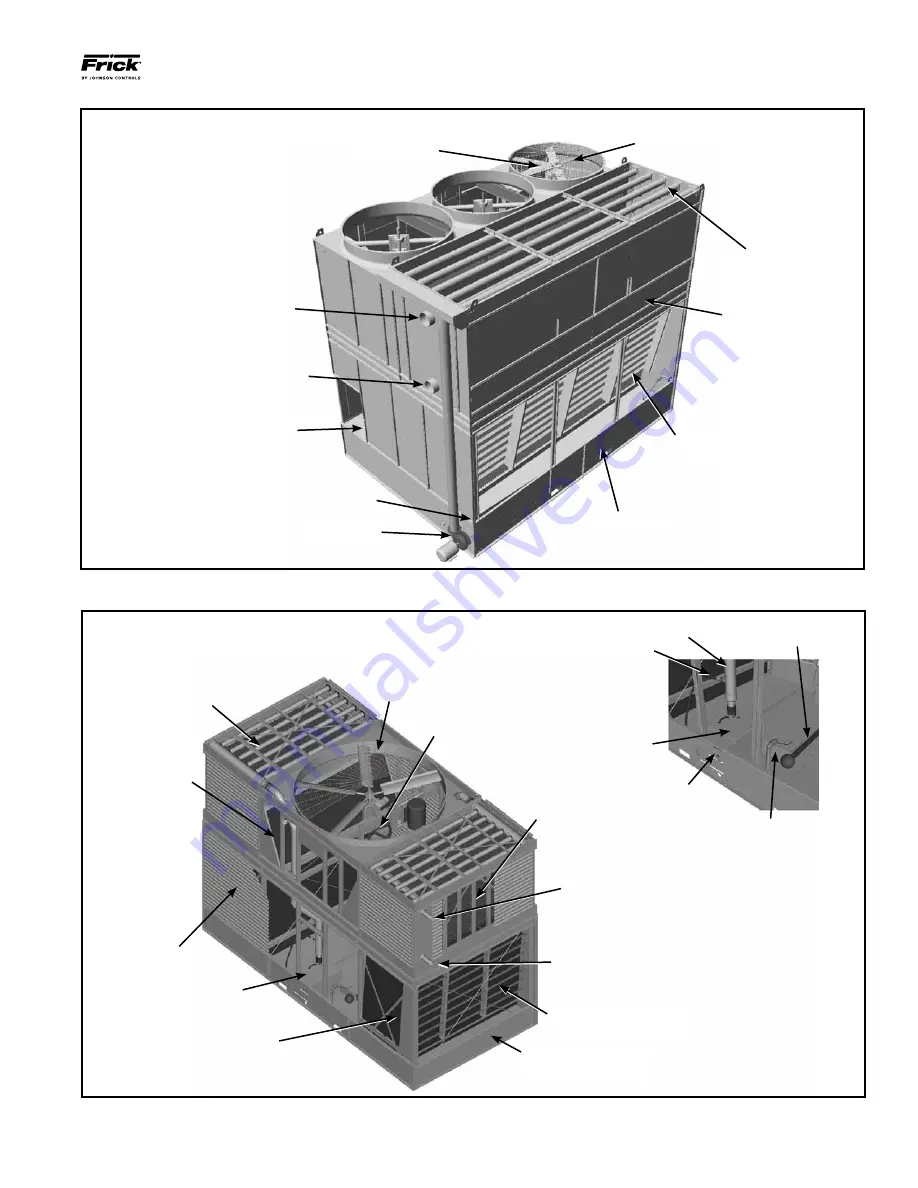
ECH EVAPORATIVE CONDENSERS
INSTALLATION - OPERATION - MAINTENANCE
140.910-IOM (DEC 13)
Page 3
Recirculating
Water Pump
Coil Connection:
ECH Refrigerant Out
Coil Connection:
ECH Refrigerant In
Access Door
Bleed Line and Valve
Air Inlet Louvers
Cold Water Basin
Fill with Integral
Drift Eliminators
Spray Water
Distribution System
Power Train
Axial Fan(s)
Single Side Air Inlet ECH
Dual Air Inlet ECH-D
Suction Strainer
Spray Riser Pipe
Bleed Valve
Spray Pump
Access Door
Spray Pump
Motor
Makeup Valve
Coil Connection:
Refrigerant Out
Coil Connection:
Refrigerant In
Prime Surface
Coil
Access Door
Air Inlet Louvers
Cold Water Basin
Fill with Integral
Drift Eliminators
Spray Water
Distribution System
Power Train
Fan Guard
Casing
Removable
Drift
Eliminators