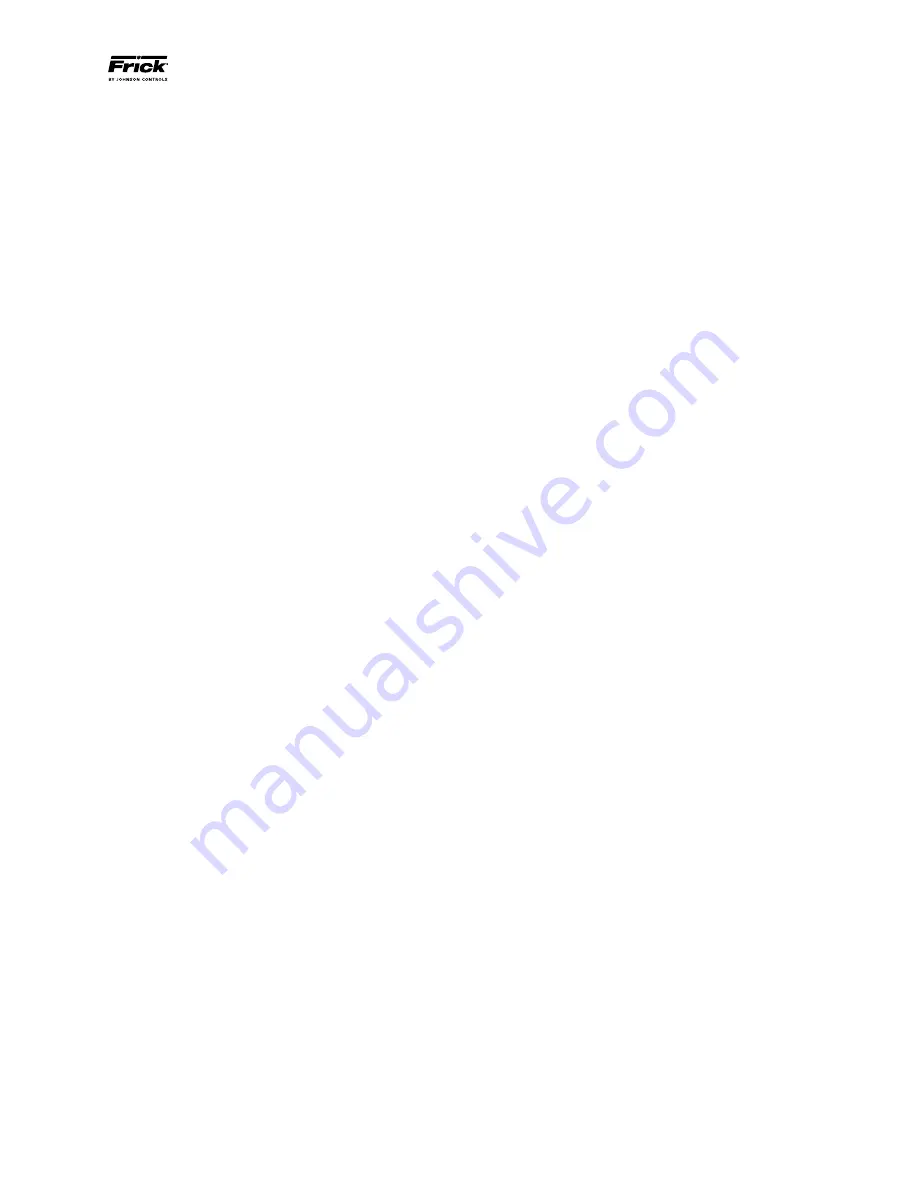
RXF ROTARY SCREW COMPRESSOR UNITS
INDEX
070.410-IOM (JAN 12)
Page 61
Heat-sink paste, 8
high-stage operation, 13
hydraulic system, 14
J
jack, 6
L
liquid carryover, 7
liquid injection, 9, 16
Alarms, 19
analog input signal, 18
Danfoss Liquid Injection Valve, 18
digital Input signal, 18
Display, 18
dual dip tube method, 10
Enter push button, 18
high-stage units, 9
ICAD (Industrial Control Actuator
with Display), 18
ICM valve, 18
low condensing pressures, 9
Mod, 18
Motorized Industrial Control Valve,
18
Opening Degree, 18
parameters, 18
Parameter list, 20
Analog Output signal, 20
Automatic calibration, 20
Digital Input function, 20
Fail-safe, 20
ICM configuration, 20
Main Switch, 20
Mode, 20
Modulating Mode, 20
Old Alarms, 20
Password, 20
solenoid valve, 18
liquid refriger ant, 16
low voltage, 11
lubrication system, 13
M
magnetic field, 50
main oil injection port, 14
Maintenance
filter elements, 30
moisture, 29
Oil quality, 29
Proper Installation of Electronic
Equipment, 48
refrigeration oil, 29
Maintenance, 22
Bare Compressor Mounting, 34
bearing failure, 22
coalescer filter element, 25
daily log, 29
discharge service valve, 25
Disconnect Power, 22
disconnect switches, 23
drain valve, 24, 25
dry nitrogen, 22
Isolation Valves, 22
isolation valves, 23
liq uid injection strainer, 24
liquid injection valves, 22
liquid refrigerant, 22
low pressure transducer, 23
motor bearings, 31
lubrication, 31
nuisance oil level cutouts, 25
oil-charging valve, 25
oil analysis testing, 29
oil cooler, 25
Oil entrained refrigerant, 23, 25
oil filters, 23
oil filter element, 25
oil foaming, 24
oil pressure loss, 25
oil pump strainer, 24
operating log, 31
Operating Log Sheet, 53
pressure sensors, 34
Pressure Transducers, 32
Conversion Data, 32
Replacement, 33
Testing, 32
P & I Diagram, 41
refrigerant vapor, 23, 25
Safety Equipment, 22
service valves, 23
sole noid valves, 23
spin-on oil filter element, 23
starting torque, 24
strainer ele ments, 25
strainer service valves, 24
suction check valve bypass, 23, 25
suction service valve, 25
suction strainer, 22
suction valve bypass, 24
superheat, 22
Troubleshooting.
See Index,
Trouble-
shooting
Ventilation, 22
vibration analysis, 29
Vibration Data Sheet, 59
vibra tion level, 22
water vapor, 22
Wiring Harness, 47
Maintenance
DIN connector plug, 33
linear transmitter, 33
Maintenance Schedule, 30
oil level control, 34
Oil Level Transmitter, 34
sensor well, 33
temperature sensor, 33
Temperature Transmitter, 34
volume ratio control, 33
metal conduit, 50
microprocessor, 10, 16
moments, 9
motor, 11
motor contactor, 11
Motor cycling, 11
motor rotation, 6, 13
motor starter contactor, 11
mounting bolts, 6
movable slide valve, 14
Multiple Compressor Economizer
System, 10
N
neoprene drive spacer, 6
noise suppression, 52
O
oil charge reservoir, 14
Oil distillers, 7
oil filter, 7
oil foaming, 29
oil heaters, 7
oil leakage, 29
oil level cutout, 29
oil pressure loss, 29
operating volume ratio, 16
Optical Isolation, 52
O-ring compression, 39
P
pH, 8
power feed, 50
power fluctuations, 12
pressure differential, 14
PVC-coated metallic, 50
PVC conduit, 50
Q
Quantum™ LX, 11
Quantum™LX, 14, 52
Quantum™ LX control system, 11
Quantum™ panel, 11
R
reboot, 52
recovery procedure, 25
RXF rotary screw compressor, 13
Moveable slide valve, 13
shaft seal, 13
S
SBC Board, 11
scaling, 8
self-lubricating, 13
separator, 6
severe water conditions, 8
Shell And Coil Economizer System, 10
shipping gauges, 7
shutdown, 22
liquid injection, 22
package valves, 22
solenoid valves, 22
strainers, 22
sight glass, 7, 14, 25
signal wiring, 50
single-port liquid injection, 16
Skip frequencies, 21
slide stop, 21