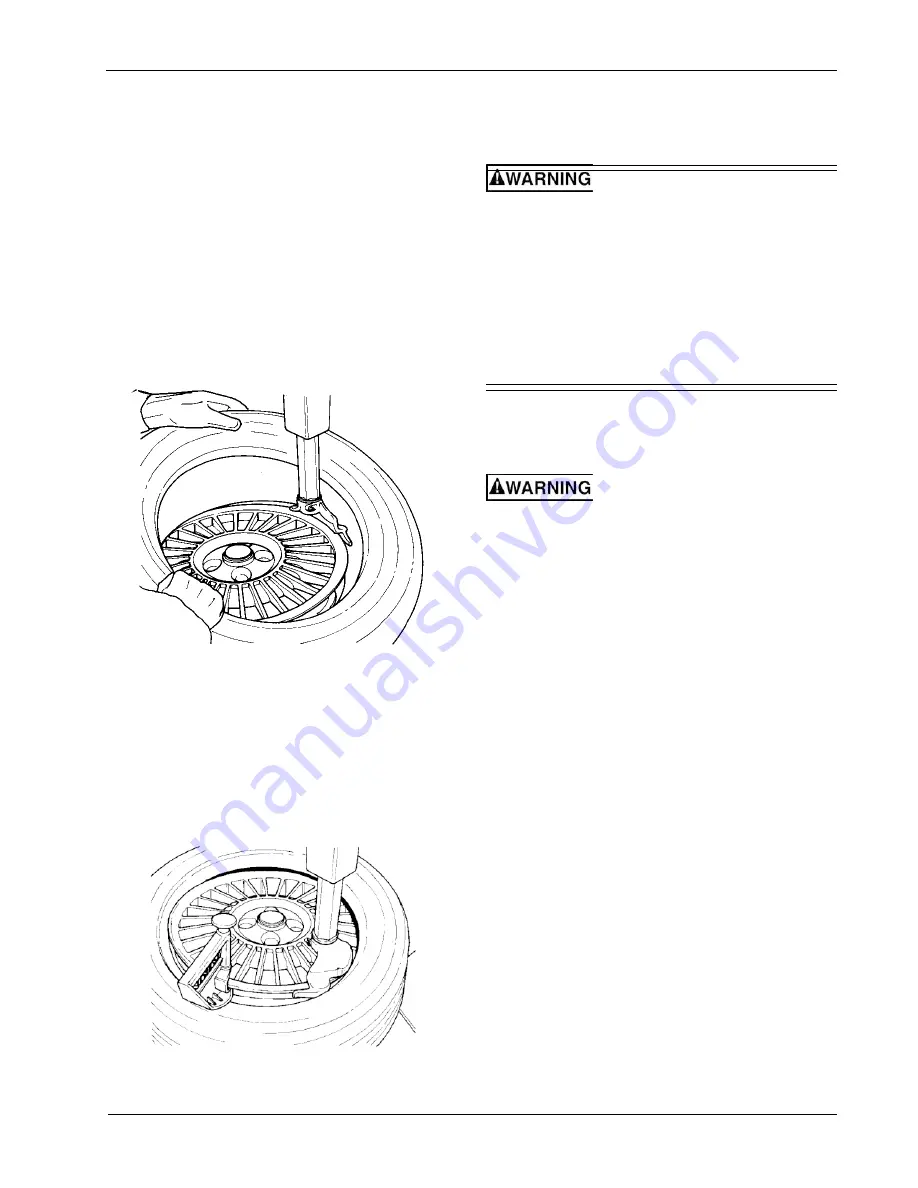
- Page 21 -
EHP Series Operation Instructions
NOTICE!
SOME TIRES HAVE A COLOR DOT THAT IS TO BE KEPT
ON THE OUTSIDE OF THE WHEEL AND IS TO BE ALIGNED
WITH THE VALVE STEM. IF THIS IS THE CASE BE SURE
TO ATTAIN PROPER ALIGNMENT PRIOR TO TIRE INFLA-
TION.
B. Lock the rim to the turntable and rotate it so that the
valve is at the 2 o’clock position. Place the tire to be
mounted on the rim. Swing the mount/demount arm in
so that the mount/demount head is in the working po-
sition. (Fig. 20) Engage the lower bead OVER the
mount/demount head and UNDER the mounting fin-
ger of the mount/demount head (Fig.20). Turn the
wheel clockwise (right pedal down) while simulta-
neously pushing the tire down into the drop center,
opposite to the mount/demount head.
338
Fig.20
C. Mount the upper bead following the directions in sec-
tion B. With low profile tires the bead holding clamp
(option 66735 Fig.21) can help to prevent the top bead
from prematurely seating during the mounting cycle.
NOTE: Bead Holding Clamp must be removed prior to
coming full circle and impacting the mount/demount
head.
39
Fig.21
4.3 INFLATION OF TUBELESS TIRES.
Make sure that both beads are properly lubricated.
BEAD SEATING IS THE MOST DANGEROUS PART OF
MOUNTING A TIRE.
NEVER STAND OVER TIRE WHEN ATTEMPTING TO SEAT
BEADS OR DURING INFLATION
IT IS POSSIBLE TO INCORRECTLY MOUNT TIRES THAT
ARE 1/2" SMALLER IN DIAMETER THAN THE RIM THAT
THEY ARE MOUNTED ON. WHILE THESE BEADS WILL
SEAL, IT IS IMPOSSIBLE TO GET THEM TO SEAT IN
THEIR PROPER POSITION.
EXPLOSION OF A TIRE MAY CAUSE SEVERE INJURY OR
DEATH.
Inflate tire according to manufacturers recommenda-
tions.
SAFETY RESTRAINT ARM MUST BE IN PLACE PRIOR
TO ATTEMPTING BEAD SEATING OR INFLATION.
NEVER EXCEED THE MAXIMUM PRESSURE ALLOWED
BY THE TIRE MANUFACTURER.
THE RIM MUST BE UNCLAMPED WHEN INFLATING BUT
ONLY AFTER THE BEADS HAVE BEEN SEATED.
THE OPERATOR MUST STAND CLEAR FROM THE
WHEEL WHEN INFLATING, AND PRESSURE MUST BE
MONITORED FREQUENTLY TO AVOID OVER INFLATION.
BEFORE INFLATING A TIRE, CHECK THE CONDITION OF
THE TIRE AND THE RIM.
Due to unusual configurations or the stacking of tires
the inflation process may be difficult. To assist with this
problem the JBC EHP Series Tire Changers are
equipped with bead seater jets integrated into the table
top.
To utilize the bead seater proceed as follows:
A. Position the safety restraint arm over center of wheel
assembly. The safety arm is lifted upward by grasping
the safety restraint position knob and lifting upward while
simultaneously depressing the anti-rotation lock arm.
Swing safety arm assembly so the circular retainer is
centered over the rim. Note that air pressure to the
inflation hose will not flow until the arm is centered over
the rim.
B. If possible lock the wheel from inside. Outside lock-
ing reduces efficiency.
For Reference Only
For Current Info See Equiserv.com
Summary of Contents for EHP System I
Page 2: ... BLANK PAGE For Reference Only For Current Info See Equiserv com ...
Page 4: ... BLANK PAGE For Reference Only For Current Info See Equiserv com ...
Page 26: ... BLANK PAGE For Reference Only For Current Info See Equiserv com ...
Page 27: ... BLANK PAGE For Reference Only For Current Info See Equiserv com ...