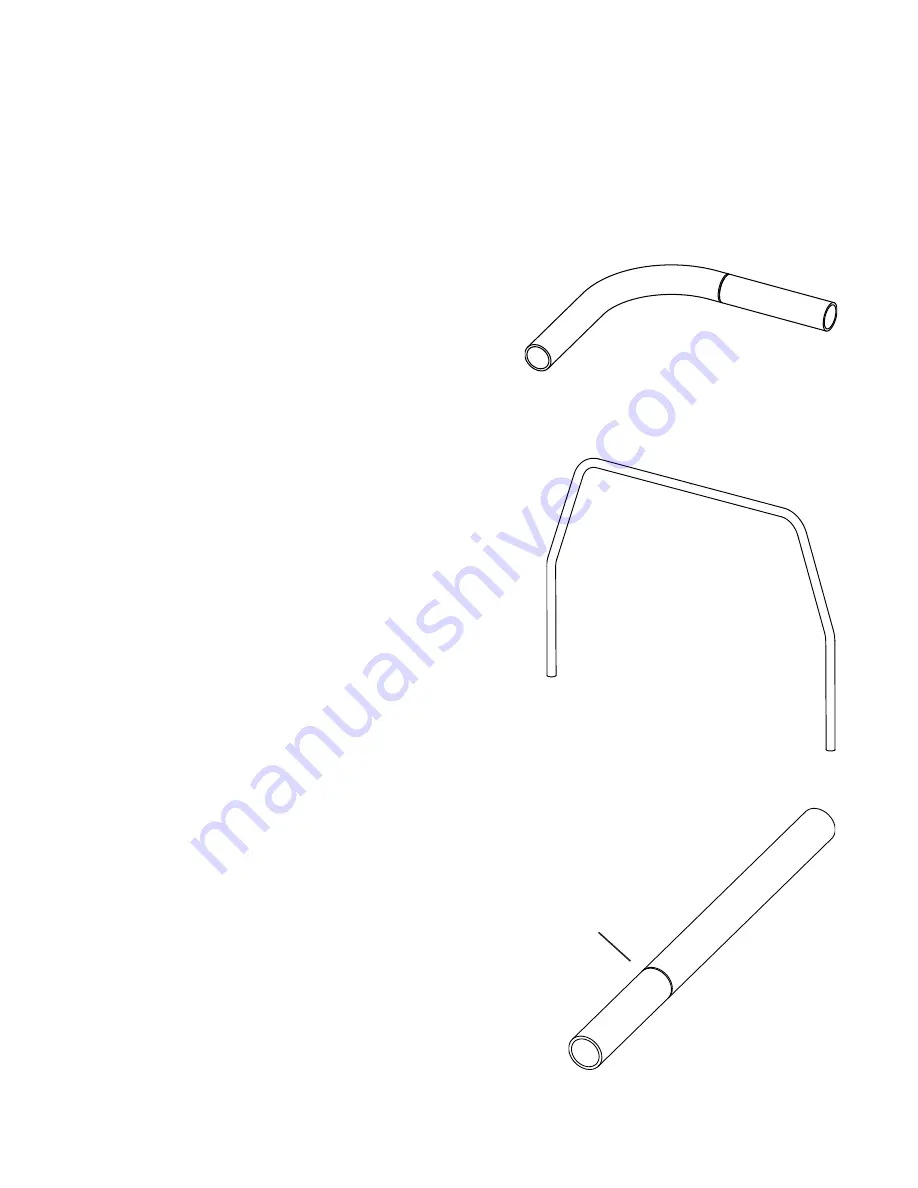
- 8 -
First, you need to make a template. For our example,
we are going to use 1 1/2” o.d. x .120” wall welded seam
mild steel tubing. As shown in Figure 15, the tem plate is a
piece of tubing bent to 90 degrees with approximately 6”
of straight tubing on each side of the bend. Cut a piece of
tubing roughly 30” long. Next, scribe an accurate line all
the way around this tubing 6” from the end. An accurate
and easy way to do this is to use an in ex pen sive pipe
cutter. Your local home supply store should carry them in
the plumbing de partment. A small lathe with a sharp cutter
also does a good job. Scribe the line deep enough, roughly
.015”, so that when you paint the tem plate, the line is still
clearly visible. Hand scribing this line is diffi cult and not rec-
ommended. The tube should now resemble Figure 17.
Learning the operation of a bender is fairly easy. The real challenge is accurately placing the tubing
into the bender so that the bend comes out in the right position. This short tutorial ex plains the simple
process of template bending.
Make a sample bend called the
Template
as shown in Figure 15. A permanent mark scribed on the
template allows you to measure and visualize where the bend should be placed in the tubing. Once bent
the tubing will spring out to a larger radius than the forming
die’s size in di cates. The larger the O.D. or the stronger
the tubing, the greater the springback. For in stance,
chromemoly tubing will springback roughly twice as far
as the ex act same size and wall thickness of welded seam
mild steel tubing. By using a tem plate bend with the same
kind of tubing you are going to bend, you do not have to
worry about this springback be cause the template has
already sprung out to its fin ished size.
You may ask if buying bending software is a good
idea. I believe bending software can only jus tified for two
reasons: Creating part drawings if the software supports that
function and for setting up a fully automatic CNC bender
for the initial test of a part with multiple bends. Even using
the software the bend locations usually need to be hand
tweaked for accu racy before going into production. Most
pro fessional fabricators use a method similar to what is
de scribed here. It is ex tremely easy, accu rate and fast.
However, what if you need to bend 500 pieces. How would
you use this process? Don’t worry, it’s a simple technique
that I will explain later but first let’s just complete a single
piece job. To do this I’m going to go through the whole
process that I use to make a four bend rollbar for a racecar
as shown in Figure 16. This is a great ex ample be cause it’s
a common request, there are no simple 90 de gree bends,
and it is generally a one-off piece. So hold on to your lug
nuts, here we go.
Bending Method #1 - Using Template Bends
The Easy Way To Position Bends
Figure 15 - Sample Template Bend
Let’s Make A Bend Template...
Figure 16
Sample Rollbar
Figure 17
Template Line