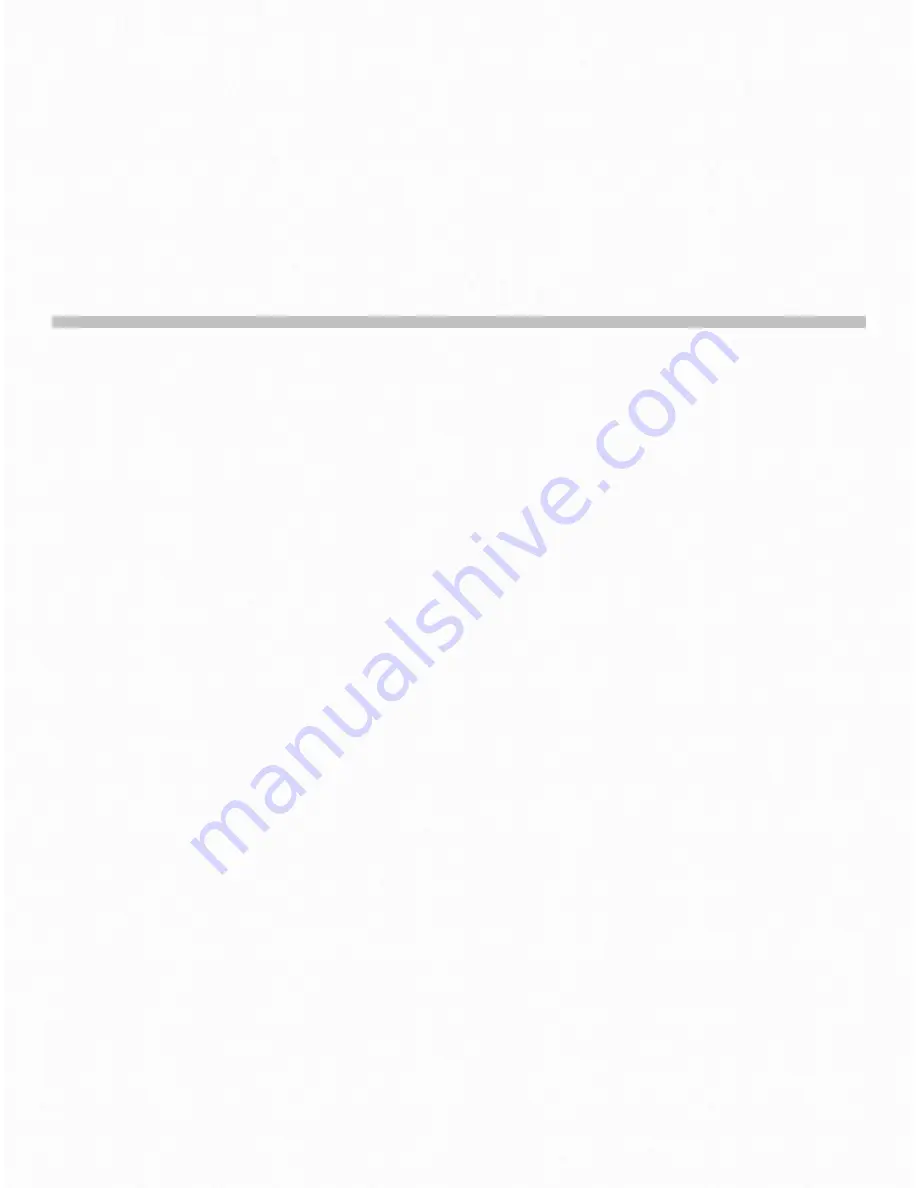
Installation
5
Unpacking
Check the packaging for any signs of damage.
Carefully remove the machine and retain the packaging until
the installation is complete.
Location
The machine should be located in a suitable position and
environment. Care should be taken to avoid moisture, dust,
steam, oil or corrosive gases
Place on a secure level surface and ensure that there is
adequate clearance around the machine to ensure natural
airflow.
Input connection
Before connecting the machine you should ensure that the
correct supply is available. Details of the machine
requirements can be found on the data plate of the machine
or in the technical parameters shown in the manual.
The equipment should be connected by a suitably qualified
competent person. Always ensure the equipment has a
proper grounding.
Never connect the machine to the mains supply with the
panels removed.
Output connections
Electrode polarity
In general when using manual arc welding electrodes the
electrode holder is connected the the positive terminal and
the work return to the negative terminal. Always consult the
electrode manufacturer’s data sheet if you have any doubts.
When using the machine for TIG welding the TIG torch
should be connected to the negative terminal and the work
return to the positive terminal
MMA welding
Insert the cable plug with the electrode holder into the “+”
socket on the front panel of the welding machine, and
tighten it clockwise.
Insert the cable plug of the work return lead into the “-”ve
socket on the front panel of the welding machine, and
tighten it clockwise
TIG welding
Insert the cable plug with the TIG torch into the “-” socket on
the front panel of the welding machine, and tighten it
clockwise.
Connect the TIG torch gas hose to the gas regulator
Insert the cable plug of the work return lead into the “+”ve
socket on the front panel of the welding machine, and
tighten it clockwise
MIG Welding
Insert the welding torch into the “Euro connector for torch in
MIG” output socket on the front panel of the machine, and
tighten it.
Install the wire spool on the spindle adapter.
Connect the cylinder equipped with the gas regulator to the
gas inlet on the back panel of the machine with a gas hose.
Insert the cable plug with work clamp into the “-” output
terminal on the front panel of the welding machine, and
tighten it clockwise.
Insert the quick plug of the gas / no gas selector into the “+”
output terminal of the welding machine, and tighten it
clockwise.
Ensuring that the groove size in the feeding position on the
drive roll matches the contact tip size of the welding torch
and the wire size being used. Release the pressure arm of
9
Summary of Contents for MIG 350C
Page 16: ...Electrical schematic 7 15 VDC...