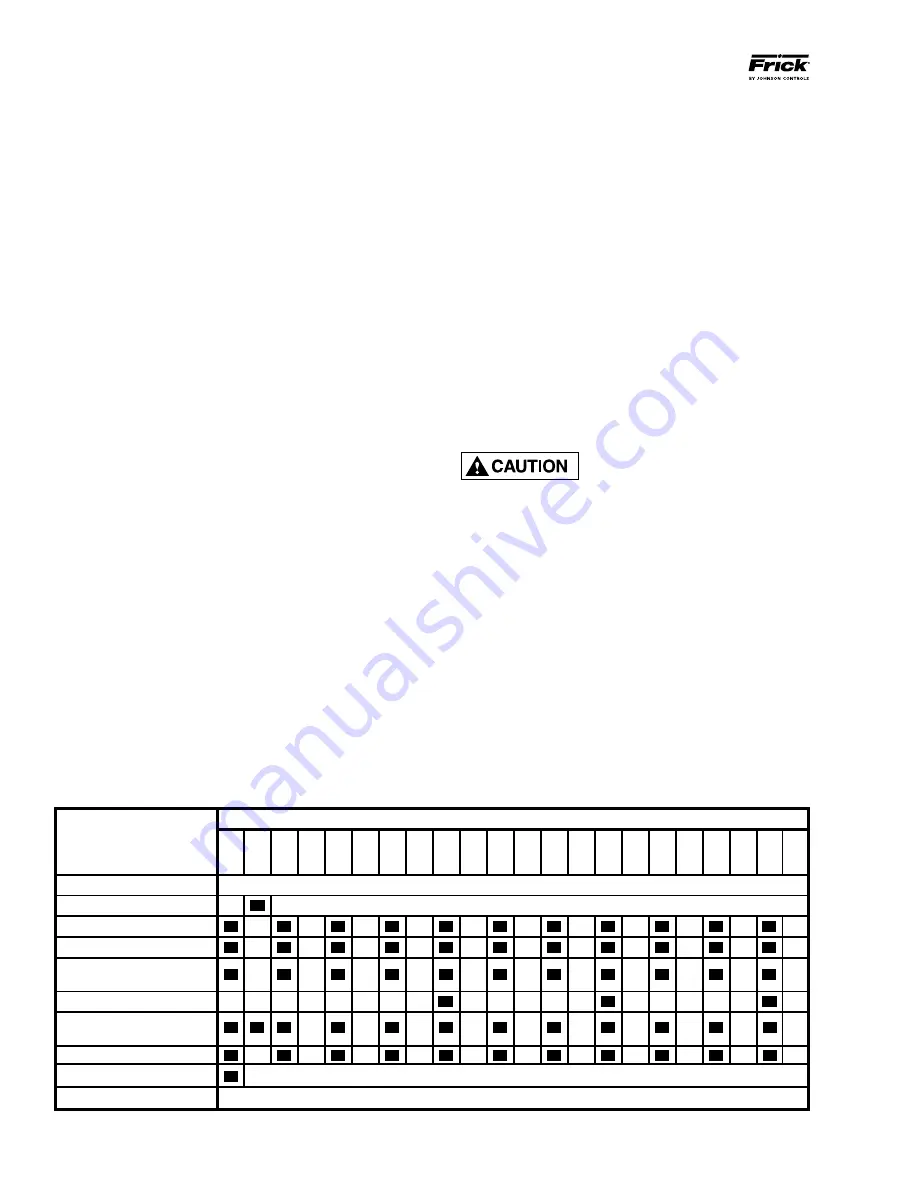
RWF ROTARY SCREW COMPRESSOR UNITS
MAINTENANCE
S70-600 IOM (OCT04)
Page 28
RECOMMENDED
MAINTENANCE PROGRAM
In order to obtain maximum compressor unit perform ance
and ensure reliable operation, a regular main tenance pro-
gram should be followed.
The compressor unit should be checked daily for leaks, ab-
normal vibration, noise, and proper operation. A log should
also be maintained. There should be continued monitor ing
of oil quality and oil analysis testing. In addition, an analysis
of the unit’s vibration should be periodic ally made.
VIBRATION ANALYSIS
Periodic vibration analysis can be useful in detecting bear-
ing wear and other mechanical failures. If vibration analysis
is used as a part of your preventive main tenance program,
take the following guidelines into consideration.
1.
Always take vibration readings from exactly the same
places and at exactly the same percentage of load.
2.
Use vibration readings taken from the new unit at start-up
as the base line reference.
3.
Evaluate vibration readings carefully as the instru ment
range and function used can vary. Findings can be easily
misinterpreted.
4.
Vibration readings can be influenced by other equip ment
operating in the vicinity or connected to the same piping as
the unit.
OIL QUALITY and ANALYSIS
High quality refrigeration oil is necessary to ensure compres-
sor longevity and reliability. Oil quality will rapidly deteriorate
in refrig eration systems containing moisture and air or other
contaminants. In order to ensure the quality of the refrigera-
tion oil in the com pressor unit:
1.
Only use Frick refrigeration oil and filter elements or
warranty claim may be denied.
2.
Participate in a regular, periodic oil analysis program to
maintain oil and system integrity.
OPERATING LOG
The use of an operating log as included in this manual (see
Table of Contents) permits thorough analysis of the operation
of a refrigeration system by those responsible for its mainte-
nance and servicing. Continual recording of gauge pressures,
temperatures, and other pertinent information, enables the
observer and serviceman to be constantly familiar with the
operation of the system and to recognize immediately any de-
viations from normal operating conditions. It is recommended
that readings be taken at least every four hours.
MOTOR BEARINGS
Follow the motor manufacturer’s maintenance recommenda-
tions for lubrication. See illustration of schedule for standard
motor, Figure 25.
Make sure the motor bearings are
properly lubricated before start-up as
required by the motor manuf ac turer.
GREASE COMPATIBILITY
If it becomes necessary to mix greases, be careful not to
combine different oil bases or thickeners. DO NOT mix a
mineral oil-base grease with a synthetic oilbase grease.
Also, a grease with a lithium thickener should not be mixed
with one containing a sodium thickener. The table illustrates
the compatibility of various types of grease based on results
by National Lubricating Grease Institute (NLGI). The chart
indicates a great variance in compaibility with the greases
tested.
MAINTENANCE SCHEDULE
This schedule should be followed to ensure trouble-free operation of the compressor unit.
CLEAN OIL STRAINERS
CLEAN LIQUID
STRAINERS
REPLACE FILTER
REPLACE COALESCER
CHECK AND CLEAN
SUCTION STRAINER
95000
90000
85000
80000
75000
70000
65000
60000
55000
50000
45000
40000
35000
30000
25000
20000
15000
10000
8000
5000
1000
200
MAINTENANCE
FREQUENCY OR HOURS OF OPERATION (MAXIMUM)
CHANGE OIL
As directed by oil analysis
OIL ANALYSIS
Then every 6 months
VIBRATION ANALYSIS*
Every 6 months, more frequently if levels increase
REPLACE SEAL
When leak rate exceeds 7 - 8 drops per minute
CHECK COUPLING
* Perform baseline vibration analysis at start-up and every six months thereafter to maintain 1-2-3 Warranty.