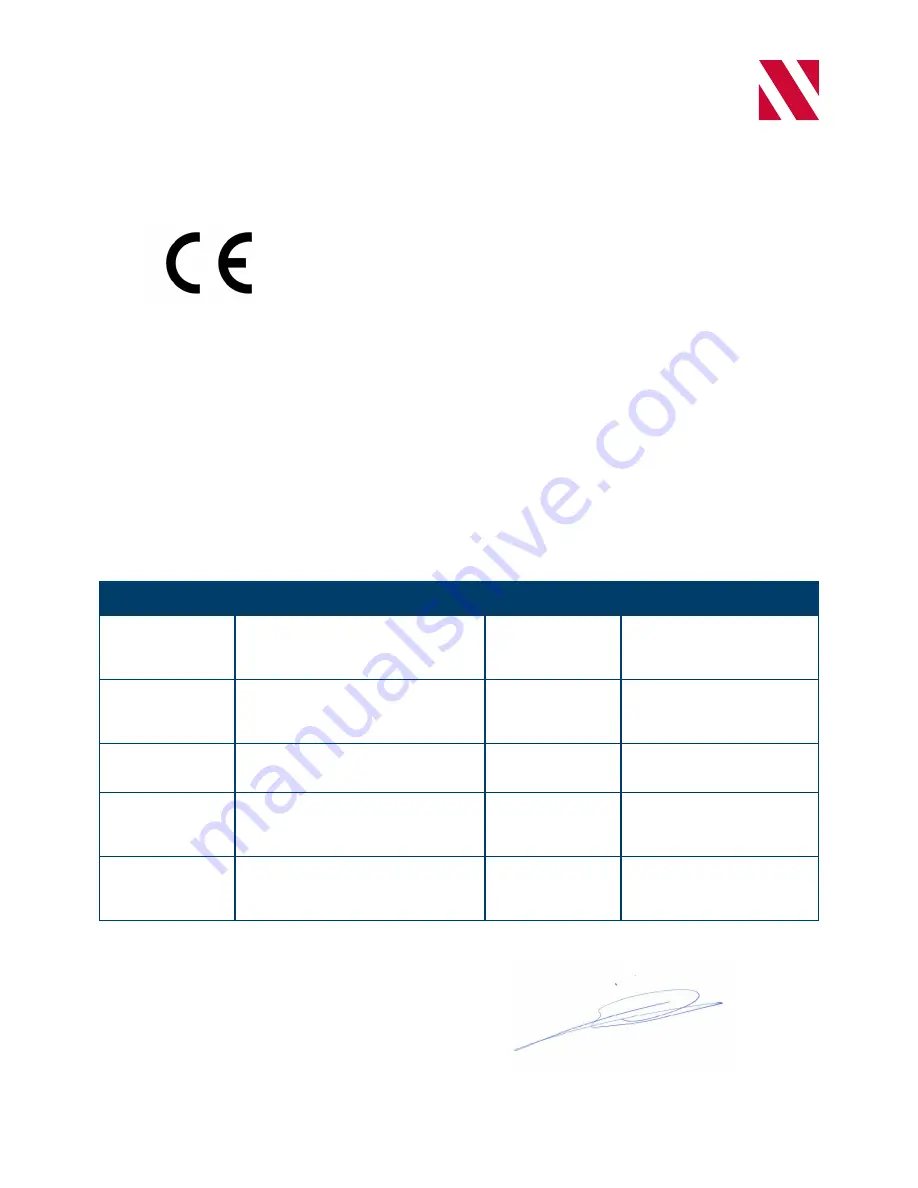
User manual for Javo Plus M2.0
Version 22300779
page 27 / 27
9.
EC declaration of conformity
In conformity with Machinery Directive 2006/42/EC, Annex II, section A
Nobels BV
Bulb Trade Park 1
2211SW Noordwijkerhout
The Netherlands
Declares that:
Machine:
Plus M2.0
Type:
Potting machine
conforms with the requirements of the
Machinery Directive 2006/42/EC
and of the
EMC Directive 2014/30/EC
complies with the follow harmonized European standards:
Harmonized
European standard Title
Harmonized
European standard Title
NEN-EN-ISO
12100:2010
Safety of machinery - Basic concepts,
general principles for design - Part 1:
Basic terminology, methodology
NPR-ISO/TR 14121-
2:2010
Safety Of Machinery - Risk
Assessment - Part 2: Practical
Guidance and Examples Of
Methods
NPR-ISO/TR
14121-2:2010
Safety Of Machinery - Risk
Assessment - Part 2: Practical
Guidance and Examples Of Methods
NEN-EN 349
Safety of machinery -
Minimum gaps to avoid
crushing of parts of the
human body
NEN-EN-ISO 13857
Safety of machinery - Safety distances
to prevent danger zones being
reached by upper and lower limbs
NEN-EN 13850
Safety of machinery -
Emergency stop - Principles
for design
NEN-EN 953
Safety of machinery - Guards -
General requirements for the design
and construction of fixed and movable
guards
NEN-EN-IEC
60204-1
Safety of machinery -
Electrical equipment of
machines - Part 1: General
requirements
NEN-EN-ISO
13849-1
Safety of machinery - Safety-related
parts of control systems - Part 1:
General principles for design
NEN-EN 983:1997
Safety of machinery - Safety
requirements for fluid power
systems and their components
- Pneumatics
The Netherlands, Noordwijkerhout,
Koos de Vink
January
2018
Managing
Director