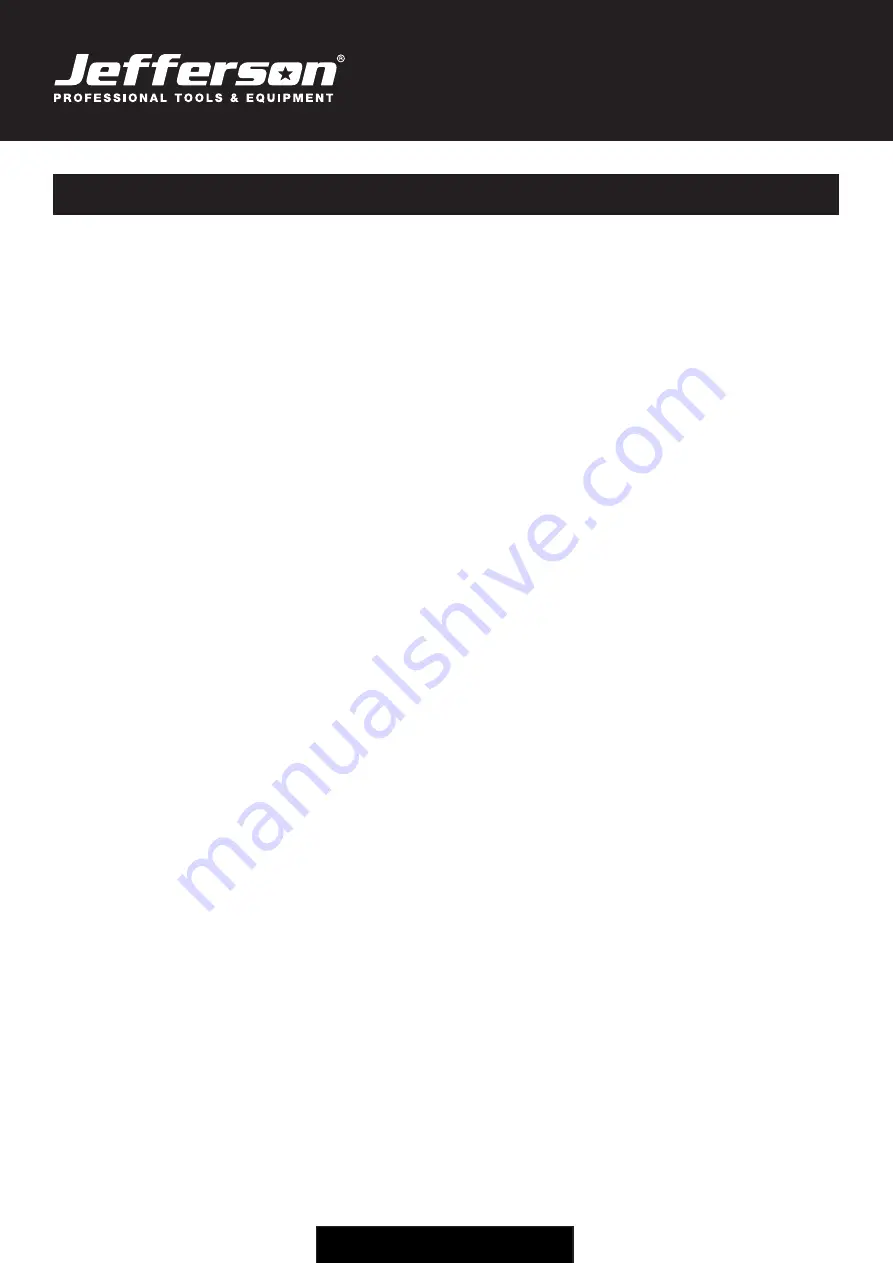
14
USER MANUAL
JEFMIG151-A
151A MIG WELDER - 230V 50Hz
www.jeffersontools.com
PRECAUTIONS
•
Ensure that there is free air circulating around the outer casing of the welder, and that the air vents are unobstructed.
•
Welding arc can seriously damage your eyes. Both the operator and spectators must always use a suitable welding face
shield or helmet, with suitable filter lenses for the welding processes.
•
Suitable Personal Protection Equipment (PPE) including gloves and working clothes should be worn at all times.
•
Always check and ensure that the pressure regulator and gauges (if fitted) are working correctly before use.
•
Regulators are designed to be used with specific gases, it is important that you use the correct regulator for the gas required.
•
Do not lubricate the regulator.
•
Inspect gas hoses, cables and clamps before use to ensure they are in good condition.
•
Remove all flammable materials from the working environment before use.
•
Keep a fire extinguisher nearby at all times. The extinguisher should be Dry Powder or CO
2
type.
•
Do not remove any of the casing panels for repair or maintenance unless the machine is disconnected from the supply,
and never use the machine with any of the panels removed. All repairs should be carried out by qualified engineers using
Jefferson approved parts. Contact your nearest Jefferson Dealer for details.
•
Never use or store this equipment in a wet or damp environment and do not expose the equipment to rain during use.
•
The MIG welding process uses an inert gas to protect the weld pool. It is important to ensure the appropriate gas is being used.
•
Never use an unknown or unidentifiable gas supply or gas from a damaged or unmarked cylinder.
•
Do not lift or move a gas cylinder by holding he cylinder by the valve.
•
Do not expose the cylinder to a heat source or sparks while in storage or in use.
•
Stop welding immediately if any static / electric shocks are felt or detected. Do not attempt to weld using the equipment until
the source of the fault is identified and repaired.
•
Do not point the MIG torch at anyone when in use.
•
Do not touch the MIG torch nozzle until the welder is switched
OFF
and the nozzle has been allowed to cool off.
•
Never connect, disconnect, or attempt to service the MIG torch, until the machine is switched
OFF
and disconnected from
the mains power supply.
•
Never allow the equipment cables to become wrapped around the operator or any bystanders in the working environment.
12. Welding Guidelines
IMPORTANT:
These instructions are not intended to teach you how to weld. If you have no experience, we recommend that you
seek training from an expert source. MIG welding is relatively easy, but does require a steady hand and supervised practice on
scrap metal, as it is only with continued practice that you will achieve the desired results.
12.1
Mig/Mag welding:
Welding wire is automatically fed through an insulated liner to the tip of the torch. The torch consists of a switch, liner,
and control cable. The switch activates the wire feed roller. Releasing the switch stops wire feed. The weld current is
transferred to the electrode (the wire) from the contact tip at the torch end. The current to the electrode is set using the
rocker switch on the front of the control panel. Wire speed must be adjusted according to current output using the rotary
control positioned to the left of the control panel. The higher the current the faster the wire speed. The torch is connected
to the positive side of a DC rectifier, and the negative clamp is attached to the workpiece.
12.2
Preparation for welding:
IMPORTANT!
BEFORE YOU COMMENCE, MAKE SURE THE MACHINE IS SWITCHED OFF
AT THE MAINS. IF WELDING A CAR, DISCONNECT THE BATTERY OR FIT AN ELECTRONIC CIRCUIT PROTECTOR.
ENSURE THAT YOU READ, UNDERSTAND AND APPLY THE SAFETY INSTRUCTIONS IN SECTION 3.
12.2.1 To ensure a complete circuit, the negative lead must be securely attached to the workpiece close to the weld area. Best
connection is obtained by grinding the point of contact on the workpiece before connecting the clamp.
12.2.2 The weld area must be free of paint, rust, grease, etc.
12.3
Thermal Protection:
Should the welder become overheated due to prolonged use beyond the stated duty cycle the thermal protection will
cause the welder to cut out and the orange light on the front panel will illuminate (as shown in
Fig.9
on page 11).
Wait for fifteen minutes for the welder to cool down at which time it will reconnect automatically.