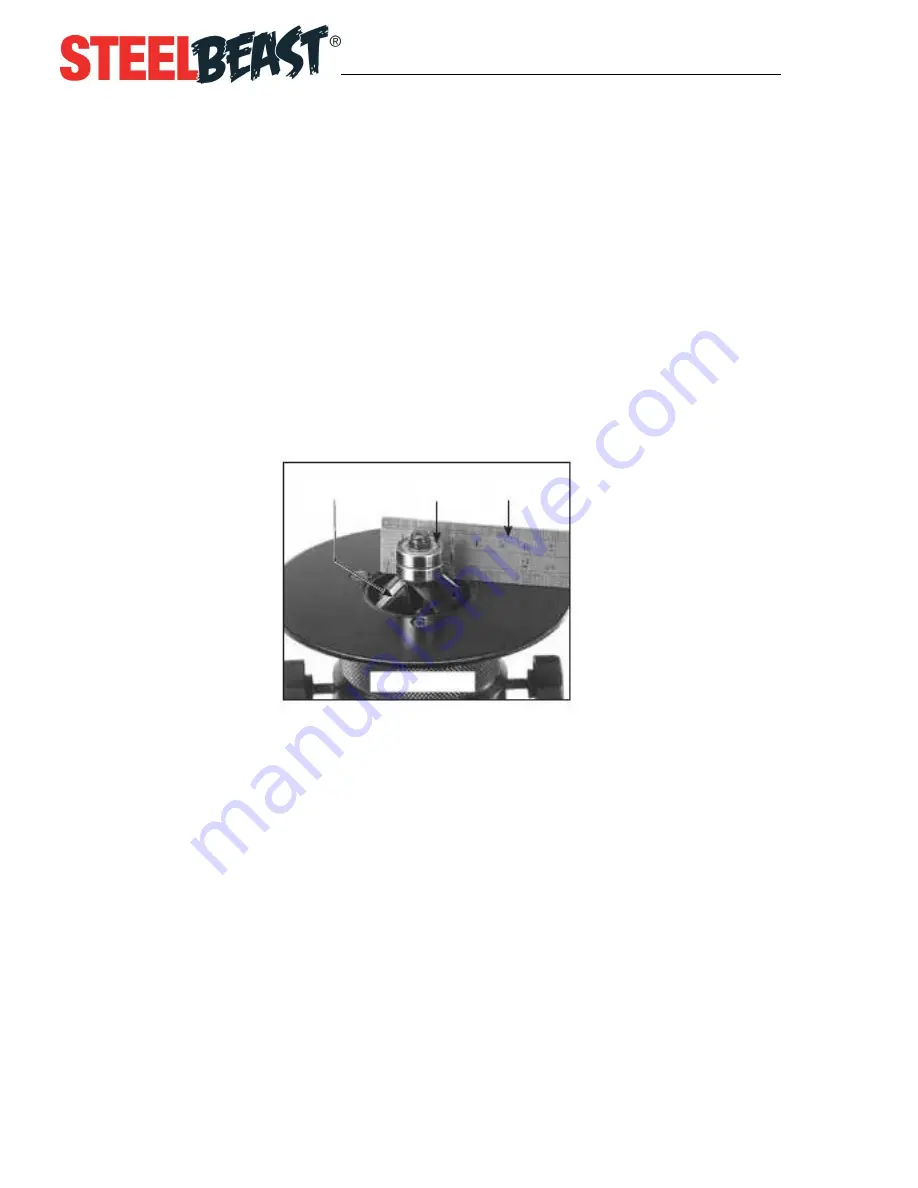
BM-12 Bevelling Machine
- 7 -
ZEROING-IN THE CHAMFER HEIGHT –
DISCONNECT TOOL FROM POWER SOURCE.
Note: The machine’s chamfer height is set at zero from the factory. If the setting
is disturbed, it must be zeroed in. Follow the instructions below for zeroing-in.
1. Loosen the 2 lock knobs then loosen the support deck assembly so that the
inserts are below flush level.
2.
Use a steel ruler or other accurate device with a right angle. While keeping the
ruler square with the impeller and the support deck, slowly adjust the support
deck until the ruler just touches the carbide insert. This is the zero point.
3. Once the zero point is found, loosen the small set screw and turn the dial ring
to indicate zero on the scale. Then retighten the set screw.
CHANGING THE INDEXABLE CABIDE INSERTS – DISCONNECT TOOL
FROM POWER SOURCE.
WARNING: Danger of Burns! Tool holder and carbide inserts become hot in
operation. Wear gloves and take precautions to prevent burns when working with
this part of the machine.
Note: indexable carbide inserts have multiple edges. When one edge is dull
simply rotate to the next sharp edge. Once all edges are dull, replace with new
inserts.
NOTE: Make sure the indexable carbide inserts are installed in the correct
direction, incorrect installation of the indexable carbide inserts can cause the
failure of chamfering or even rupture of the indexable carbide inserts. Please
refer to the front of the machine for rotating direction, and install the indexable
carbide inserts accordingly.
Impeller
Carbide Insert
Ruler
Summary of Contents for SteelBeast BM-12
Page 13: ...BM 12 Bevelling Machine 12 ...
Page 14: ...BM 12 Bevelling Machine 13 ...
Page 15: ...BM 12 Bevelling Machine 14 ...