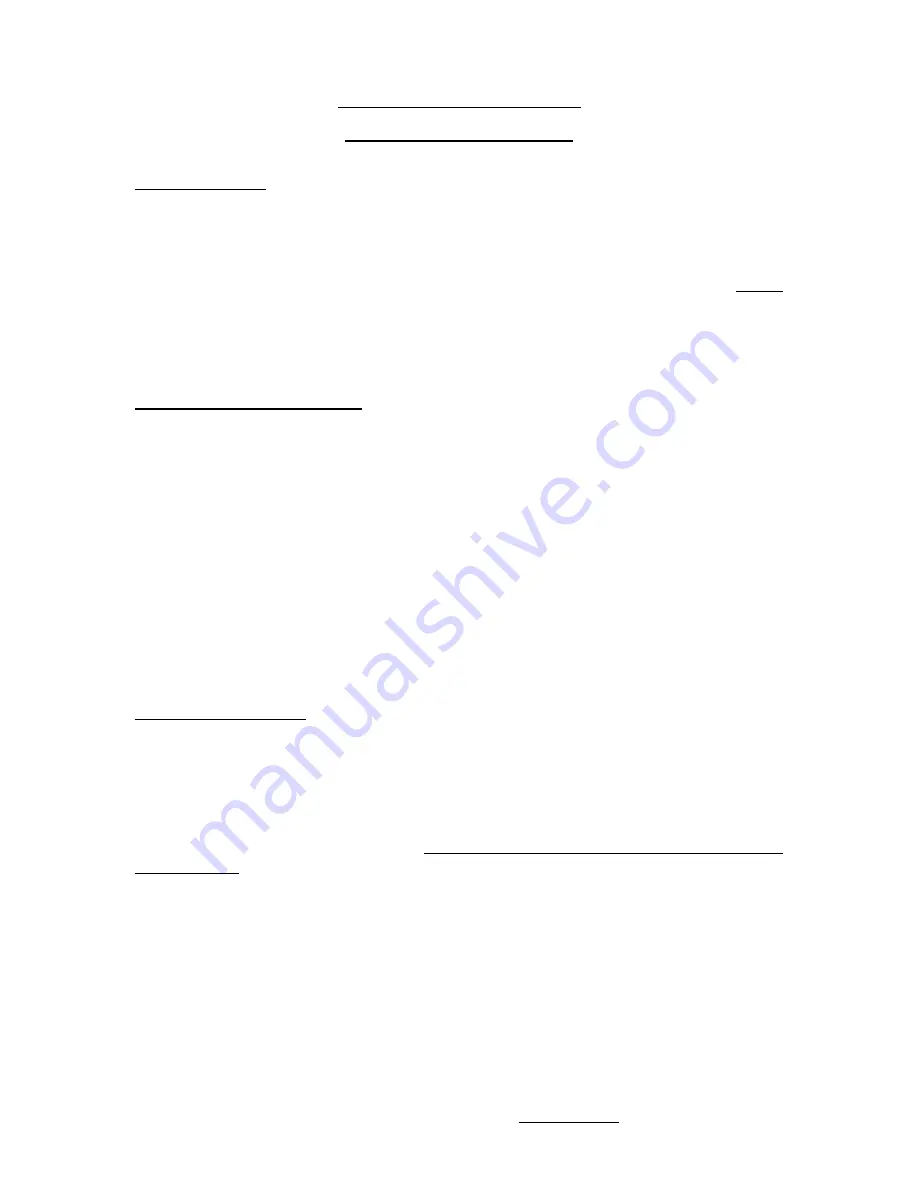
O
YLER
B
ARBECUE
P
IT
M
ODEL
700E / 1300E
COOK MODES
The “E” version of the Oyler Barbecue Pit Model 700/1300 uses electric heating
elements in addition to wood fuel for the cooking heat source. Additional
controls allow the operator to cook in one of two “Cook” Modes, “Standard” or
“Dual Fuel”. In addition, a “Cook and Hold” feature can be utilized in either
mode. The basic operation and use of the Oyler Barbecue Pit has not been
altered. The control design of this unit incorporates the same basic operation
sequencing of the standard 700/1300 series. Therefore, the basic
Operating
and
Maintenance Instructions
apply and should be referred to.
STANDARD COOK MODE
This mode allows the use of electric heating elements in addition to wood fuel.
Please note: the convection fan is engaged continuously in this mode, so overall
cooking times will be reduced.
Preheat pit in the “Standard Mode”. Load product and allow the pit to return to
the desired cooking temperature. Once the unit has reached desired cooking
temperature, turn the
“HTR.ELM”
switch to the “ON” position. A time delay
built into the “Dual Fuel” circuitry will allow the wood fuel to be consumed first,
utilizing the electric heating elements to “finish” the product. Used in this
method, the operator can regulate the use of the heating elements (and wood
fuel) in the cook cycle. A fully “stoked” firebox will delay (and may prevent) the
use of the electric heating elements until late in the cook cycle. Consequently,
a very small amount of wood fuel will bring on the elements much earlier. In
either case the electric heating elements will guarantee that the thermostat set
point will be maintained to the end of the cooking cycle.
Optional method for use in the “Dual Fuel” mode: Same as described above, except turn the red
switch labeled
“HTR.ELM”
to the “ON” position at the
beginning
of the preheat operation.
Using the pit in this method will allow the time delay for the electric heating elements to “time
out” during preheat and the electric elements will be used simultaneously with the wood fuel
from the beginning of the cook cycle.
Operation of the 700/1300 “E” Barbecue Pit in this mode is the
same as described on page
8
under the paragraph titled “Start Up”.
Turn the black
“COOK/OFF – COOK/HOLD”
switch to the “COOK”
position. The yellow
“EVAC”
switch should be in the “ON” position and the
“HTR.ELM”
switch should be in the “OFF” position. Build a fire in the
firebox using fresh cut hardwood.
Please note
: using the
“EVAC”
MODE WILL ACCELERATE
THE ESTABLISHMENT OF A FIRE IN THE FIREBOX. Once an adequate
fire has been established in the firebox, turn the
“EVAC”
switch to the
“OFF” position and set the thermostat to the desired cooking temperature.
For best results, allow the pit to preheat prior to loading the product.
DUAL FUEL MODE
1
Summary of Contents for 700E
Page 2: ...SN _______________...
Page 4: ......
Page 6: ......
Page 10: ...3...
Page 30: ...23...
Page 31: ...Figure 3 Oyler Through the Wall Installation with Direct Vent 24...
Page 32: ...25...
Page 33: ...Oyler With Exhaust Hood Vent Unit shown is a Model 700 Left Firebox Figure 5 26...
Page 36: ...29...
Page 38: ...31...
Page 39: ...32...
Page 40: ...33...
Page 41: ...34...
Page 42: ...35...
Page 46: ...39...
Page 47: ...40...
Page 48: ...41...
Page 49: ...42...
Page 50: ...43...
Page 55: ...48...
Page 56: ...49...
Page 60: ......