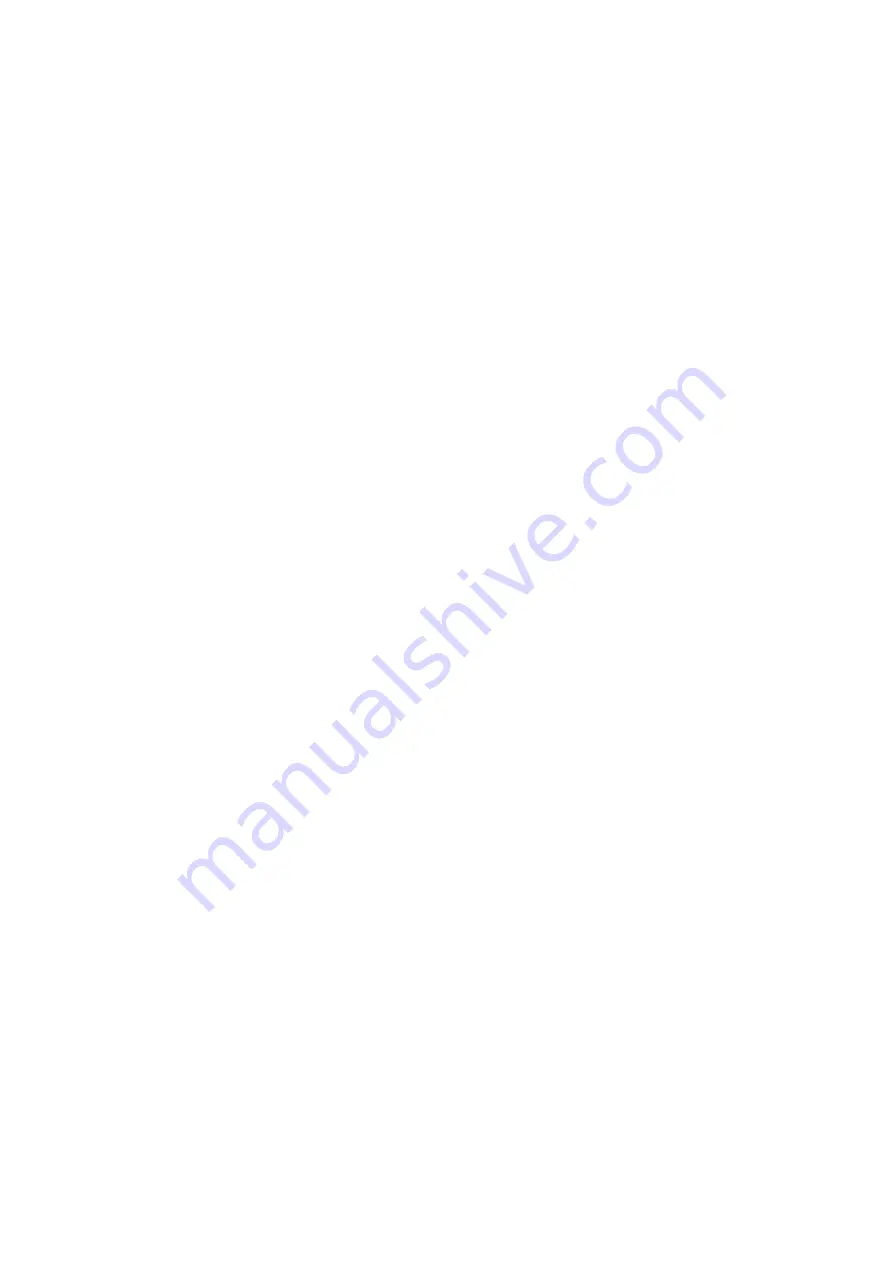
11
PRODUCT DETAILS AND APPLICATION
Advanced digital control mode
The Jasic plasma cutting machines JP-61 and JP-81 incorporate MUC intelligent digital control technology,
and all its major functions are performed using software controls. The digital control plasma cutting machine
offers many improvements in function and performance when compared with the traditional type plasma
cutting machines.
With PWM technology and high power component IGBTs, it inverts the DC voltage, which is rectified from
50Hz/60Hz input AC voltage, to 30K~50kHz AC high voltage. The voltage is dropped and rectified to output the
DC power supply for cutting. This inverter technology provides a machine which is smaller and much less
weight than the traditional style machine. The technology provides a high efficiency unit and a switching
frequency which is outside the audible range.
Good consistency and stable performance
In traditional machines consistency and performance is often governed by the tolerances of the components
used in manufacture and environmental such as temperature and humidity. In some cases the same machine
brand and type can vary in performance due to tolerance differences. One of the characteristics of digital
control is that it is not sensitive to the change of these parameters. The performance of cutting machine will
not be affected by the change of the parameters of individual parts. Therefore, the consistency and stability
of performance of the digital control cutter is better than that of traditional cutter.
Powerful cutting performance
The Jasic 61 and 81 plasma machines provide economical cutting of metals using compressed air as the
plasma gas source. The cutting speed is 1.8 times when compared with oxy acetylene cutting. These machines
can cut steel, stainless steel, copper, cast iron and aluminium easily and quickly. The arc is an easy to ignite
arc and uses a non HF arc ignition mode. There is a postflow function operates to cool the torch after cutting.
The simple operation and high cutting speed, smooth cutting surface make the plasma process and excellent
cutting method.
Product features
The Cut 61 and 81 cutting current can be accurately preset with seamless adjustment which is achieved
through the preset current function. Thus, the machine can be used to cut work pieces of different
thicknesses.
Low current is used when cutting thin plate and high current is used when cutting thick plate to ensure
good cutting quality and energy savings.
With protection function of over/under-voltage, thermal overheating and low gas pressure inside the
machine; gas-check and 2T/4T function.
Also as standard is the automated interface with remote start/stop, arc established ok to move signal
and a divided arc voltage output for a torch height controller making it suitable to connect to most CNC
cutting tables when fitted with a 180° cutting torch.
Application
The non HF pilot arc of the Cut 61 and 81 combined with the PT100 plasma torch offers excellent arc
ignition which can cut through rusty and painted metals along with ferrous and non ferrous easily which
can effectively prolong the lifespan of the electrode and nozzle of the plasma cutting torch.
It can be widely used in various industries involving metal cutting such as boiler and pressure vessel
manufacturing, chemical container manufacturing, power plant installation and construction industry,
metallurgy, chemical engineering, aerospace, automobile and engineering vehicles manufacturing and
construction etc.