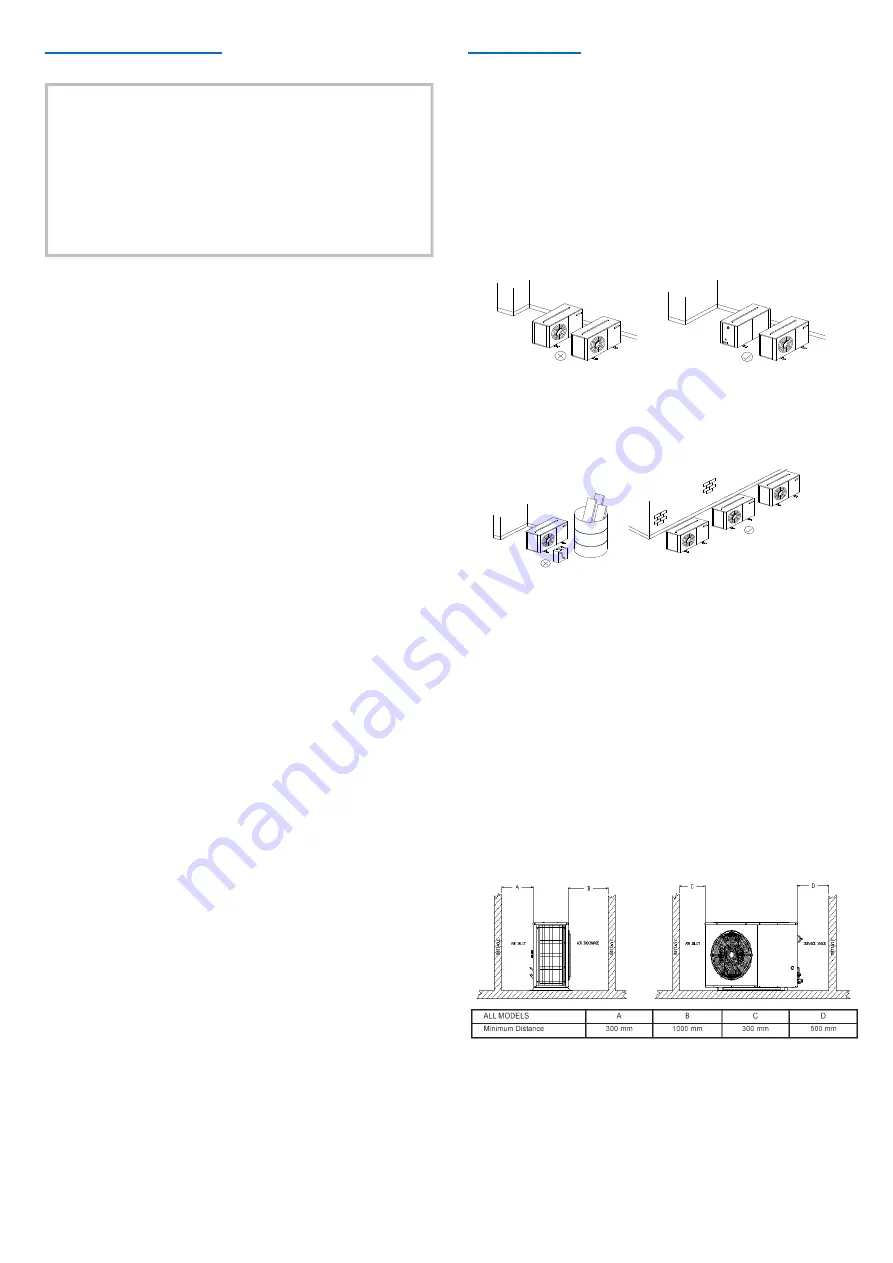
Issue: 01.05.2019 Page 4
Health and Safety
Before Installation
•
Ensure the units received are the correct models for the
intended application.
•
Ensure the refrigerant, voltage and MWP are all suitable for
the proposed application.
•
Check there is no damage to the units. Any damage should be
advised to the supplier immediately.
•
Check that the proposed equipment locations are suitable
and provide adequate support for the weight of the units.
During Installation and subsequent maintenance
•
Installation and maintenance are to be performed only by
qualified personnel who are familiar with local codes and
regulations, and experienced with this type of equipment.
•
If lifting equipment is required, ensure that it is suitable for
purpose, certificated and that the operatives are qualified to
use it.
•
Safe working methods are identified and operatives have
suitable Personal Protective Equipment (PPE).
•
Ensure the working area has adequate ventilation during
brazing procedures.
•
The units contain moving machinery and electrical power
hazards, which may cause severe injury or death. Disconnect
and shut off power before installation or service of the
equipment.
•
Refrigerant release into the atmosphere is illegal. Proper
evacuation, recovery, handling and leak testing procedures
must be observed at all times.
•
Units must be earthed and no maintenance work should be
attempted prior to disconnecting the electrical supply.
•
The electrical covers and fan guards must remain fitted at all
times.
•
Use of the units outside of the design conditions and the
application for which the units were intended may be unsafe
and be detrimental to the units, regardless of short or long-
term operation.
•
The units are not designed to withstand loads or stresses from
other equipment or personnel. Such extraneous loads or stress
may cause failure/leak/injury.
Installation
Unit location
•
In order to achieve maximum cooling capacity, the installation
location for the condensing unit should be carefully selected.
•
Install the condensing unit in such a way so that hot air ejected
by the condensing unit cannot be drawn in again (short circuit
of hot discharge air). Allow sufficient space for maintenance
around the unit.
•
Ensure that there is no obstruction to air flow into or out of
the unit. Remove obstacles which block air intake or
discharge.
•
The location must be well ventilated, so the unit can draw in
and distribute plenty of air thus lowering the condensing
temperature.
•
To optimize the unit running conditions, the condenser coil
must be cleaned at regular intervals.
•
The unit must be level in all directions.
Installation clearances
•
The installation location should allow sufficient space for air
flow and maintenance around the unit.
Important Note:
Only qualified personnel, who are familiar with refrigeration
systems and components including all controls, should perform
the installation and start-up of the system. To avoid potential
injury, use care when working around coil surfaces or sharp edges
of metal cabinets. All piping and electrical wiring should be
installed in accordance with all applicable codes, ordinances and
local by-laws.
X
X