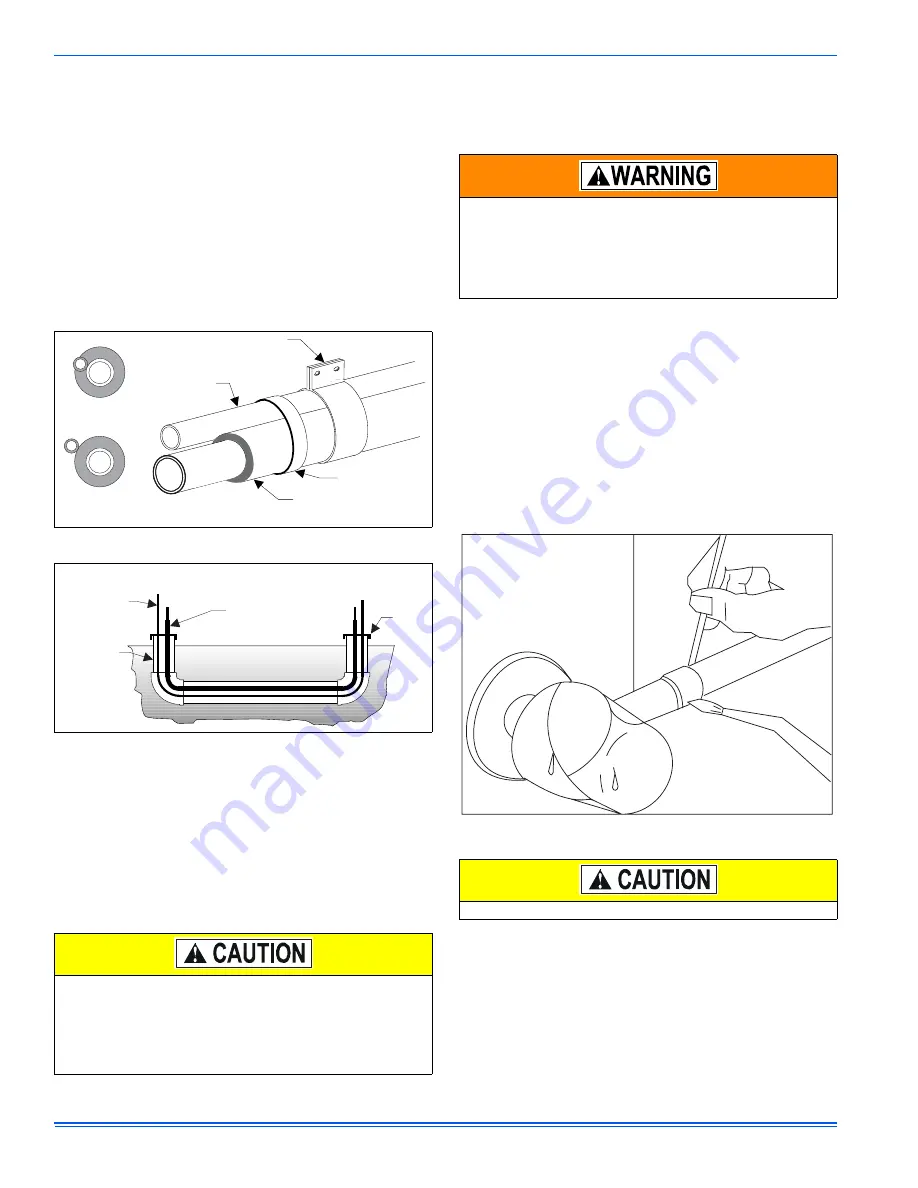
501562-UIM-A-0909
4
Johnson Controls Unitary Products
4.
The vapor line must be insulated with a minimum of 1/2" foam rub-
ber insulation (Armaflex or equivalent). Liquid lines that will be
exposed to direct sunlight and/or high temperatures must also be
insulated.
5.
Tape and suspend the refrigerant lines as shown. DO NOT allow
tube metal-to-metal contact. See Figure 2.
6.
Use PVC piping as a conduit for all underground installations as
shown in Figure 3. Buried lines should be kept as short as possible
to minimize the build up of liquid refrigerant in the vapor line during
long periods of shutdown
7.
Pack fiberglass insulation and a sealing material such as perma-
gum around refrigerant lines where they penetrate a wall to reduce
vibration and to retain some flexibility.
8.
See application part number 036-61920-000 for additional piping
information.
PRECAUTIONS DURING BRAZING OF LINES
All outdoor unit and evaporator coil connections are copper-to-copper
and should be brazed with a phosphorous-copper alloy material such
as Silfos-5 or equivalent. DO NOT use soft solder. The outdoor units
have reusable service valves on both the liquid and vapor connections.
The refrigerant charge is retained within the outdoor unit during ship-
ping and installation. The reusable service valves are provided to evac-
uate and charge per this instruction.
Serious service problems can be avoided by taking adequate precau-
tions to ensure an internally clean and dry system.
PRECAUTIONS DURING BRAZING SERVICE VALVE
Wrap a wet rag around the service valve as shown in Figure 4 to pre-
vent heat damage. Also, protect all painted surfaces, insulation, and
plastic base during brazing. After brazing, cool joint with wet rag.
The valve can be opened by removing the plunger cap and fully insert-
ing a hex wrench into the stem and backing out counter-clockwise until
valve stem just touches the chamfered retaining wall.
Connect the refrigerant lines using the following procedure:
1.
Remove the cap and Schrader core from both the liquid and vapor
service valve service ports at the outdoor unit. Connect low pres-
sure nitrogen to the liquid line service port.
2.
Braze the liquid line to the liquid valve at the outdoor unit. Be sure
to wrap the valve body with a wet rag. Allow the nitrogen to con-
tinue flowing. Refer to the Tabular Data Sheet for proper liquid line
sizing.
3.
Carefully remove the rubber plugs from the evaporator liquid and
vapor connections at the indoor coil.
4.
Braze the liquid line to the evaporator liquid connection. Nitrogen
should be flowing through the evaporator coil.
5.
Slide the grommet away from the vapor connection at the indoor
coil. Braze the vapor line to the evaporator vapor connection. After
the connection has cooled, slide the grommet back into original
position. Refer to the Tabular Data Sheet for proper vapor line siz-
ing.
FIGURE 2:
Tubing Hanger
FIGURE 3:
Underground Installation
Dry nitrogen should always be supplied through the tubing while it
is being brazed, because the temperature is high enough to cause
oxidation of the copper unless an inert atmosphere is provided. The
flow of dry nitrogen should continue until the joint has cooled.
Always use a pressure regulator and safety valve to insure that only
low pressure dry nitrogen is introduced into the tubing. Only a small
flow is necessary to displace air and prevent oxidation.
LIQUID
LINE
INCORRECT
CORRECT
TAPE
SHEET METAL
HANGER
INSULATED
VAPOR LINE
TO INDOOR
COIL
TO OUTDOOR
COIL
CAP
INSULATED
VAPOR LINE
LIQUID
LINE
PVC
CONDUIT
This is not a backseating valve. The service access port has a
valve core. Opening or closing valve does not close service access
port.
If the valve stem is backed out past the chamfered retaining wall,
the O-ring can be damaged causing leakage or system pressure
could force the valve stem out of the valve body possibly causing
personal injury.
FIGURE 4:
Heat Protection
The evaporator is pressurized.