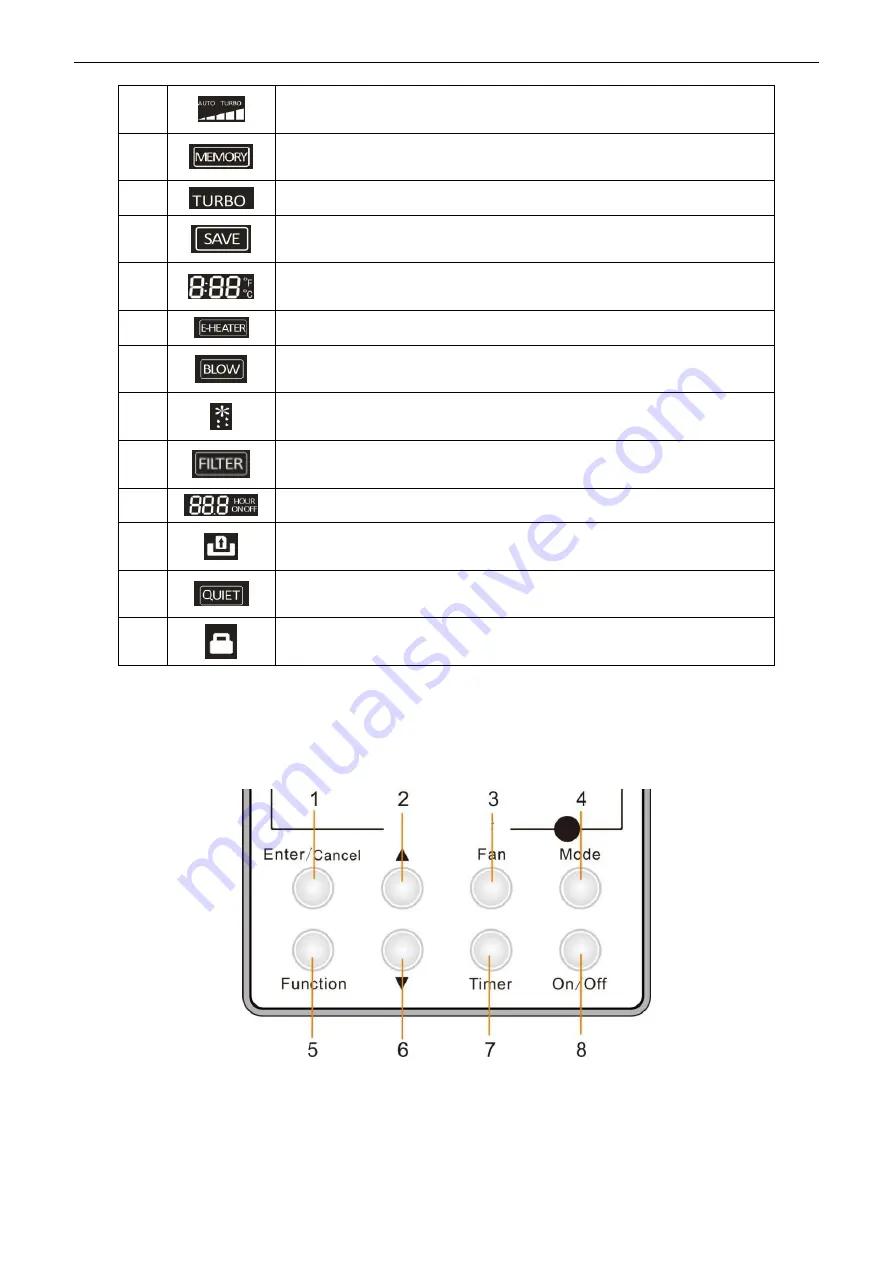
Service Manual
18
15
Fan speed
16
Memory function
The unit will resume the original setting state after power
is restored
17
Turbo function
18
Energy-saving function
19
Ambient/setting temperature
20
Electric heater
21
Blow function
(Coil drying function)
22
Defrosting function
(Heat Pump only)
23
Filter cleaning
reminder
24
Timer Setting
25
Keycard control /
Motion Sensor Activation
26
Quiet function
27
Lock function
7
.2 Operation View
7
.2.1
Wired Zone Controller
Buttons
Figure 2-3-3
Wired zone controller
buttons
Summary of Contents for DHR18CSB21S
Page 12: ...Service Manual 3 2 Nomenclature ...
Page 47: ...Service Manual 38 Figure 2 7 13 ...
Page 65: ...56 H6 DC fan error Service Manual ...
Page 73: ...64 DHR48CSB21S Service Manual Service Manual ...
Page 92: ...83 ...