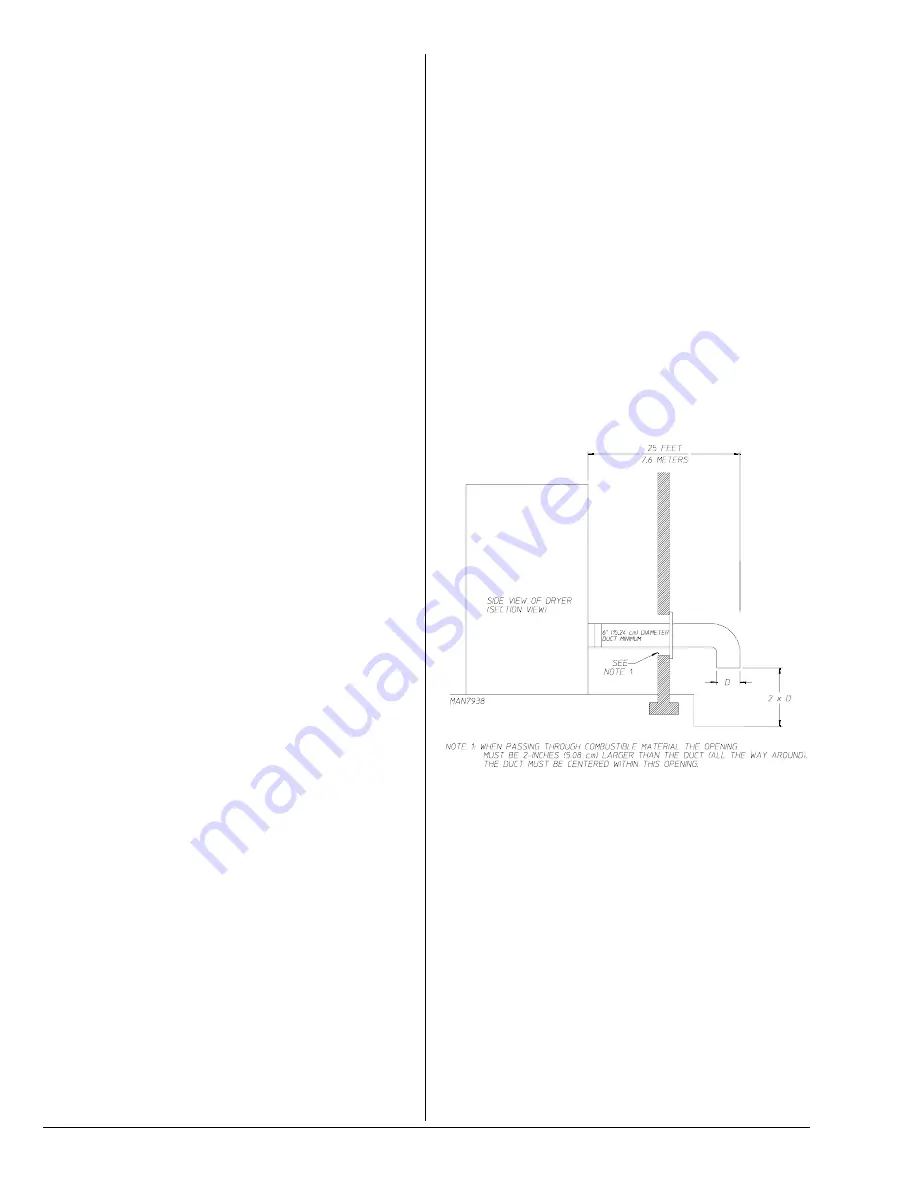
14
JLA Limited
113538 - 7
Exhaust Requirements ________________
Exhaust ductwork should be designed and installed by a
qualified professional. Improperly sized ductwork will create
excessive back pressure, which results in slow drying,
increased use of energy, and shutdown of the burner by the
airflow (sail) switch, burner hi-limits, or lint chamber hi-limit
protector thermostat. The dryer must be installed with a proper
exhaust duct connection to the outside.
The dryer shall not be exhausted into any gas vent, chimney,
wall, ceiling or concealed space of a building.
The design of the flue system shall be such that any
condensate formed when operating the appliance from cold
shall either be retained and subsequently re-evaporated or
discharged.
CAUTION: This dryer produces combustible lint and
must be exhausted to the outdoors.
Improperly sized or installed exhaust ductwork can
create a potential fire hazard.
The ductwork should be laid out in such a way that the
ductwork travels as directly as possible to the outdoors with
as few turns as possible. There should be a minimum
6-inch (15.24 cm) clearance between the back guard and the
first bend in the ductwork for ease of servicing. Single or
independent dryer venting is recommended. It is suggested
that the use of 90° turns be avoided; use 30° and/or 45° bends
instead. The radius of the elbows should preferably be 1-1/2
times the diameter of the duct. All ductwork should be smooth
inside with no projections from sheet metal screws or other
obstructions, which will collect lint. When adding ducts,
overlap the duct being connected. All ductwork joints must
be taped to prevent moisture and lint from escaping into the
building. Back draft dampers must be installed in all commonly
ducted systems. Inspection doors should be installed at
strategic points in the exhaust ductwork for periodic inspection
and cleaning of lint from the ductwork.
IMPORTANT:
Exhaust back pressure measured by a
manometer/magnehelic in the exhaust duct must be no less
than 0 and must not exceed 0.6 in WC (1.5 mb).
NOTE:
It is recommended that exhaust or booster fans not
be used in the exhaust ductwork system except where
necessary to maintain exhaust back pressure (in the
exhaust duct) between zero and 0.6 inch water column.
Where employed, booster fans must not activate the dryer
airflow proving switch (sail switch) when the dryer is not in
operation.
NOTE:
When the exhaust ductwork passes through a wall,
ceiling, or roof made of combustible materials, the opening
must be 2-inches (5.08 cm) larger than the duct (all the way
around). The duct must be centered within this opening.
As per the National Fuel Gas Code, “Exhaust ducts for type
2 clothes dryers shall be constructed of sheet metal or other
noncombustible material. Such ducts shall be equivalent in
strength and corrosion resistance to ducts made of
galvanized sheet steel not less than 26 gauge
(0.0195-inches [0.50 mm]) thick.”
The ductwork for this appliance must be suitable for the
appliance category in accordance with national installation
regulations of the country of destination.
Outside Ductwork Protection
To protect the outside end of the horizontal ductwork from the
weather, a 90° elbow bent downward should be installed where
the exhaust exits the building. If the ductwork travels vertically
up through the roof, it should be protected from the weather
by using a 180° turn to point the opening downward. In either
case, allow at least twice the diameter of the duct between
the duct opening and the nearest obstruction (refer to the
diagram).
IMPORTANT:
Do not use screens, louvers, or caps on the
outside opening of the exhaust ductwork.
Single Dryer Venting (SD35)
IMPORTANT:
For the SD35, a minimum exhaust duct size
of 6-inches (15.24 cm) must be used.
For a 6-inch (15.24 cm) horizontal run where a maximum of
one elbow is used, the ductwork from the dryer outlet must
not exceed dimension “A” in the following illustration.
SD35 ONLY
HORIZONTAL SINGLE DRYER VENTING
6-INCH (15.24 CM) DUCTING
If the length of the duct run or quantity of elbows used exceeds
the above noted specifications, the cross-sectional area of
the ductwork may need to be increased.
IMPORTANT:
For extended ductwork runs, the cross
section area of the ductwork can only be increased to an
extent. When the ductwork approaches the maximum limits
noted in this manual, a professional HVAC firm should be
consulted for proper venting information.
Single Dryer Venting (SD35, SD50, SD80)
IMPORTANT:
A minimum exhaust duct size of 8-inches
(20.32 cm) must be used.
For an 8-inch (20.32 cm) horizontal run where a maximum of
one elbow is used, the ductwork from the dryer outlet must
not exceed dimension “A” in the following illustration on the
next page.