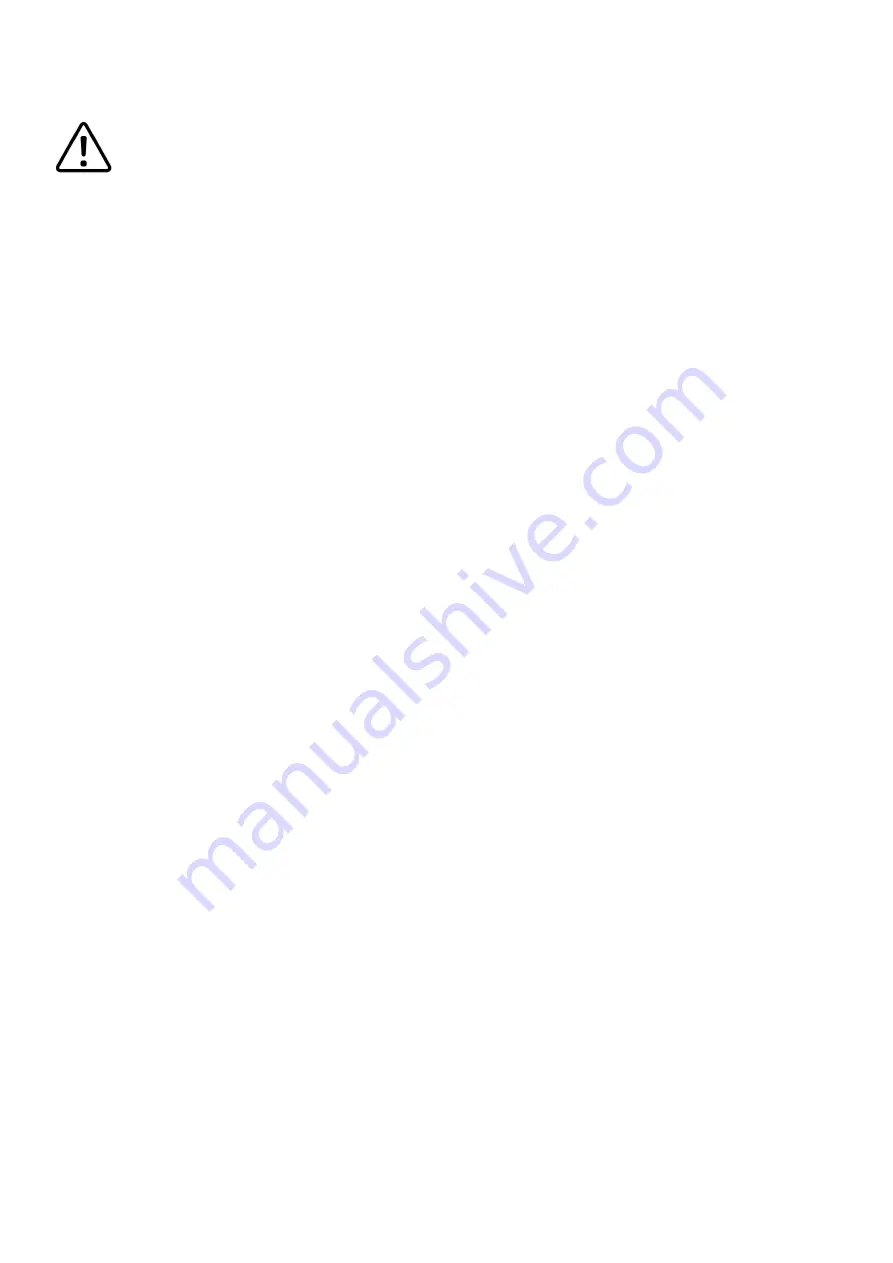
19
OPERATION
Before starting any welding or cutting activity ensure that you have suitable eye protection and
protective clothing. Also take the necessary steps to protect any persons within the welding
area.
Plasma cutting
Check that all connections have been made as required. Check the following before starting the machine.
Check if the machine is reliably grounded according to the relevant local standards.
Check that there are no bad contacts.
Check if the mains power cable is connected to the correct input voltage and rated supply.
Check if the plasma torch, connecting cables and gas hoses are in good condition and are not twisted.
Operation
1. Set cutting current according to the thickness of work piece.
2. Ensure that the cutting tip and consumables fitted matches the application and cutting amperage
setting of the machine.
3. Turn on the power switch on the back panel of the machine and the power LED is on.
4. To check the air pressure by placing the purge/run switch into purge to set the correct pressure.
5. Select trigger mode required via the front control panel: 2T and 4T.
6. There are two functions available: normal cutting and metal mesh cutting, please note that the
electrode and nozzle are more easily to wear out in metal mesh cutting due to the pilot arc being
more active for longer.
7. Bring the copper nozzle of the cutting torch at a distance of about 2mm between the copper nozzle
of the torch and the work piece and then push the torch trigger. For other modes of cutting/gouging,
please see below ‘Modes of cutting’.
8. After the arc has ignited, cutting starts and you can now start moving the torch at a regular speed
along the material you are cutting.
Modes of cutting
Drag cutting
is the process of dragging the tip of the torch along the work piece to cut the metal.
This is often the easiest way to cut while minimizing heat input but usually only on cutting currents of
40amps and below. Drag cutting does require a ‘drag’ cutting tip and you need to ensure that the plasma
machines output amperage is matched to the amperage with the tip. It can often be helpful to use a
non-conductive straight edge to help maintain a straight cut. This technique works best when cutting
metal that is less than or equal to 5mm. When you start to drag cut, you would place the tip of the torch
on the work piece and begin dragging the tip across the work piece. You should always start with the
torch placed at farthest point from you and then cut by pulling the torch towards you. Make sure to keep
the torch upright to the material being cut throughout the cutting process. As you are drag cutting ensure
you maintain a smooth and consistent travel speed to make a clean, precise cut.
Stand-off cutting
is a cutting technique where the operator will hold the plasma torch so that the tip of
the torch is between 3-4mm from the work piece to achieve the optimum cut. Stand-off cutting requires
a cutting tip that you need to ensure that the plasma machines output amperage is matched to the
amperage with the tip. A stand-off guide, roller guides and circle cutting guide kits can be very helpful in
creating the cuts you want. To begin cutting you would place the torch above the work piece of about
3-4mm and begin drawing the tip across the work piece. You should always start with the torch placed
at farthest point from you and then cut by pulling the torch towards you. Make sure to keep the torch
upright to the material being cut throughout the cutting process. As you are cutting ensure you maintain
a smooth and consistent travel speed to make a clean, precise cut.