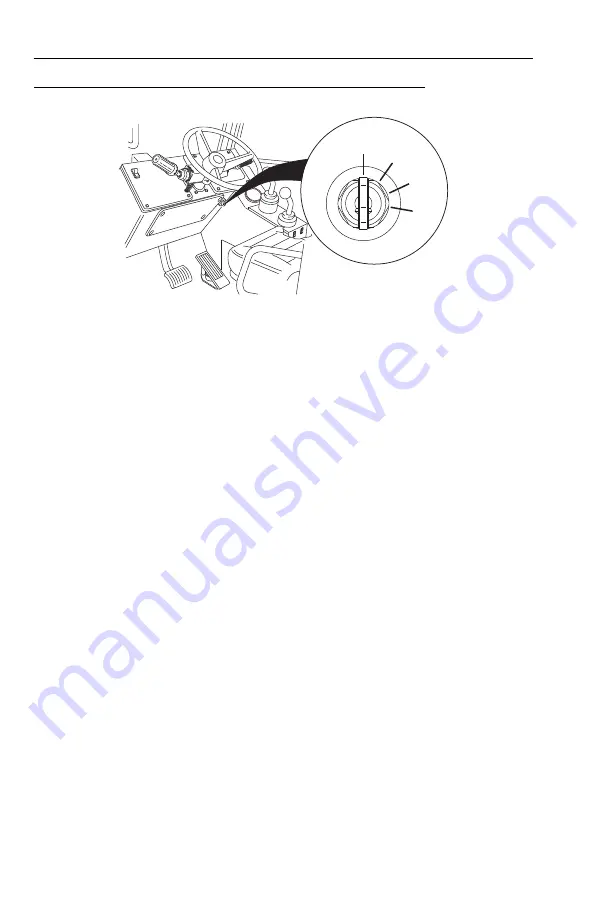
Section 3 - Controls and Indicators
3-6
31200749
Ignition
• Position
0
- Engine off, no voltage available.
• Position
1
- Voltage available for all electrical functions. Wait to start engine until
engine pre-heat indicator light goes out.
• Position
P
- Engine run.
• Position
2
- Engine start. In the event the engine does not start, rotate key to
position 0 then back to position 2 to re-engage the starter.
OH4
7
4
0
0
1
P
2
Summary of Contents for Skytrak 10042
Page 3: ...Revision Log a 31200749 Revision Log REVISION LOG March 30 2012 A Original Issue of Manual ...
Page 24: ...Section 1 General Safety Practices 1 14 31200749 This Page Intentionally Left Blank ...
Page 33: ...Section 2 Pre Operation and Inspection 2 9 31200749 This Page Intentionally Left Blank ...
Page 70: ...Section 4 Operation 4 12 31200749 This Page Intentionally Left Blank ...
Page 75: ...Section 5 Attachments 5 5 31200749 This Page Intentionally Left Blank ...
Page 79: ...Section 5 Attachments 5 9 31200749 This Page Intentionally Left Blank ...
Page 106: ...Section 5 Attachments 5 36 31200749 This Page Intentionally Left Blank ...
Page 116: ...Section 7 Lubrication and Maintenance 7 8 31200749 10054 OH4242 50 EVERY ...
Page 118: ...Section 7 Lubrication and Maintenance 7 10 31200749 8042 10042 10054 OH4172 EVERY 250 ...
Page 148: ...Index 4 31200749 ...
Page 150: ...Inspection Maintenance and Repair Log Date Comments ...
Page 152: ......