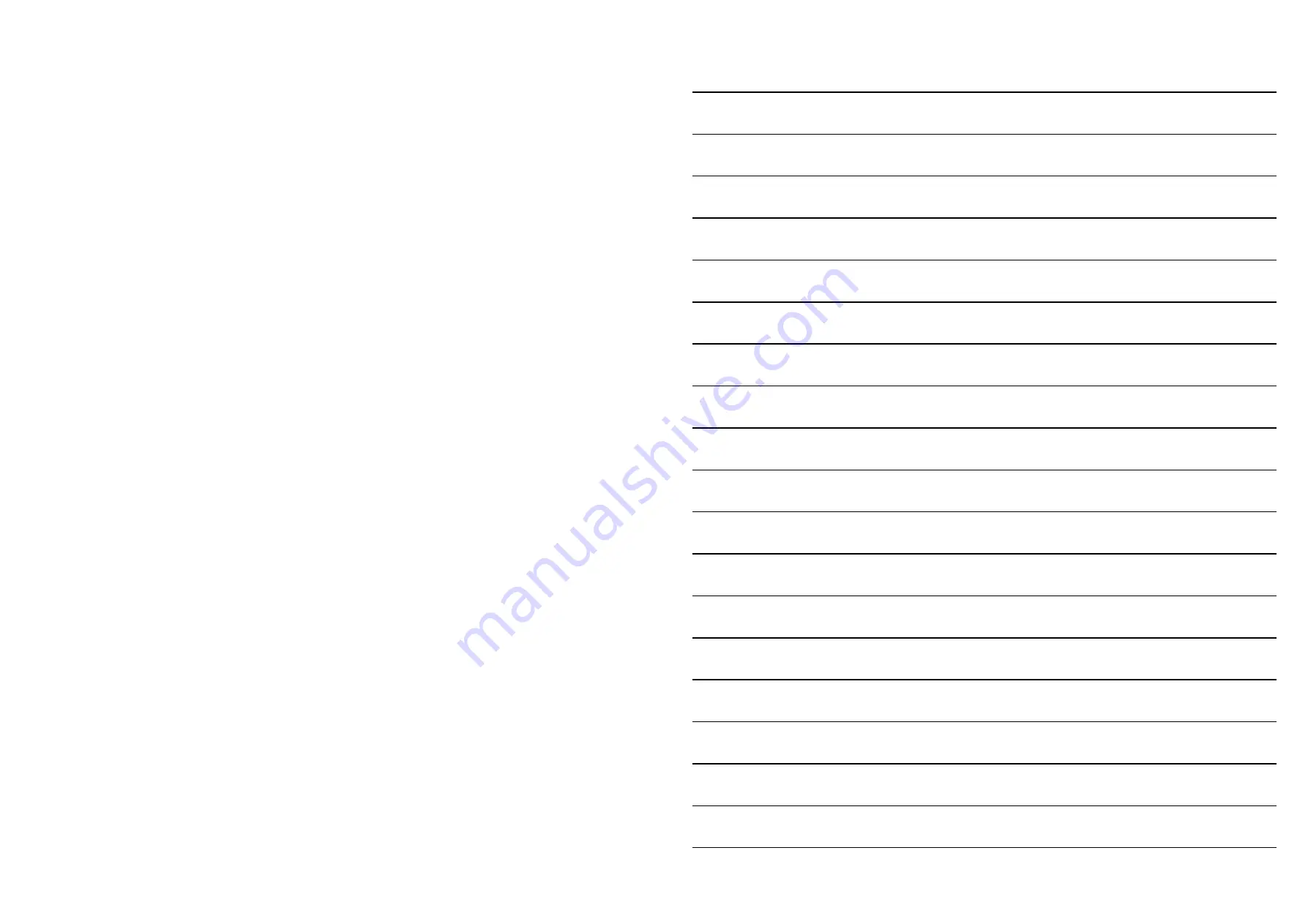
2
31
NOTES:
IMPORTANT: STATUTE LAW DEFINES THAT ALL GAS APPLIANCES MUST BE INSTALLED BY COMPETENT
PERSONS, (i.e. CORGI REGISTERED INSTALLERS) IN ACCORDANCE WITH THE GAS SAFETY
(INSTALLATION AND USE) REGULATIONS (CURRENT EDITION). FAILURE TO COMPLY WITH THESE
REGULATIONS MAY LEAD TO PROSECUTION.
2.
HEATER COMPARTMENT AND CLEARANCES (SEE BS 5864)
2.1
IMPORTANT:
If the heater is to be fitted to an existing base duct (warm air plenum), always ensure that installation is carried
out such that the rear left hand corner of the heater is aligned with the rear left hand corner of the base duct, so that any
overhang or blanking off will be at the front and/or right hand side. In any event, blanking plates must be mechanically
secured and all joints sealed.
2.2
When the heater is fitted into a compartment, a minimum clearance from the compartment walls of 25mm (1in) at the sides, rear
and front must be left. Consideration should also be given to the space required for the removal and replacement of the filter
tray and the entry of the gas and electrical supplies.
2.3
For service access, a minimum of 450mm (18ins) is required at the front of the heater. Space must also be allowed, in a
compartment installation, to permit the removal of the heater. The clearance between the appliance and the compartment
should not be less than 75mm (3in). However, where clearances are less than 75mm, the internal surface of the compartment
must be lined with non-combustible material. The compartment must be of a fixed rigid structure.
2.4
In airing cupboard installations, the part used as the air heater compartment must comply with the relevant section of BS 5864
and must be completely separated by either a non-combustible partition or a perforated metal partition with the perforations
not exceeding 13mm (
1
/
2
in). The secondary flue must be a tight fit where it passes through the partition and must be suitably
protected (see BS 5440:Part 1).
2.5
In under-stairs installations, the compartment must comply with the relevant section of BS 5864, provided that in addition, all
internal surfaces, including the base, are non-combustible or lined with non-combustible material. This requirement is
applicable only to dwellings of more than two storeys.
2.6
In slot fit installations (see instructions packed with Slotfit Kit TS50), the slot fit compartment must comply with the relevant
section of BS 5864. Side and rear clearances should be not less than 25mm (1in).
Important:
Ensure that the rear of the heater is at no time subjected to air pressure subject to leaks from underfloor, joists or
roof spaces.
2.7
In freestanding installations (see instructions packed with Top Closure Kit TCS50), only one or two walls will be in close
proximity to the air heater; these must be non-combustible in compliance with the relevant section of BS 5864.
2.8
If the appliance is to be installed onto a combustible surface, a suitable base tray (BT50 ) is required. However, when a base
duct is used, this provides sufficient protection for combustible material and no further insulation is required.
2.9
For Slot Fix applications (see instructions packed with the Slot Fix Kit), it is important to ensure that the draught diverter relief
is maintained on both sides of the application.
3.
VENTILATION AND COMBUSTION AIR
3.1
The room or internal space in which the heater is installed requires a permanent air vent of minimum effective area 81cm
2
(12in
2
). The air vent should be either direct to outside air or to an adjacent room or internal space (other than a toilet or
bathroom) that itself has an equivalent air vent direct to outside.
3.2
Combustion air may be introduced, via a 120mm (5in) nominal bore pipe, connected to a return air duct or plenum from a
ventilated area and fitted with a lockable damper. The damper should be adjusted to control combustion airflow to 0.0137m
3
/s
(29cfm), (i.e. 1.11m/s [220ft/min] velocity in a 120mm [5in] bore pipe). If this arrangement is used, a non-closeable warm air
register MUST be provided in the same area as the front of the air heater or heater compartment if a return air grille is not
located in that area.
3.3
When installed in a compartment, two permanent ventilation openings into the compartment are required, one at high level
and one at low level, both communicating either directly with outside air or with a ventilated room or space. The minimum
effective areas specified in Table 1 are related to the rated heat input of the Air Heater, and assuming that an ELJAN 6
circulator is fitted.
3.4
If any room or area from which air is drawn for ventilation or combustion contains an extract fan, the permanent vents must be
sized to ensure that the operation of the appliance(s) at full rate is/are not adversely affected. A spillage test as specified in
sub-para 6.8 (Safety Checks) is carried out and any remedial work undertaken.