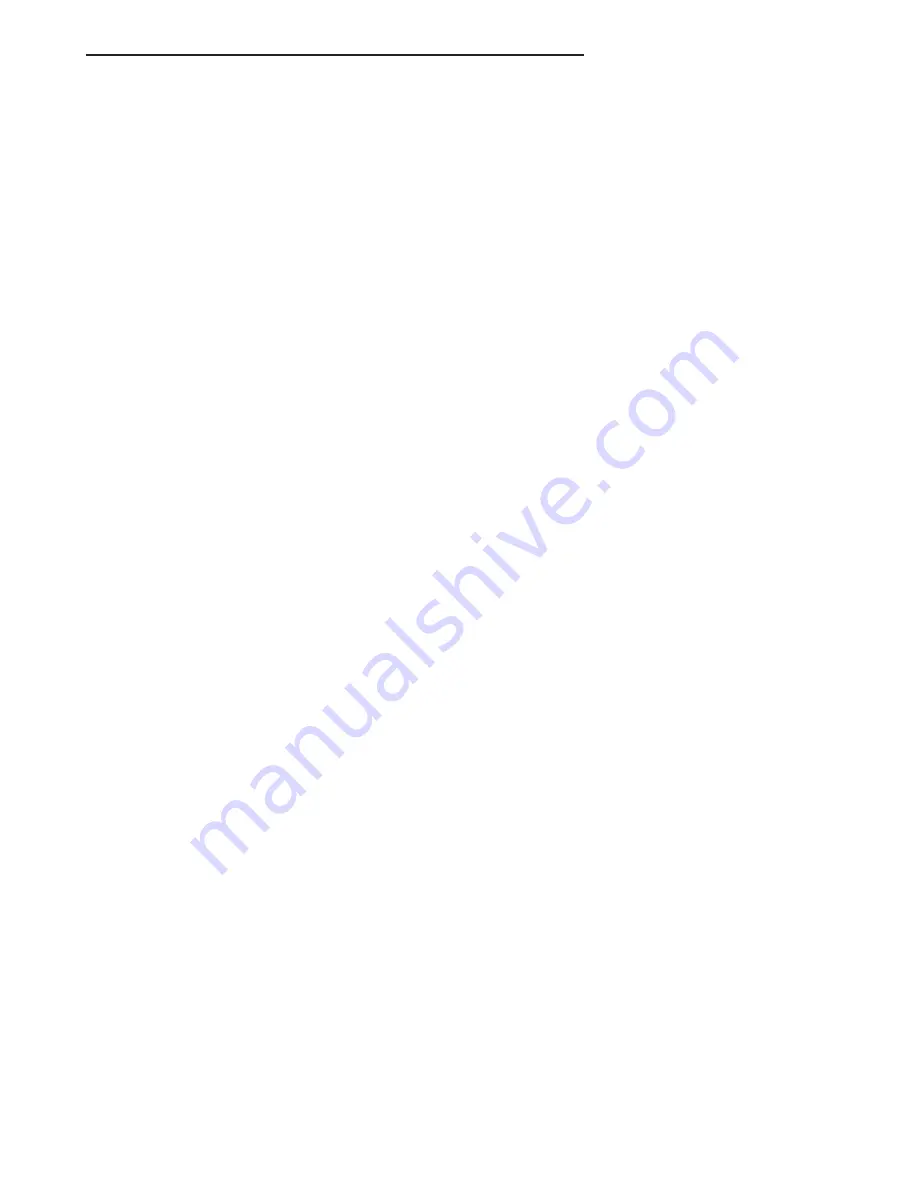
FRONT CLUTCH
OPERATION
To apply the clutch, pressure is applied between
the clutch retainer and piston. The fluid pressure is
provided by the oil pump, transferred through the
control valves and passageways, and enters the
clutch through the hub of the reaction shaft support.
With pressure applied between the clutch retainer
and piston, the piston moves away from the clutch
retainer and compresses the clutch pack. This action
applies the clutch pack, allowing torque to flow
through the input shaft into the driving discs, and
into the clutch plates and pressure plate that are
lugged to the clutch retainer. The waved snap-ring is
used to cushion the application of the clutch pack.
When pressure is released from the piston, the
spring returns the piston to its fully released position
and disengages the clutch. The release spring also
helps to cushion the application of the clutch assem-
bly. When the clutch is in the process of being
released by the release spring, fluid flows through a
vent and one-way ball-check-valve located in the
clutch retainer. The check-valve is needed to elimi-
nate the possibility of plate drag caused by centrifu-
gal force acting on the residual fluid trapped in the
clutch piston retainer.
DISASSEMBLY
(1) Remove waved snap-ring and remove pressure
plate, clutch plates and clutch discs (Fig. 67).
(2) Compress clutch piston spring with Compressor
Tool C-3575-A (Fig. 68). Be sure legs of tool are
seated squarely on spring retainer before compress-
ing spring.
(3) Remove retainer snap-ring and remove com-
pressor tool.
(4) Remove spring retainer and clutch spring. Note
position of retainer on spring for assembly reference.
(5) Remove clutch piston from clutch retainer.
Remove piston by rotating it up and out of retainer.
(6) Remove seals from clutch retainer piston bore
and clutch retainer hub. Discard both seals as they
are not reusable.
ASSEMBLY
(1) Soak clutch discs in transmission fluid while
assembling other clutch parts.
(2) Install new seals in the clutch retainer lower
groove and on the outer diameter of the retainer hub.
Be sure lip of each seal faces interior of clutch
retainer.
(3) Lubricate lips of the retainer seals with liberal
quantity of Mopar
t
Door Ease. Then lubricate
retainer hub, bore, and piston with light coat of
transmission fluid.
(4) Install clutch piston in retainer (Fig. 69). Use
twisting motion to seat piston in bottom of retainer.
CAUTION: Never push the clutch piston straight in.
This will fold the seals over causing leakage and
clutch slip.
TJ
AUTOMATIC - 32RH
21s - 111
Summary of Contents for 2001 Wrangler TJ
Page 5: ......
Page 15: ......
Page 73: ......
Page 103: ......
Page 119: ......
Page 120: ......
Page 121: ......
Page 122: ......
Page 123: ......
Page 124: ......
Page 125: ......
Page 126: ......
Page 127: ......
Page 128: ......
Page 129: ......
Page 130: ......
Page 131: ......
Page 132: ......
Page 133: ......
Page 134: ......
Page 135: ......
Page 137: ......
Page 138: ......
Page 139: ......
Page 140: ......
Page 141: ......
Page 142: ......
Page 143: ......
Page 144: ......
Page 145: ......
Page 147: ......
Page 148: ......
Page 149: ......
Page 150: ......
Page 151: ......
Page 152: ......
Page 153: ......
Page 154: ......
Page 155: ......
Page 156: ......
Page 157: ......
Page 158: ......
Page 159: ......
Page 161: ......
Page 163: ......
Page 164: ......
Page 165: ......
Page 167: ......
Page 168: ......
Page 169: ......
Page 171: ......
Page 172: ......
Page 173: ......
Page 174: ......
Page 175: ......
Page 176: ......
Page 177: ......
Page 178: ......
Page 179: ......
Page 180: ......
Page 181: ......
Page 182: ......
Page 183: ......
Page 184: ......
Page 185: ......
Page 186: ......
Page 187: ......
Page 188: ......
Page 189: ......
Page 191: ......
Page 193: ......
Page 194: ......
Page 195: ......
Page 197: ......
Page 198: ......
Page 199: ......
Page 200: ......
Page 201: ......
Page 202: ......
Page 203: ......
Page 204: ......
Page 205: ......
Page 207: ......
Page 208: ......
Page 209: ......
Page 211: ......
Page 212: ......
Page 213: ......
Page 215: ......
Page 216: ......
Page 217: ......
Page 219: ......
Page 220: ......
Page 221: ......
Page 222: ......
Page 223: ......
Page 224: ......
Page 225: ......
Page 227: ......
Page 228: ......
Page 229: ......
Page 231: ......
Page 233: ......
Page 234: ......
Page 235: ......
Page 236: ......
Page 237: ......
Page 238: ......
Page 239: ......
Page 240: ......
Page 241: ......
Page 243: ......
Page 244: ......
Page 245: ......
Page 246: ......
Page 247: ......
Page 248: ......
Page 249: ......
Page 250: ......
Page 251: ......
Page 253: ......
Page 254: ......
Page 255: ......
Page 256: ......
Page 257: ......
Page 259: ......
Page 260: ......
Page 261: ......
Page 263: ......
Page 264: ......
Page 265: ......
Page 266: ......
Page 267: ......
Page 268: ......
Page 269: ......
Page 315: ......
Page 347: ...Fig 1 HEADLAMP SPLICES 8Wa 95 4 8W 95 SPLICE LOCATIONS TJ SPLICE LOCATIONS Continued ...
Page 348: ...Fig 2 RIGHT HEADLAMP SPLICES TJ 8W 95 SPLICE LOCATIONS 8Wa 95 5 SPLICE LOCATIONS Continued ...
Page 355: ...Fig 13 INSTRUMENT PANEL RHD 8Wa 95 12 8W 95 SPLICE LOCATIONS TJ SPLICE LOCATIONS Continued ...
Page 356: ...Fig 14 DASH PANEL LHD TJ 8W 95 SPLICE LOCATIONS 8Wa 95 13 SPLICE LOCATIONS Continued ...
Page 357: ...Fig 15 DASH PANEL RHD 8Wa 95 14 8W 95 SPLICE LOCATIONS TJ SPLICE LOCATIONS Continued ...
Page 358: ...Fig 16 BODY WIRING SPLICES TJ 8W 95 SPLICE LOCATIONS 8Wa 95 15 SPLICE LOCATIONS Continued ...
Page 359: ...Fig 17 REAR LAMPS 8Wa 95 16 8W 95 SPLICE LOCATIONS TJ SPLICE LOCATIONS Continued ...
Page 367: ......