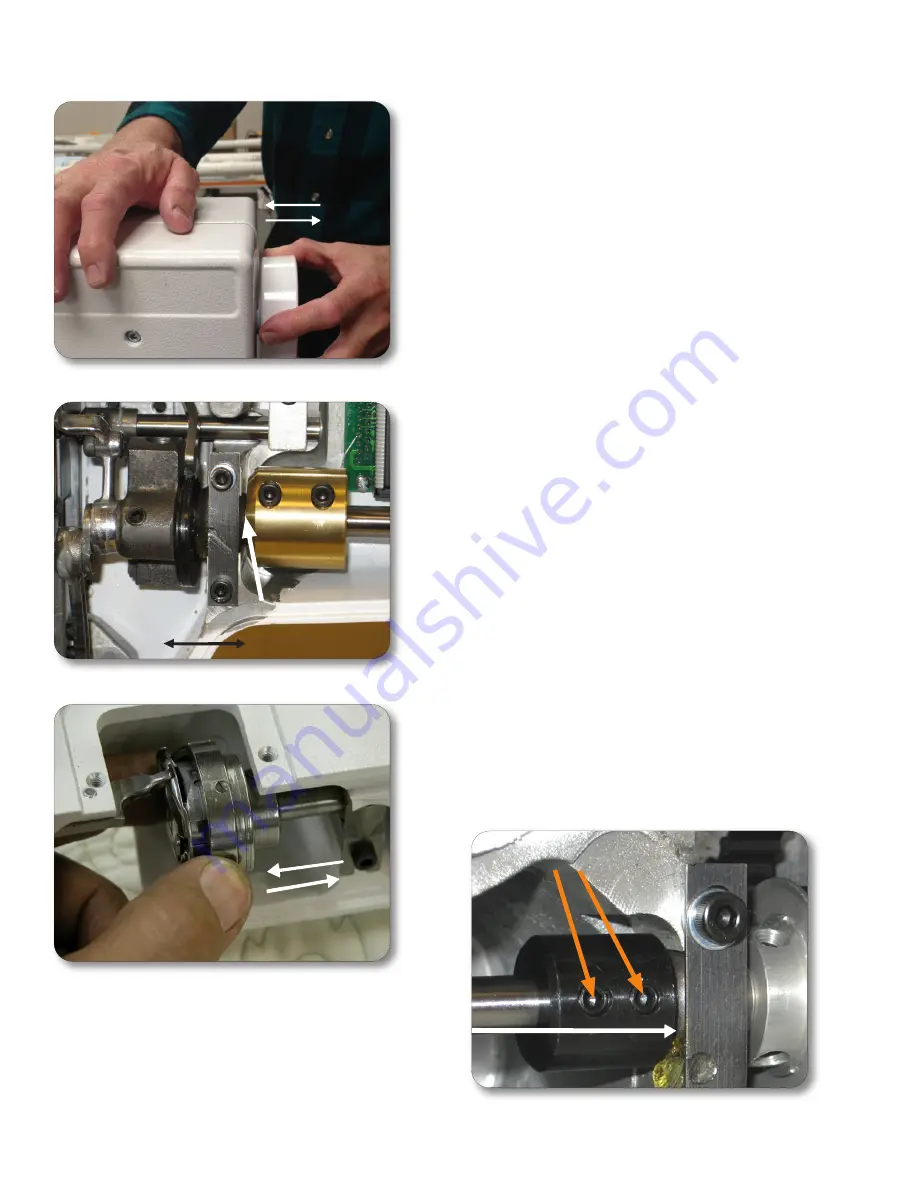
Page 14
Quit Maker Pro 18 VERSA
Figure 5.1
Figure 5.2
Figure 5.3
5. Axial Play Check and Adjustment
Axial or end play on shafting can result in noise, wear
and faulty sewing.
Check:
1. Check the main-shaft by pushing and pulling on
the hand wheel.
(Figure 5.1)
Note: A small amount
of main shaft axial play is permissible. Too much
main shaft play, however, may cause noise and or
stitching issues.
Remove play here
Test left to right
If a correction is necessary:
• Remove the front cover.
• Loosen the counterweight screws
(3 mm handle hex tool) (Figure 5.2).
• Adjust so that minimal to no play is detected.
• Provisionally set the screws.
• Check that the shaft has minimal play and no
tightness from the collar being too tight by
rotating the shaft through a few 360
o
rotations.
• Check that the timing of the eccentric is still
correct
(see counterweight timing Section 4 page
12, figure 4.2.
• Fully tighten the screws.
• Check shaft again for play or tightness.
2 .
Check
the hook shaft by pushing and pulling the
hook as shown in
(Figure 5.3).
If a correction is necessary:
•
Remove the front cover.
•
Remove the play by loosening the hook-shaft
thrust
collar
(not the hook-shaft timing pulley)
and adjusting out any axial play
(Figure 5.4).
Note:
There is no flat for the hook-shaft thrust collar.
•
Check for proper setting by rotating shaft through
a few 360
o
rotations.
Take out play here
Collar set screws
Collar set screws
Figure 4.4
Summary of Contents for Quilt Maker Pro 18 VERSA
Page 1: ...Janome Quilt Maker Pro 18 VERSA Service Manual...
Page 57: ...Janome America com Page 57 Notes...
Page 58: ......