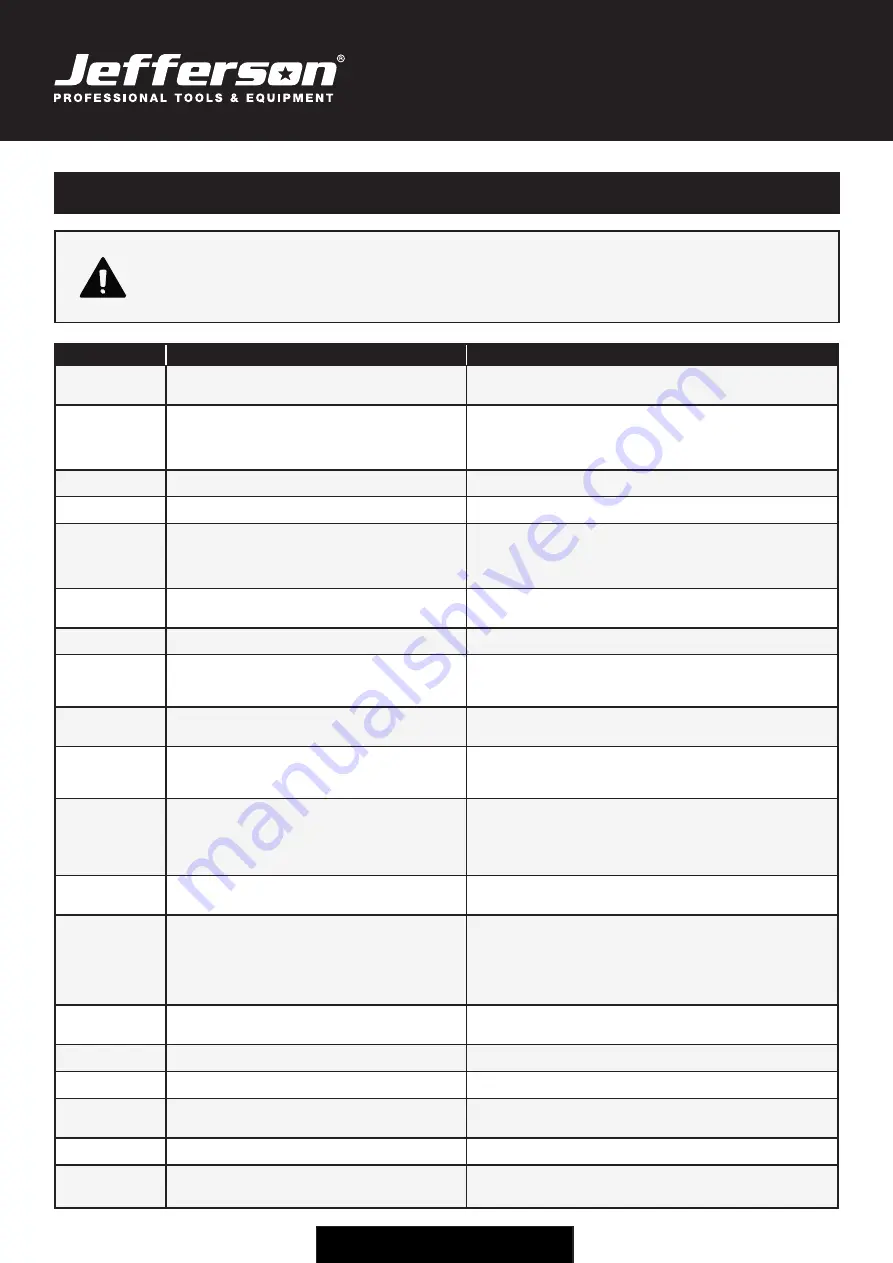
18
USER MANUAL
JEFMIG151-A
151A MIG WELDER - 230V 50Hz
www.jeffersontools.com
WARNING:
Be certain to shut off the welder, disconnect it from power, and discharge the torch to ground before
adjusting, cleaning, or repairing the unit. Electrical repairs should only be made by a trained technician.
Symptom
Possible Cause
Corrective Action
No output
1. Duty cycle exceeded
2. Poor work clamp connection
3. Blown breaker or fuse
1. Allow welder to cool until lamp goes out
2. Be sure all connections are secure, and attaching surface is clean
3. Reduce circuit load, reset breaker or replace fuse
Wire tangles at
drive roller
1. Wrong size contact tip
2. Torch liner clogged or damaged
3. Contact tip clogged or damaged
4. Drive roller worn
5. Not enough tension
1. Use proper size contact tip
2. Clean or replace wire liner
3. Clean or replace contact tip
4. Replace drive roller
5. Tighten tension knob
Gun nozzle arcs to
work surface
1. Slag inside gun nozzle
2. Insulation ring melted or expired
1. Clean slag from gun nozzle
2. Replace nozzle
Work clamp and/or
cable gets hot
1. Poor contact
2. Using an extension cord with excessive length
1. Be sure all connections are secure, and welding surface is clean
2. Never use an extension cord longer than 20ft
Wire does not feed
1. Wire jammed
2. Out of wire
3. Not enough tension
4. Wire liner worn
5. Contact tip clogged
1. Reload wire
2. Replace wire spool
3. Tighten tension knob if wire is slipping
4. Replace liner
5. Replace contact tip
Weld pops and
sputters
1. Wire speed setting
2. Contact tip size too large
3. Drive roller slipping
1. Tune in correct setting
2. Replace contact tip
3. Increase tension
Weld current
interrupted
1. Overheating protection activated due to overload
1. Protection automatically resets when transformer has cooled
(approximately 15 minutes)
No weld current
1. Rectifier blown
2. Bad connection between clamp and workpiece
3. Break in earth lead
4. Break in torch lead
1. Replace rectifier
2. Clean or grind contact surface and weld area
3. Repair or replace earth lead
4. Repair or replace torch lead
Feed motor
not working
1. Gear damaged or worn
2. Motor defective
3. PCB fault
1. Replace gears
2. Replace motor (contact service agent)
3. Replace PCB
Wire does not feed.
Feed roller rotates
1. Pressure roller improperly adjusted
2. Dirt, copper, dust, etc. have collected in torch liner
3. Gas cup (nozzle) or tip defective
4. Deformed wire
1. Adjust tension
2. Clean the liner from the machine forward using compressed air
3. Replace gas cup (nozzle) and/or tip. Check roller tension (Sec 6)
4. Adjust roller tension
Wire feeds unevenly
1. Dirt etc. in liner
2. Gas cup (nozzle) or tip defective
3. Gas cup (nozzle) spattered
4. Feed roller groove clogged
5. Feed roller groove deformed
6. Pressure roller tension incorrect
1. Clean the liner from the machine forward using compressed air
2. Replace gas cup (nozzle) and/or tip
3. Clean or replace gas cup (nozzle)
4. Clean feed roller
5. Replace feed roller
6. Adjust tension
Unstable arc
1. Incorrect settings
2. Impurities in weld area
3. Worn or defective gas cup (nozzle)
1. Check settings
2. Clean and/or grind workpiece
3. Replace gas cup (nozzle)
Porous weld
1. No gas
2. Gas cup clogged
3. Draught blowing away shielding gas
4. Rusty/dirty joints
5. Torch too far from, or at wrong angle to, workpiece
6. Gas leak
7. Faulty electrovalve
1. Open gas cylinder, regulate gas flow
2. Clean or replace gas cup (nozzle)
3. Screen off welding site or increase gas flow
4. Clean and/or grind workpiece
5. Gas cup to workpiece should be 8-10mm. Torch angle approx 75°
6. Check hoses, connections and torch assembly. Press gas cup into position
7. Clean out or replace
Electrode sticking
in gas cup (nozzle)
1. Worn or defective gas cup (nozzle)
2. Wire deformed
3. Wire speed too slow
1. Replace gas cup (nozzle)
2. Check roller tension
3. Increase wire speed
Irregular
weld head
1. Torch incorrectly held
2. Wire weaving in weld pool
1. Use correct torch angle
2. Check roller tension and adjust
Weld bead too
narrow and raised
1. Weld current too low
2. Weld speed too fast
1. Increase power and wire speed
2. Move torch more slowly and weave a little more
Weld bead too wide
1. Weld current too high
2. Weld speed too slow
3. Arc too long
1. Increase power and wire speed
2. Move torch more quickly and weave a little less
3. Bring torch closer to workpiece
Poor penetration
1. Weld current too low
2. Arc too long
1. Increase current and wire speed
2. Bring torch closer to workpiece
Excessive
penetration
1. Weld current too high
2. Weld speed too slow
3. Incorrect distance of torch to workpiece
1. Decrease current and wire speed
2. Move torch faster
3. Torch distance should be 8-10mm
15. Troubleshooting