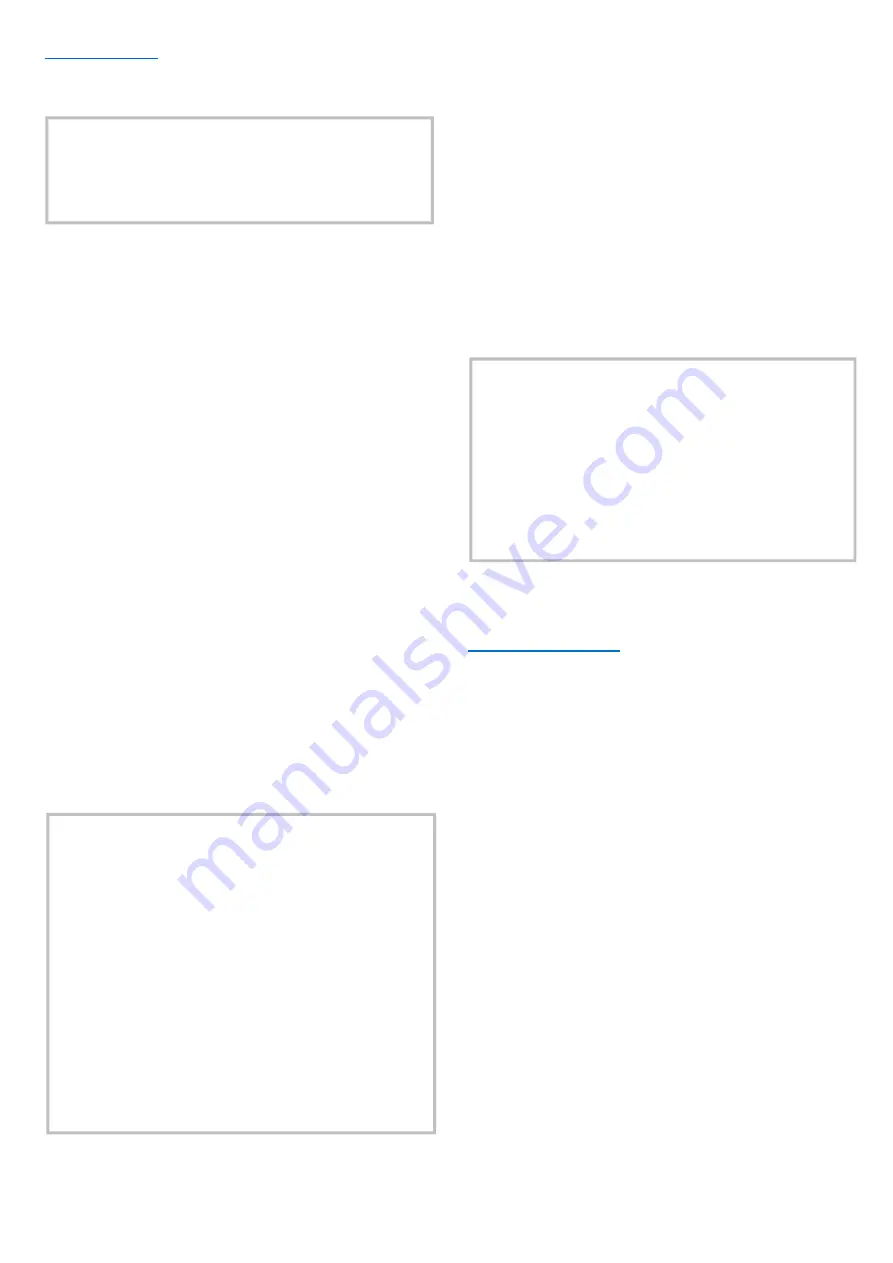
Issue: 01.05.2019
Page 7
Installation
Evacuation & Charging
Once pressure testing has been completed, the system can now be
evacuated to remove air and any moisture from the piping. This
can be done as follows:
•
Ensure any nitrogen charge is safely released from the
system.
•
Connect a gauge manifold to the connections on the
service valves on the condensing unit.
•
Connect a vacuum pump and vacuum gauge to the
system.
•
Ensure all gauge manifold and service valves are open as
required.
•
Evacuate the system until vacuum is below 250 microns
(0.25 torr).
Note: A triple evacuation procedure is recommended for all new
systems or where moisture is suspected
Once the system is isolated and the vacuum pump is switched off,
any rise in pressure indicates that either there may be a leak in the
system or moisture is still present. In this case, recheck the system
for leaks, repair as necessary, and then restart the evacuation
procedure. Once completed satisfactorily, the vacuum pump and
vacuum gauge can be removed.
At this point, the refrigerant charge can be added to the system as
required. Refrigerants must be charged in the liquid phase.
Charging
of liquid into the suction side of the system should ONLY be done
with a metering device.
Use calibrated weighing scales to record
the amount of refrigerant added to the system.
Electrical
Mains cable type and sizing must be selected for the
particular application and the electrical installation
should conform to the current local standards.
•
Cables to the condensing unit should wherever possible
be routed through the cable glands supplied on the rear
of the units.
•
Connect the mains supply to the units as per the wiring
diagrams on pages 13–20.
To gain access to the electrical box, turn the mains isolator switch
on the end of the unit to the OFF position, remove the screws from
the end cover panel and remove panel. The electrical box is located
behind the panel. Remove the screws in the electrical box cover to
access components.
Commissioning
Pre startup checks
Before starting the condensing unit, the following
checks should be carried out as a minimum:
•
Check electrical supply is correct and all connections are
sound.
•
All moving parts are free and guards fitted.
•
Compressor oil level satisfactory.
•
Initial settings for safety switches and fan speed control.
•
Overload set correctly.
•
All valves in correct operating position.
•
Initial refrigerant charge.
•
Crankcase heater energized for a minimum of 12 hours
before compressor start-up.
•
Gauge manifold connected to both low and high sides of
system.
Running the unit
•
Run the unit and check compressor and condenser fan
operation.
•
Check system pressures and temperatures, gas charge
and running currents of motors to ensure correct
operation.
Important Note:
The mains electrical supply to the condensing unit must be via a
suitable motor rated circuit breaker or fuse. A mains isolator is
fitted to all condensing units therefore an additional isolator is not
required unless site conditions or regulations dictate differently.
J & E Hall Fusion condensing units require either a 230 volt / 1
phase / 50Hz supply or a 400 volt / 3 phase / 50Hz supply, both of
which must include a Neutral and an Earth. These systems are not
suitable for any other supply voltages (other than a deviation of +/-
10% of the above values) and are not suitable for 60Hz supplies.
When utilizing a three phase supply, ensure that the compressor
motor rotates in the correct direction (Fusion Scroll models only).
Please see note on page 8.
Important Note:
Moisture prevents proper functioning of the compressor and the
refrigeration system. Ensure that a good quality vacuum pump is
used to pull a minimum vacuum of 250 microns (0.25 torr).
Important Note:
There must be no more than 10 compressor starts per hour. A
higher number reduces the service life of the compressor. There
is no minimum off time for scroll compressors, as they start
unloaded. However, consideration should be given to ensuring an
adequate minimum run time to ensure proper oil return. A
minimum runtime of 3 minutes after each compressor start and a
minimum idle time of 3 minutes after each stop are
recommended. Only during the pump down cycle may the
compressor run for shorter intervals.