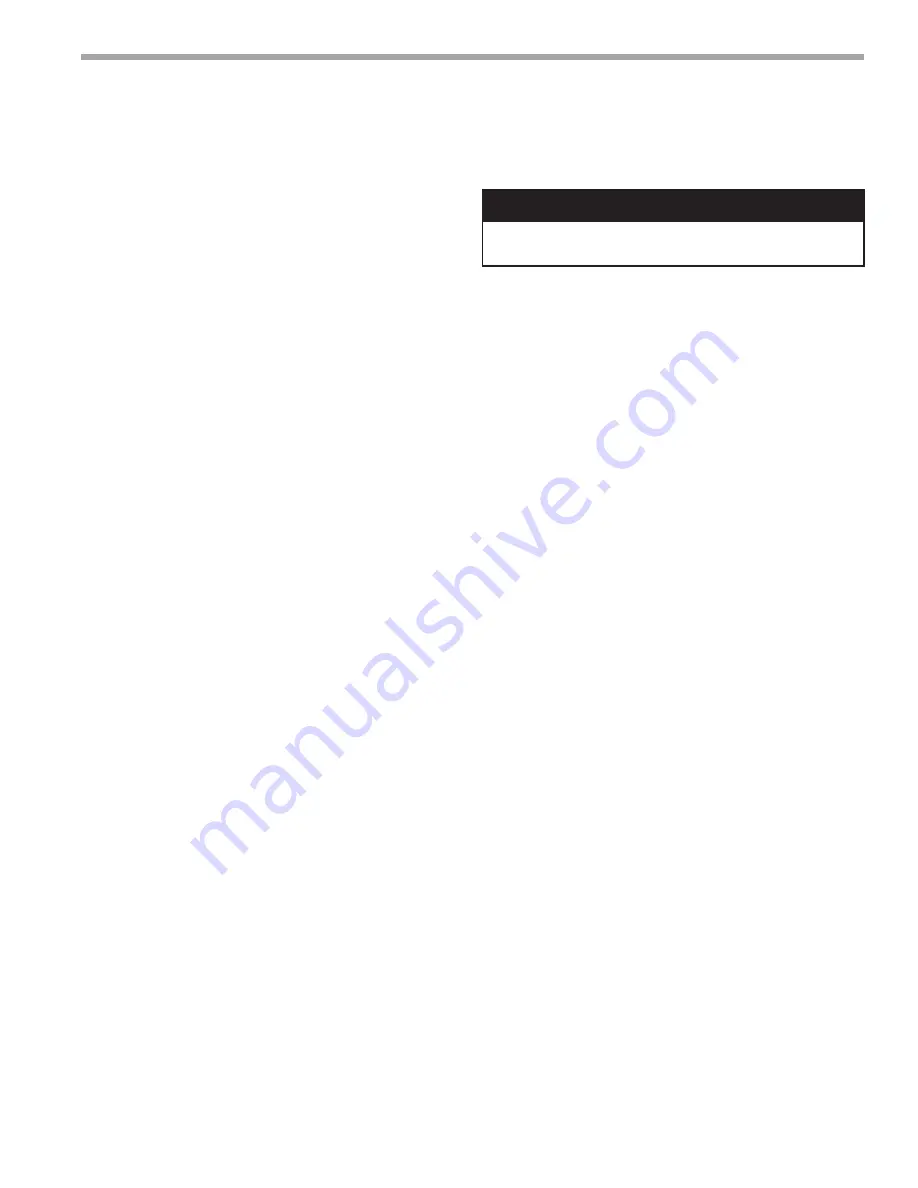
JRC-Series
R e v. : D e c e m b e r 8 , 2 0 2 1
T H E S M A R T S O L U T I O N F O R E N E R G Y E F F I C I E N C Y
I n s t a l l a t i o n , O p e r a t i o n , M a i n t e n a n c e
31
Piping System Cleaning and Flushing
Piping System Cleaning and Flushing -
Cleaning and
flushing the WLHP piping system is the single most
important step to ensure proper start-up and continued
efficient operation of the system.
Follow the instructions below to properly clean and flush
the system:
1. Ensure that electrical power to the unit is disconnected.
2. Install the system with the supply hose connected
directly to the return riser valve. Use a single length of
flexible hose.
3. Open all air vents. Fill the system with water. DO
NOT allow system to overflow. Bleed all air from the
system. Pressurize and check the system for leaks
and repair as appropriate.
4.
Verify that all strainers are in place (the manufacturer
recommends a strainer with a #20 stainless steel
wire mesh). Start the pumps, and systematically
check each vent to ensure that all air is bled from the
system.
5. Verify that make-up water is available. Adjust make-
up water as required to replace the air which was
bled from the system. Check and adjust the water/air
level in the expansion tank.
6. Set the boiler to raise the loop temperature to
approximately 86°F [30°C]. Open a drain at the
lowest point in the system. Adjust the make-up water
replacement rate to equal the rate of bleed.
7.
Refill the system and add trisodium phosphate in
a proportion of approximately one pound per 150
gallons [1/2 kg per 750 l] of water (or other equivalent
approved cleaning agent). Reset the boiler to raise
the loop temperature to 100°F [38°C]. Circulate the
solution for a minimum of 8 to 24 hours. At the end of
this period, shut off the circulating pump and drain the
solution. Repeat system cleaning if desired.
8. When the cleaning process is complete, remove the
short-circuited hoses. Reconnect the hoses to the
proper supply, and return the connections to each of
the units. Refill the system and bleed off all air.
9. Test the system pH with litmus paper. The system
water should be in the range of pH 6.0 - 8.5 (see
table 3). Add chemicals, as appropriate to maintain
neutral pH levels.
10.
When the system is successfully cleaned, flushed,
refilled and bled, check the main system panels,
safety cutouts and alarms. Set the controls to properly
maintain loop temperatures.
DO NOT use “Stop Leak” or similar chemical agent in
this system. Addition of chemicals of this type to the
loop water will foul the heat exchanger and inhibit unit
operation.
CAUTION!
To avoid possible damage to a plastic (PVC) piping
system, do not allow temperatures to exceed 110ºF (43ºC).
Note: The manufacturer strongly recommends all piping
connections, both internal and external to the unit, be
pressure tested by an appropriate method prior to any
finishing of the interior space or before access to all
connections is limited. Test pressure may not exceed
the maximum allowable pressure for the unit and all
components within the water system. The manufacturer
will not be responsible or liable for damages from water
leaks due to inadequate or lack of a pressurized leak
test, or damages caused by exceeding the maximum
pressure rating during installation.
⚠
CAUTION!
⚠