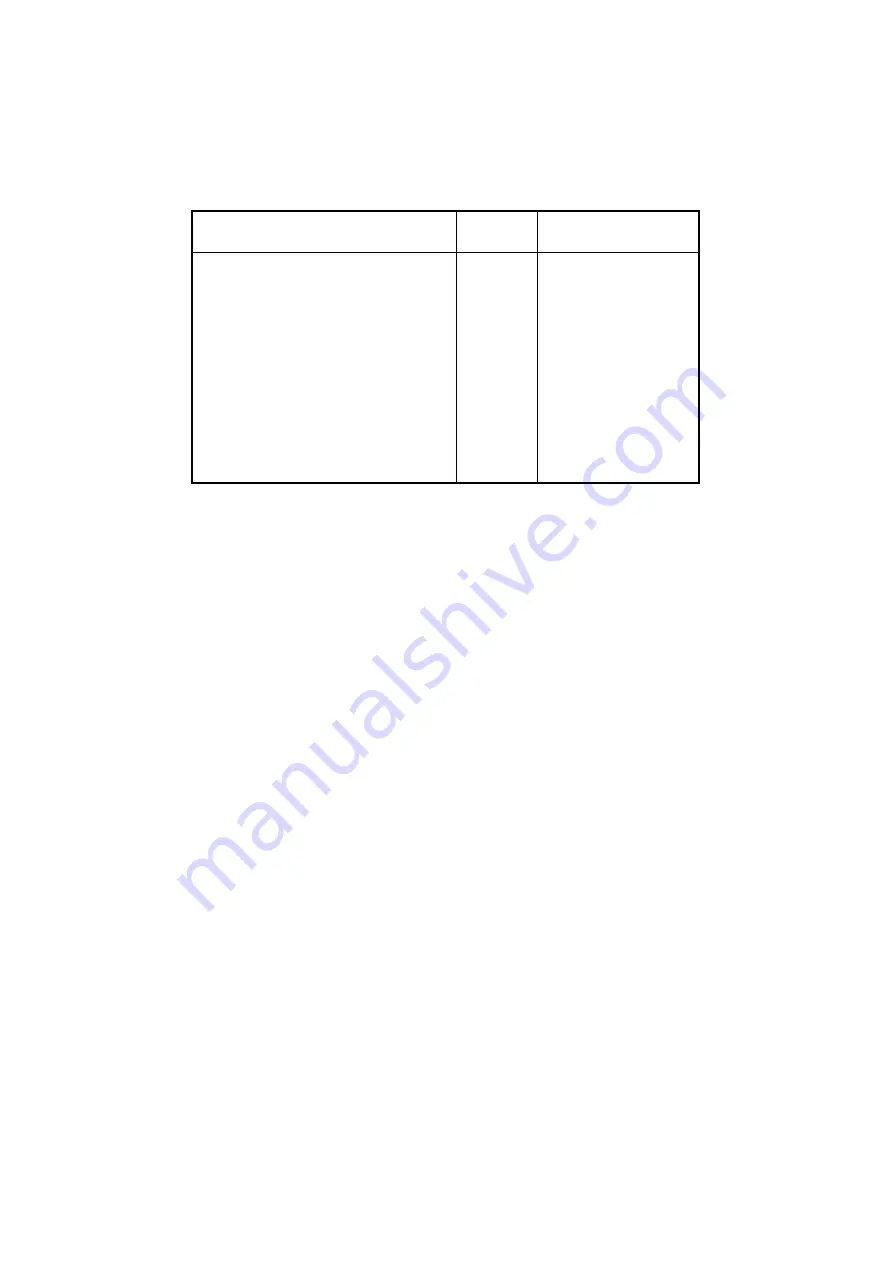
53
Table 5.1 lists the major consumable parts of the pump.
Table 5.1 Consumable Parts List
Part Name
Order
unit
Reference
diagram
Inlet tube assembly
Replacement plate filter
Plunger seal (black)
Line filter kit
Plunger washing mechanism
diaphragm
purge valve needle
Plunger
Pump head assembly (delivery)
Pump head assembly (modifier)
Check valve assembly (IN)
Check valve assembly (OUT)
1 set
5
3
2 sets
10
1
1
1
1
1
1
Fig. 5.14
Fig. 5.14
Fig. 5.9
Fig. 5.13
Fig. 5.20
Fig. 5.22
Fig. 5.25
Fig. 5.3
Fig. 5.3
Fig. 5.16
Fig. 5.16