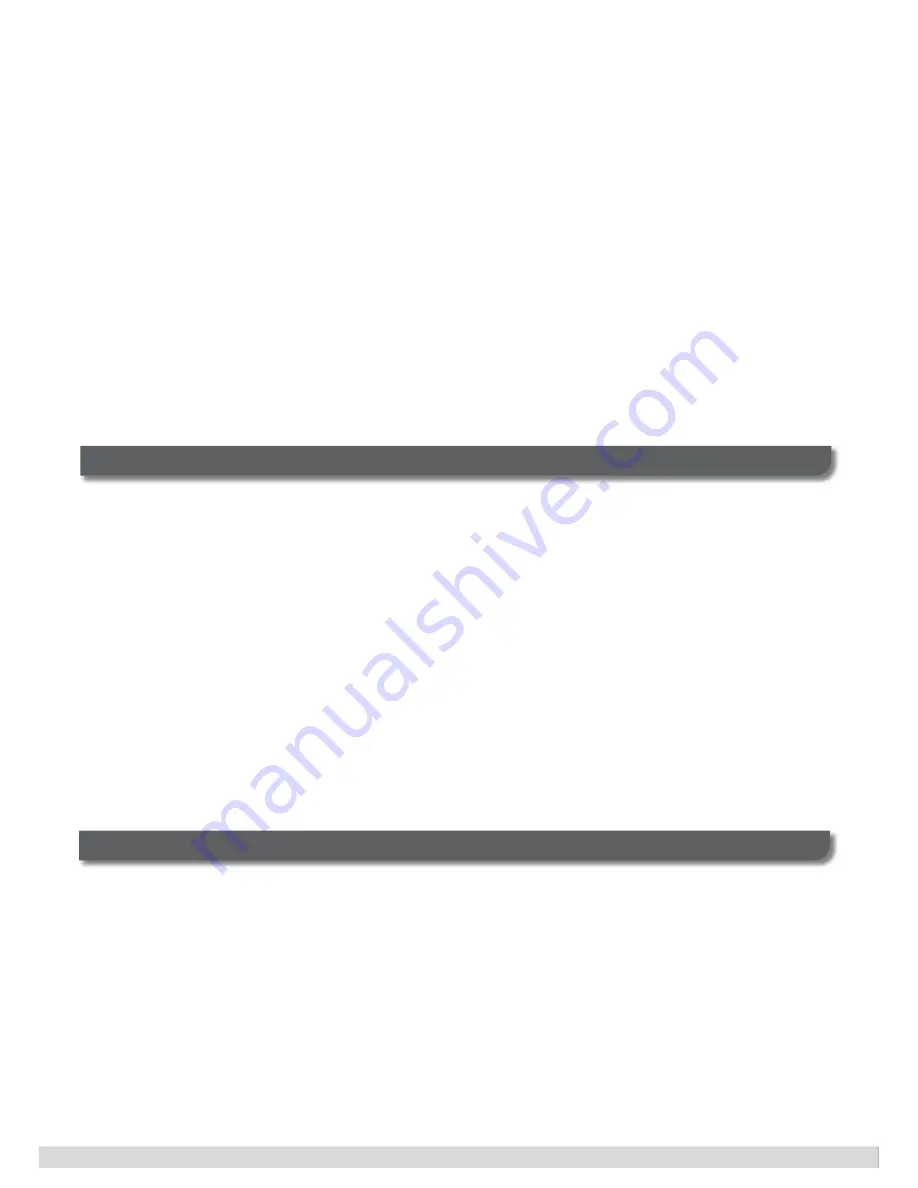
www.johnsonandstarley.co.uk
1
13.3 WATER BURNER PRESSURE TEST
NOTE:
THE WATER CIRCULATOR BURNERS ARE PRE-SET AND SHOULD NOT REQUIRE ADJUSTING.
13.3.1 Loosen the screw on the outlet pressure test point and fit a pressure test gauge (see Figure 7)
13.3.2 Check the gauge reading against the information at Table 4.
13.3.3 If necessary, use the burner pressure adjuster to obtain the required gauge reading as shown at Table 4.
13.3.4 Remove the pressure gauge and re-tighten the screw on the outlet pressure test point.
13.4 SAFETY CHECKS
13.4.1 Check for gas soundness within the appliance.
13.4.2 Check for water soundness around circulator and ALL joints.
13.4.3 Turn on both the gas and electrical supplies to the heater.
13.4.4 Set the “WATER HEATER” switch on the time control unit to “CONT”.
13.4.5 Light the ignition and main burners as described in paragraph 13.2
13.4.6 Allow the circulator to operate for a period of 5 minutes to stabilise.
13.4.7 Turn off gas supply to heater at the heater gas cock. DO NOT TURN OFF AT GAS METER!
13.4.8 The circulator SHOULD automatically go into “LOCKOUT” indicated by the red LED on the indicator panel and
the LED status indicator will show “H”
13.4.9 Reinstate gas supply and wait for a minimum period of 10 seconds.
13.4.10 Depress the “RESET” button on the indicator panel.
13.4.11 The heater will go through its ignition procedure and the ignition and main burners SHOULD ignite.
13.4.12 Set the “WATER HEATER” switch on the time control unit to “TIMED”
14. INSTRUCTIONS FOR USERS
14.1
If the building is unoccupied, ensure that the user instructions are left taped to the air heater for the the user’s reference
and that the installation instructions are left at or near the air heater for use on future service calls.
14.2
If the building is occupied, hand the user instructions over and ensure that the user understands:
14.2.1 How to light both the air heater and water circulator.
14.2.2 How to re-set the air heater or water circulator if “LOCKOUT” occurs.
14.2.3 How to operate the time control, thermista-stat and the SUMMER AIRFLOW switch.
14.2.4 That the time control must be reset following a power failure.
14.2.5 How to use the circulator thermostat to set the water temperature.
14.2.6 How to turn off the heater and switch off the electrical supply to the heater.
14.2.7 How to remove, clean and refit the air filter and at what intervals, (i.e. fortnightly, or weekly for new houses).
14.2.8 How to control the heating system by opening and closing warm air outlets.
14.2.9 How to obtain summer air circulation.
14.2.10 That the air grilles on the heater or heater compartment; grilles and ventilators in the walls, windows or doors
of the building
MUST NOT BE OBSTRUCTED
.
14.2.11 That the heater must be serviced at least once a year by a competent person to ensure efficient and safe
operation.
14.2.12 That the red instructions for safe use have been pointed out and understood.
14.2.13 That expert help must be obtained if persistent “LOCKOUT” occurs.
15. MAINTENANCE
NOTE: It is recommended that this appliance be serviced at intervals of no less than 12 months.
IMPORTANT: Ensure that the gas and electricity supplies are isolated before commencing any maintenance or
replacement of components. Because the appliance is room sealed, it is also imperative that if at any stage of repairs
the gasket on the sealing plate is damaged it MUST be replaced! After completion of any maintenance, always test
for gas soundness and carry out a complete functional test of the appliance in accordance with the Commissioning
Instructions at paragraphs 11.1 to 11.6 inclusive.
15.1 ROUTINE MAINTENANCE
15.1.1 Operate the appliance and check for the correct function of the burner and controls.
15.1.2 Turn OFF the gas and electrical supplies to the appliance.
15.1.3 Remove the air heater front panel.
15.1.4 Remove and check the return air filter/cleaner for cleanliness, remove and clean the air circulation fan as
detailed in paragraph 15.6.
15.1.5 Remove the burner and controls assembly as detailed in paragraph 15.2, inspect and clean the main burner
and injector as necessary. Examine the main burner for cracks, including hairline cracks, exchanging the
burner as necessary.
15.1.6 Inspect and clear the ignition burner orifice.
Summary of Contents for ECONOMAIRE 32
Page 19: ...19 Telephone 01604 762881 FIGURE 12 CONTROL FLOWCHART 17 DIAGNOSIS FLOWCHARTS...
Page 20: ...www johnsonandstarley co uk 20 FIGURE 13 AIR HEATER DIAGNOSIS FLOWCHART...
Page 21: ...21 Telephone 01604 762881 FIGURE 14 CONTROL FLOWCHART...
Page 22: ...www johnsonandstarley co uk 22 18 LOGIC DIAGRAM FIGURE 15 LOGIC DIAGRAM...
Page 23: ...23 Telephone 01604 762881 3 19 SCHEMATIC DIAGRAM FIGURE 16 SCHEMATIC DIAGRAM...
Page 25: ...25 Telephone 01604 762881 21 DIMENSIONS FIGURE 18 DIMENSIONS...
Page 27: ...27 Telephone 01604 762881 FIGURE 19 EXPLODED DIAGRAM 23 EXPLODED DIAGRAM...
Page 31: ......