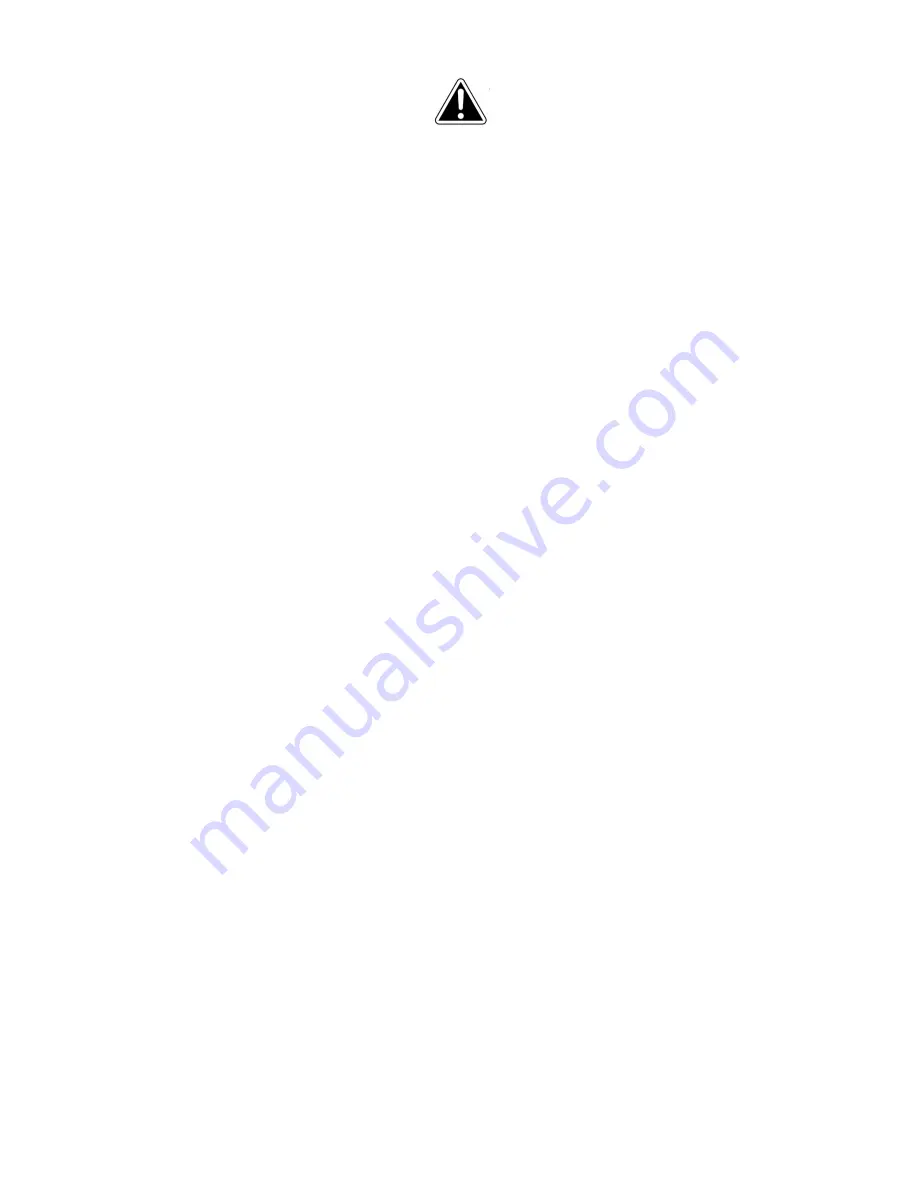
2
1.0
IMPORTANT SAFETY INSTRUCTIONS
WARNING – To reduce risk of injury:
1. Read and understand the entire owner's manual before attempting assembly or operation.
2. Read and understand the warnings posted on the machine and in this manual. Failure to comply with
all of these warnings may cause serious injury.
3. Replace the warning labels if they become obscured or removed.
4. This Woodworking Jointer is designed and intended for use by properly trained and experienced
personnel only. If you are not familiar with the proper and safe operation of a woodworking jointer, do
not use until proper training and knowledge have been obtained.
5. Do not use this Jointer for other than its intended use. If used for other purposes, JET disclaims any
real or implied warranty and holds itself harmless from any injury that may result from that use.
6. Always wear approved safety glasses/face shields while using this woodworking jointer. Everyday
eyeglasses only have impact resistant lenses; they are not safety glasses.
7. Before operating this woodworking jointer, remove tie, rings, watches and other jewelry, and roll
sleeves up past the elbows. Remove all loose clothing and confine long hair. Non-slip footwear or
anti-skid floor strips are recommended. Do
not
wear gloves.
8. Wear ear protectors (plugs or muffs) during extended periods of operation.
9. Do not operate this machine while tired or under the influence of drugs, alcohol or any medication.
10. Make certain the switch is in the
OFF
position before connecting the machine to the power source.
11. Make certain the machine is properly grounded.
12. Make all machine adjustments or maintenance with the machine unplugged from the power source.
13. Remove adjusting keys and wrenches. Form a habit of checking to see that keys and adjusting
wrenches are removed from the machine before turning it on.
14. Keep safety guards in place at all times when the machine is in use. If removed for maintenance
purposes, use extreme caution and replace the guards immediately.
15. Make sure the woodworking jointer is firmly secured to the floor or bench before use.
16. Check damaged parts. Before further use of the machine, a guard or other part that is damaged
should be carefully checked to determine that it will operate properly and perform its intended
function. Check for alignment of moving parts, binding of moving parts, breakage of parts, mounting
and any other conditions that may affect its operation. A guard or other part that is damaged should
be properly repaired or replaced.
17. Provide for adequate space surrounding work area and non-glare, overhead lighting.
18. Keep the floor around the machine clean and free of scrap material, oil and grease.
19. Keep visitors a safe distance from the work area.
Keep children away.
20. Make your workshop child proof with padlocks, master switches or by removing starter keys.
21. Give your work undivided attention. Looking around, carrying on a conversation and “horse-play” are
careless acts that can result in serious injury.
22. Maintain a balanced stance at all times so that you do not fall or lean against the cutterhead or other
moving parts. Do not overreach or use excessive force to perform any machine operation.
23. Use the right tool at the correct speed and feed rate. Do not force a tool or attachment to do a job for
which it was not designed. The right tool will do the job better and safer.
24. Use recommended accessories; improper accessories may be hazardous.
Summary of Contents for 708457DXJ
Page 27: ...27 15 1 1 Fence Assembly All Models Exploded View ...
Page 29: ...29 15 2 1 Stand Assembly JJ 6CSDX Exploded View ...
Page 31: ...31 15 3 1 Stand Assembly JJ 6HHDX only Exploded View ...
Page 33: ...33 15 4 1 Bed Assembly All models Exploded View ...
Page 37: ...37 16 0 Wiring diagrams All Models ...
Page 39: ...39 This page intentionally left blank ...
Page 40: ...40 427 New Sanford Road LaVergne Tennessee 37086 Phone 800 274 6848 www jettools com ...