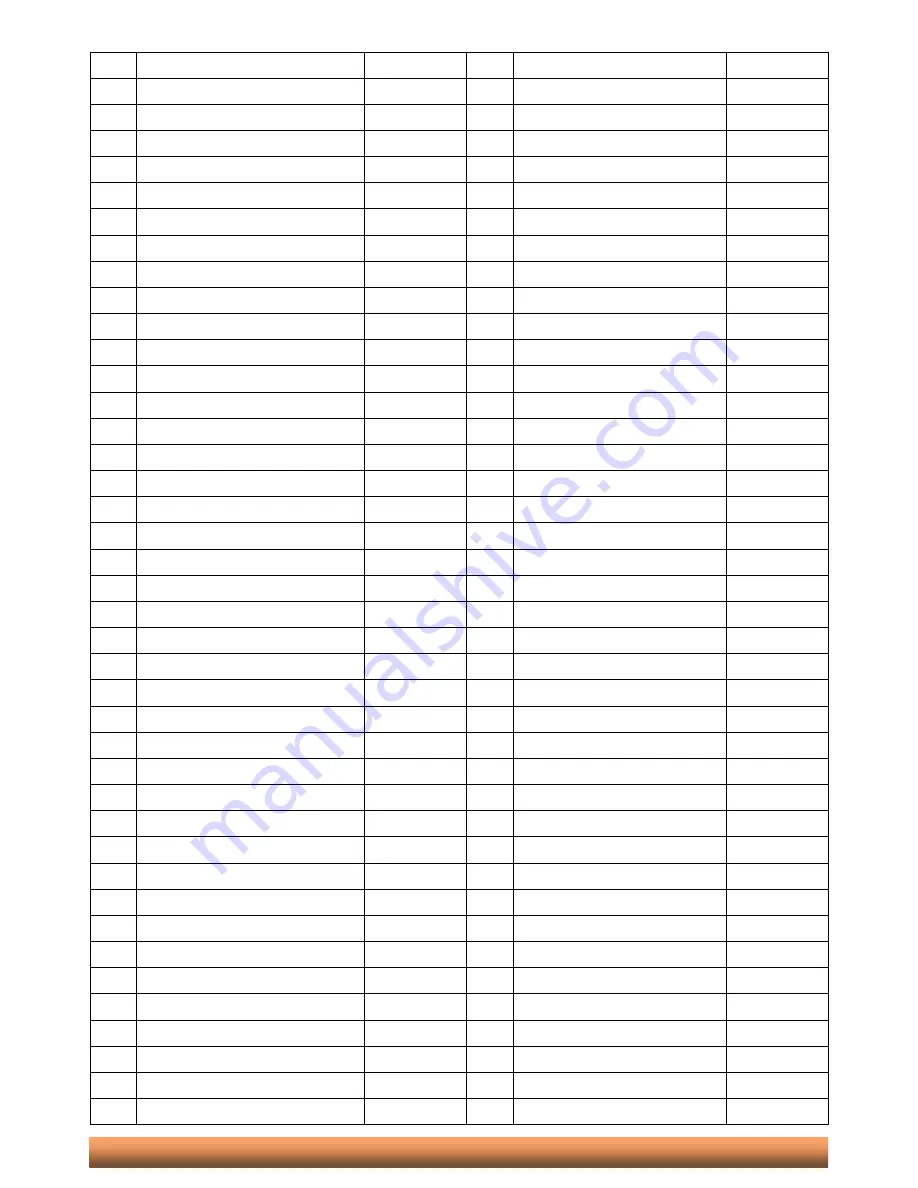
WWW.JASIC.CO.UK
34
Pos
Item
Part No
Pos
Item
Part No
1
Plastic front surround
10039142 41 Gathering board
10000789
2
Front panel
10040491 42 Control board
10000601
3
Plastic rear surround
10039141 43 Wire guard ring
10046803
4
Rear panel
10056987 44 Rectifier
10006635
5
Centre panel
10055865 45 IGBT drive board
10036190
6
Base
10050157 46 Capacitor
10005910
7
Deflector
10050200 47 Insulation pad
10015712
8
Heatsink
10050182 48 IGBT
10007255
9
Diode module
10046144 49 IGBT drive board
10036191
10 RC PCB
10000897 50 Thermal switch
10006443
11 Connector
10016014 51 Connection
10028065
12 Sleeve
10016048 52 Capacitor
10045958
13 Fan
10022052 53 Inductance
10002052
14 Bracket
10039104 54 Connection
10039978
15 Insulation
10050212 55 Capacitor
10005752
16 Main transformer
10039921 56 Capacitor hoop
10040011
17 Inductor
10002059 57 Heat sink
10050181
18 Capacitor
10005914 58 Deflector
10050159
19 Reactor
10040050 59 Support
10050196
20 Inductor
10002043 60 Absorbing board
10020611
21 Connection
10050160 61 Current transformer
10037728
22 Connection
10049037 62 Cover
10043859
23 Hall sensor
10050128 63 Cable clip
10004895
24 Insulation
10015717 64 Power cable
10042834
25 Plate
10015776 65 Cable retainer
10016621
26 Bracket
10055842 66 Socket
10045461
27 Handle
10027491 67 Circuit breaker
10006397
28 Switch
10052012 68 Power switch
10004935
29 Encoder
10046580 69 Switch
10048969
30 Knob
10004918 70 10 Pin socket
10055897
31 Socket
10028782 71 Insulation pad
10055864
32 Multi pin socket
10004702 72 Pins
10055882
33 Fuse holder
10006405 73 Baffle
10050140
34 Fuse
10006396 74 Fan guard
10007335
35 Line bank
10004960 75 Baffle
10050158
36 EMC board
10026027 76 Nameplate
10049065
37 Transformer
10006211 77 Clapboard
10049036
38 Transformer
10006210 78 EVA adhesive
10048674
39 Can converter board
10050199 79 Absorbing board
10001769
40 Power drive board
10050174
Summary of Contents for MIG 350 Pulse Separate
Page 1: ...Operator Manual www jasic co uk MIG Series MIG 350 Pulse Separate JM 350P ...
Page 9: ...WWW JASIC CO UK 9 Controls Front Rear ...
Page 30: ...WWW JASIC CO UK 30 Electrical Schematic ...
Page 31: ...WWW JASIC CO UK 31 Parts list FRONT REAR ...
Page 32: ...WWW JASIC CO UK 32 LEFT SIDE RIGHT SIDE ...
Page 33: ...WWW JASIC CO UK 33 TOP ...