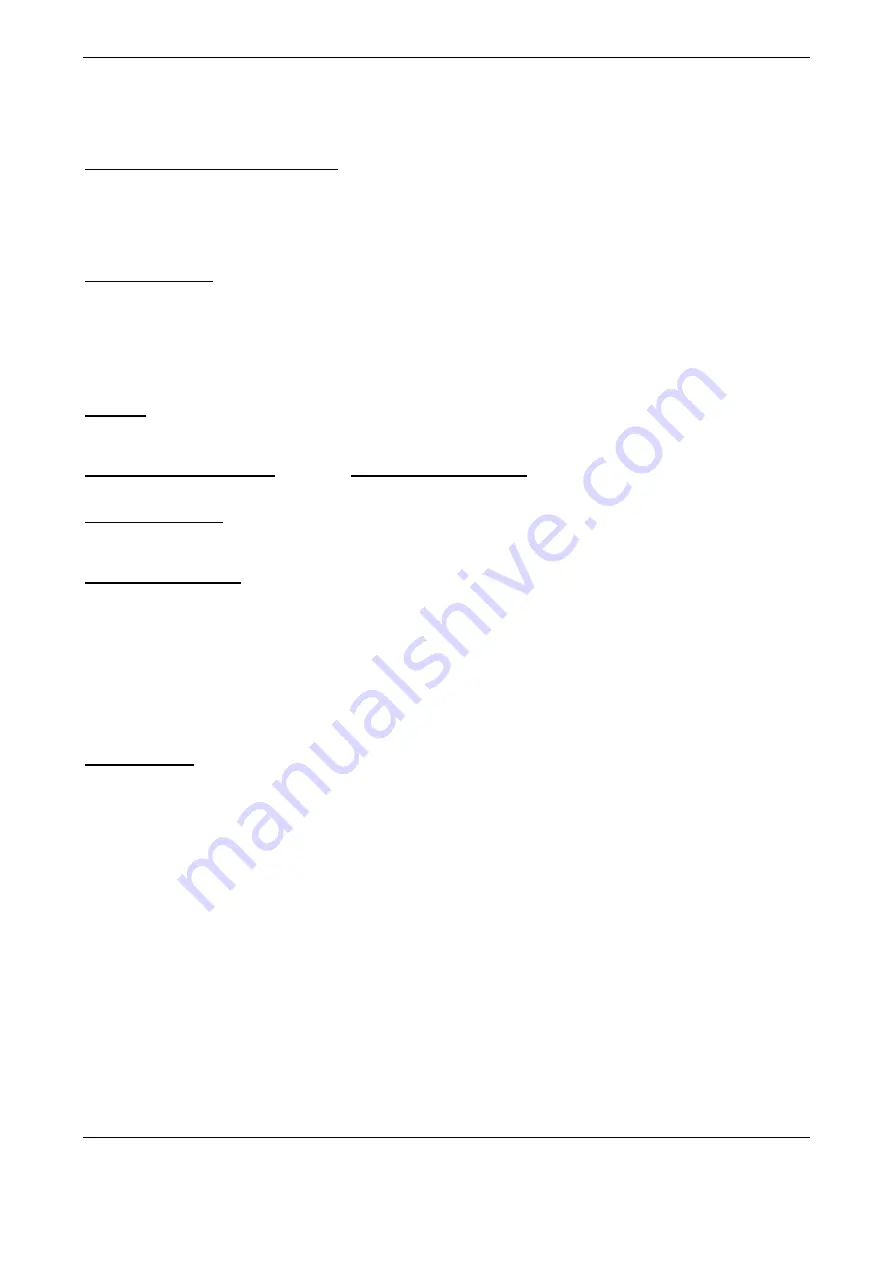
2
111 6187 050 E
A 12
Pipelines should be insulated to protect actuators against high temperatures; here sufficient room is to be left
for servicing the stem seal pack. For trouble free function of the control valve the pipe immediately upstream
of the valve should be straight for the length of at least 2x DN and the pipe immediately downstream for the
length of at least 6x DN.
mounting and removal information:
The control valve is normally supplied complete with actuator. It is not permitted to remove or replace an
actuator on systems in operation, under operating temperature and pressure. For conversion or service, The
actuator mounting procedure should follow the actuator SDI. During mounting procedure the plug should
NOT be rotated with downward pressure. Ensure adherence to max. valve operating forces for actuator
replacement.
Actuator removal:
In addition to general mounting guidelines and TRB 700 the following points should be observed:
•
Pressure free piping system
•
Cooled
fluid
•
Drained piping system
•
With corrosive or aggressive fluids the piping system should be vented.
•
Work to be performed by qualified personnel only.
Caution:
Electrical wiring must be in conformance with directives for high-voltage installations; voltage supply and
frequency must be identical with data on the product nameplate.
Voltage supply line wiring:
Voltage supply line fuse:
Wire gauge min. 1mm
2
.
max. 6 A, 2 A at 24V, observe DIN VDE 116!
Electrical isolation:
Prior to the removal of the actuator cover, e.g. for mechanical maintenance and adjustment, line voltage
supply must be disconnected by means of an isolation switch, safeguarded against inadvertent operation.
Electrical connection:
•
Select cable conduit adapter, in accordance EN 50262, to match cable diameter.
•
Lead cable through the conduit adapter to the respective terminals, and then remove insulation from wire
tips. Inside the actuator, wires must be routed or fastened so that they are protected against damage by
moving or rotating parts and removal or replacement of the actuator cover.
•
Fasten ground wire to ground terminal. (Not applicable for 24V version )
•
Tighten Conduit adapter to achieve a reliable strain relief.
Installation and test are to be in accordance with accessory by-pack instructions.
Technical data:
Electrical connection:
Terminal strip via 2 PG 9/11 cable connectors
M 16 x 1.5, (1) PG 9 plug M 16 x 1.5
Operating voltage:
230V / 50Hz
+ 10% / - 15%
24V / 50Hz
+ 10% / - 15%
24V / 60Hz
+ 10% / - 15%
Limit switches:
2 pressure switches max. 250V AC
Permissible ambient temperature:
-20°C to +60°C
Operating force:
6000 N + 300N
Manual operation:
Side-mounted hand wheel
Stroke timing
for 42mm stroke
:
148sec. with 50 Hz, 118sec. with 60 Hz
Power consumption:
37 / 50VA with 50 / 60 Hz + 5VA with positioner
Nominal stroke:
42mm max. 45mm
Enclosure to DIN 40050:
IP 65
Accessories (installable in-situ):
E
= 2 limit switches, max. 250V AC
Resistive load max. 5A
Inductive load max. 3A
Light bulb
max. 3A
R2 = feedback potentiometer 2 k
Ω
R135 = feedback potentiometer 135
Ω
Positioner:
0-10V (0-20mA) Control