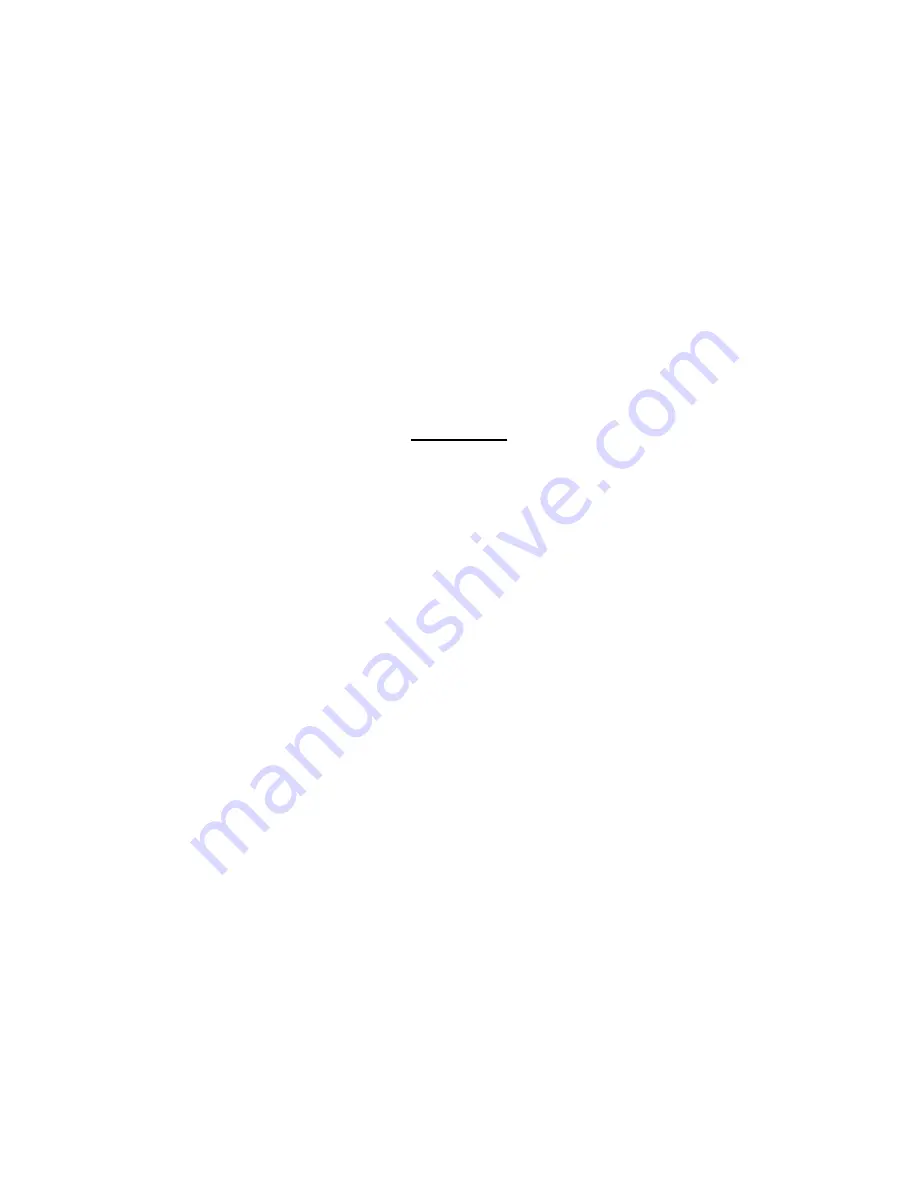
JBF Environmental Technology
24
handling it is important to prevent spills). Emergency pump shutdown is
possible as follows:
(1) Place pump hydraulic control lever in neutral.
(2) Shut down hydraulics.
(3) Close discharge valve.
v)
Operate the pump in reverse for 5- 10 seconds to clear the piping and pump
before terminating skimming operations and to prevent water from freezing in
the pump.
CAUTION
Before performing maintenance on the Desmi unit, shut down the hydraulic system.
C Belt
Adjustment/Maintenance
i)
To adjust the tension on the belt use the following procedure:
(1) Remove the forward pontoons to expose the belt adjustment slot in both
sides of the hull.
(2) Measure the belt catenary from the bottom center of the belt to the bottom of
the belt box structure.
(3) Unlock catenary adjustment screw locking nut.
(4) Adjust the catenary of the belt by turning the adjustment screws so that the
gap is 1 inch +/- ¼ inch.
(5) Lock the adjusting nut.
(6) Refasten the forward pontoons in place.
8 APPENDICIES
A SPARE/REPAIR PARTS LIST