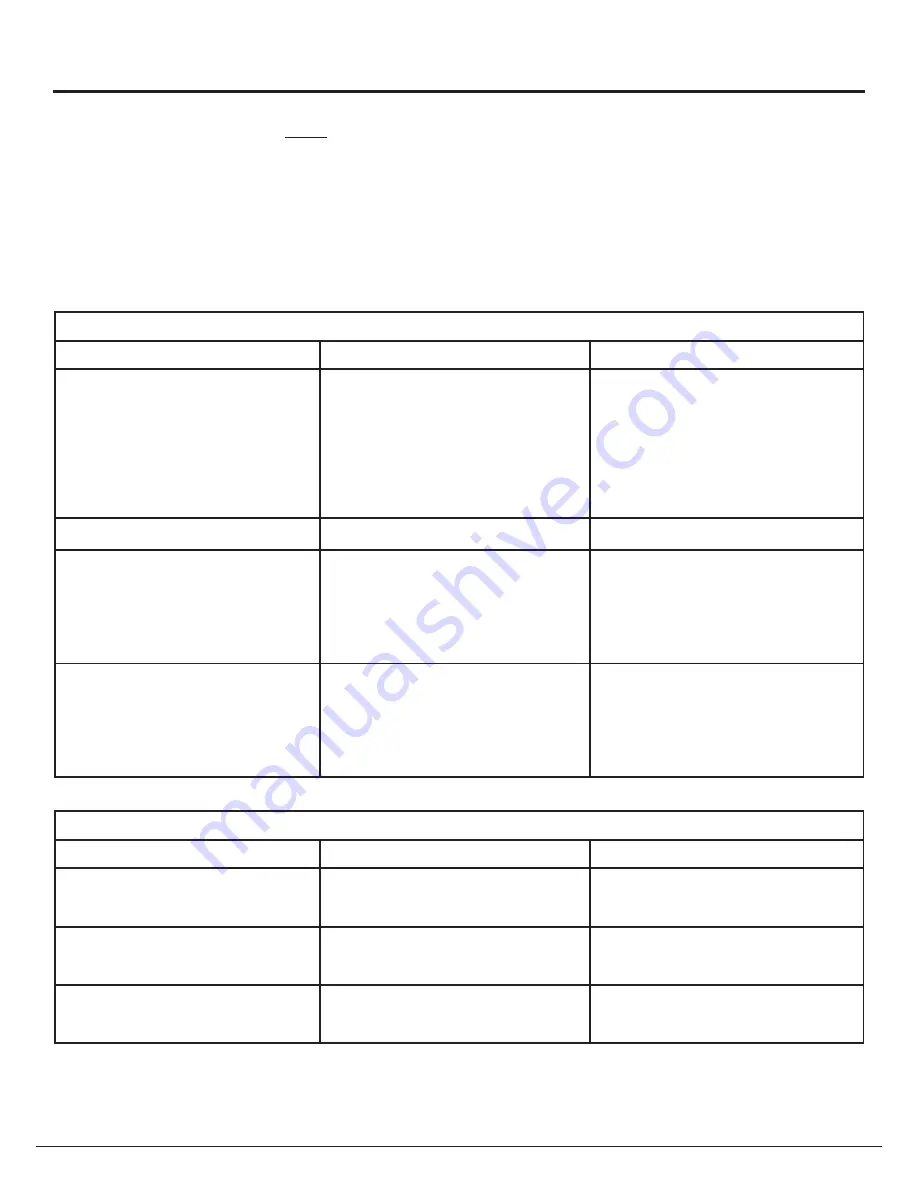
© 2018 Jason
®
Hydrotherapy • [email protected]
Page 15 of 16
Customer Service : 800.255.5766
TROUBLE SHOOTING GUIDE
If you believe the unit to be within the warranty period, you must contact Jason Customer Service: 1-800-255-5766 with the
bath’s Product and Serial numbers before work is started. These numbers can be found on the label on the front page of
this manual and also adhered to the underside of the bath above the equipment.
ALL WARRANTY REPAIRS MUST BE AUTHORIZED BY JASON BEFORE WORK IS STARTED.
FOR SERVICE, ALWAYS CONTACT YOUR DEALER OR AUTHORIZED SERVICE CENTER.
WARNING:
Always turn off power at the main electrical service panel when servicing the bath
ALL SYSTEMS
SYMPTOMS
POSSIBLE CAUSES
RECOMMENDED ACTION
System fails to operate
a. No power to the motor or control
box
b. Motor is not plugged into control
box
c. Pneumatic switch/Plastic air tubing
disconnected or broken
a. Reset circuit breakers and GFCI if
tripped. Check fuses and replace if
bad. Check voltage at motor when
control is on. If no voltage, control
is defective.
b. Make sure plug is fully inserted into
the control box outlet.
c. Check and reconnect if necessary.
Equipment does not manually shut off. a. Control defective
a. Refer to installer/dealer.
Equipment shuts off by itself or before
set time elapses.
a. Motor overheated and thermal
protection device deactivated
motor. (Possible low voltage)
b. GFCI
tripped.
a. Make sure motor has sufficient
ventilation, clear any obstructions
and allow motor to cool down.
Check service and wire size.
b. Refer to Jason Customer Service
Circuit breaker trips repeatedly
a. Defective breaker
b. Short circuit between the bath and
the breaker box.
c. Other items are connected to the
same circuit.
a. Replace
breaker
b. Refer to installer/dealer.
c. Refer to installer/dealer.
MICROSILK
®
[MS] PUMP SYSTEM
SYMPTOMS
POSSIBLE CAUSES
RECOMMENDED ACTION
Pump operates, but no microbubbles
are injected into the water.
a. Air intake clogged.
a. Refer to installer/dealer.
Pump operates, but water is not being
pumped.
a. Suction or discharge blocked.
a. Check and remove obstruction
Pump leaks.
a. Damaged or defective seal
a. Refer to installer/dealer.