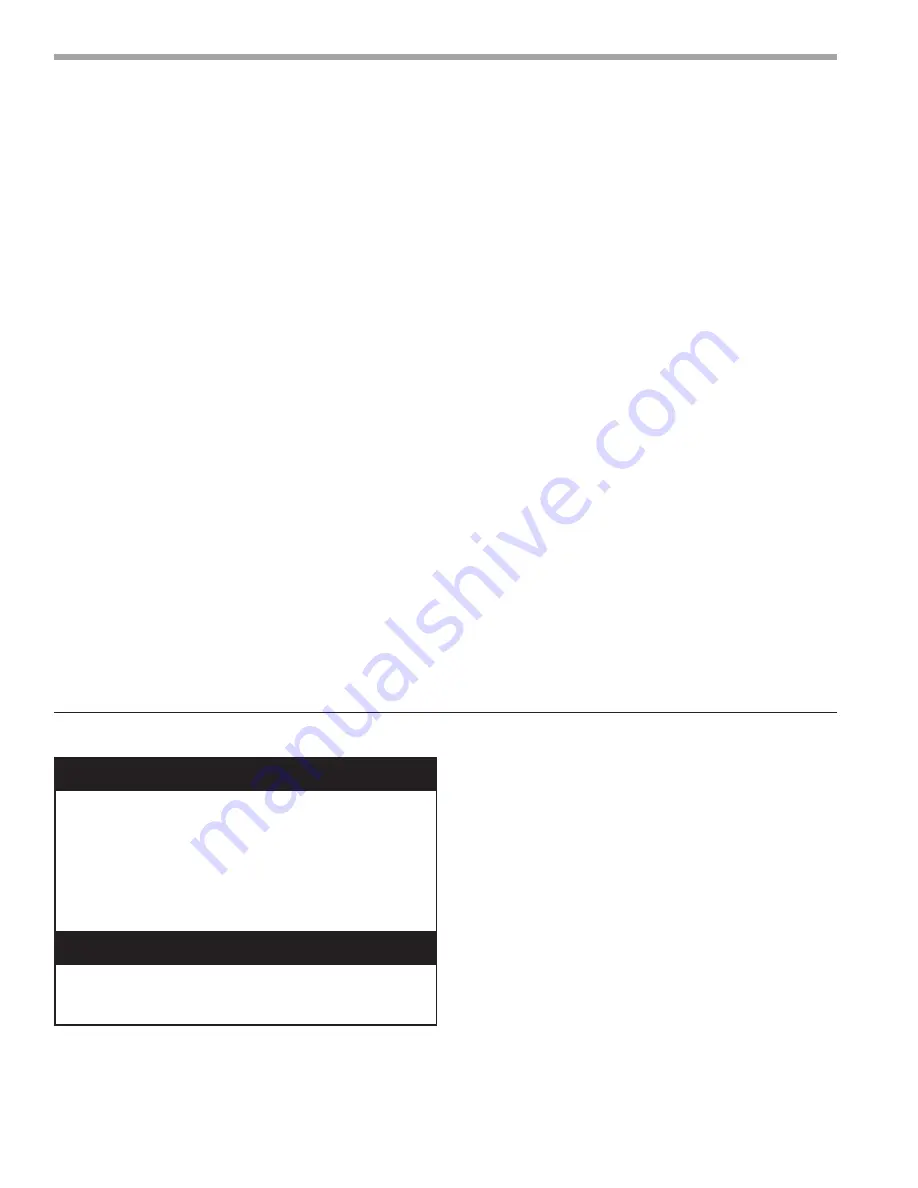
W A T E R - S O U R C E H E A T P U M P S
JRE-Series
R e v. : A u g u s t 1 9 , 2 0 2 0
I n s t a l l a t i o n , O p e r a t i o n , M a i n t e n a n c e
38
Unit System Checkout
•
Voltage:
Ensure that voltage is within the utilization
range specifications of the unit compressor and fan
motor.
•
System Water Temperature:
Ensure that it is within
an acceptable range to facilitate start-up. (When
conducting this check, also verify proper heating and
cooling setpoints.)
•
System Water pH:
Verify system water acidity. (pH =
7.5 or 8.5) Proper pH promotes the longevity of hoses
and heat exchangers.
•
System Flushing:
Properly clean and flush system
periodically. Ensure that all supply and return hoses
are connected end-to-end to facilitate system flushing
and prevent fouling of the heat exchanger by system
water. Water used in the system must be of potable
quality and clean of dirt, piping slag, and chemical
cleaning agents.
•
Closed-Type Cooling Tower or Open Tower with
Heat Exchanger:
Check equipment for proper
temperature set points and operation.
•
Water Flow Rate to Heat Pump:
System is balanced.
•
Standby Pump:
Verify that the standby pump is
properly installed and in operating condition.
•
Control Box:
Tighten/check all electrical connections.
Ensure transformer is wired on correct voltage TAP
(208 - 230 Volt only).
•
Access Panels:
Assure that all access panels in the
filter and fan section are securely closed.
•
Air Dampers:
Assure that all air dampers are
properly set.
•
System Controls:
To ensure that no catastrophic
system failures occur, verify that system controls are
functioning and that the sequencing is correct.
•
Freeze Protection for Water System:
Verify that
freeze protection is provided for the building loop
water system when outdoor design conditions require
antifreeze. Inadequate freeze protection can lead to
expensive tower and system piping repairs.
•
System Water Loop:
Verify that all air is bled from
the system. Air in the system impedes unit operation
and causes corrosion in the system piping.
•
Unit Filters:
To avoid system damage, ensure that the
unit filter is clean.
•
Unit Fans:
Manually rotate fans to assure free
rotation. Ensure that fans are properly secured to the
fan shaft. Do not oil fan motors on start-up since they
are lubricated at the factory.
•
System Control Center:
To ensure control of the
temperature set-points for operation of the system’s
heat rejector and boiler (when used), examine the
system control and alarm panel for proper installation
and operation.
•
Miscellaneous:
Note any questionable aspects of the
installation.
1. Adjust all water valves to their full open position. Turn
on the line power to all heat pump units.
2. Operate each unit in the cooling cycle. Room
temperature should be approximately 70° to 75° F
DB, and 61° to 65° F WB. Loop water temperature
entering the heat pumps should be between 60° F
and 110° F. When the unit is operating in the cooling
mode under AHRI conditions, the leaving water
temperature is approximately 10° F warmer than the
entering water temperature at 3 GPM / ton.
a. Adjust the unit thermostat to the coolest position.
If the unit has a MCO thermostat, set the selector
switch to cool. Both the fan and compressor
should run. For heat pumps with ACO, adjust the
cooling set point to a temperature at least 3° F
below room temperature.
b. Check for cool air delivery at the unit grille within
a few minutes after the unit has begun to operate.
List the identification number of any machines
that do not function.
�
WARNING!
�
WARNING!
When the disconnect switch is closed, high
voltage is present in some areas of the electrical panel.
Exercise caution when working with energized equipment.
UNIT START-UP
WARNING!
Polyolester Oil, commonly known as POE oil, is
a synthetic oil used in many refrigeration systems including
those with HFC-410A refrigerant. POE oil, if it ever comes
in contact with PVC or CPVC piping, may cause failure of
the PVC/CPVC. PVC/CPVC piping should never be used
as supply or return water piping with water source heat
pump products containing HFC-410A as system failures and
property damage may result.
�
WARNING!
�