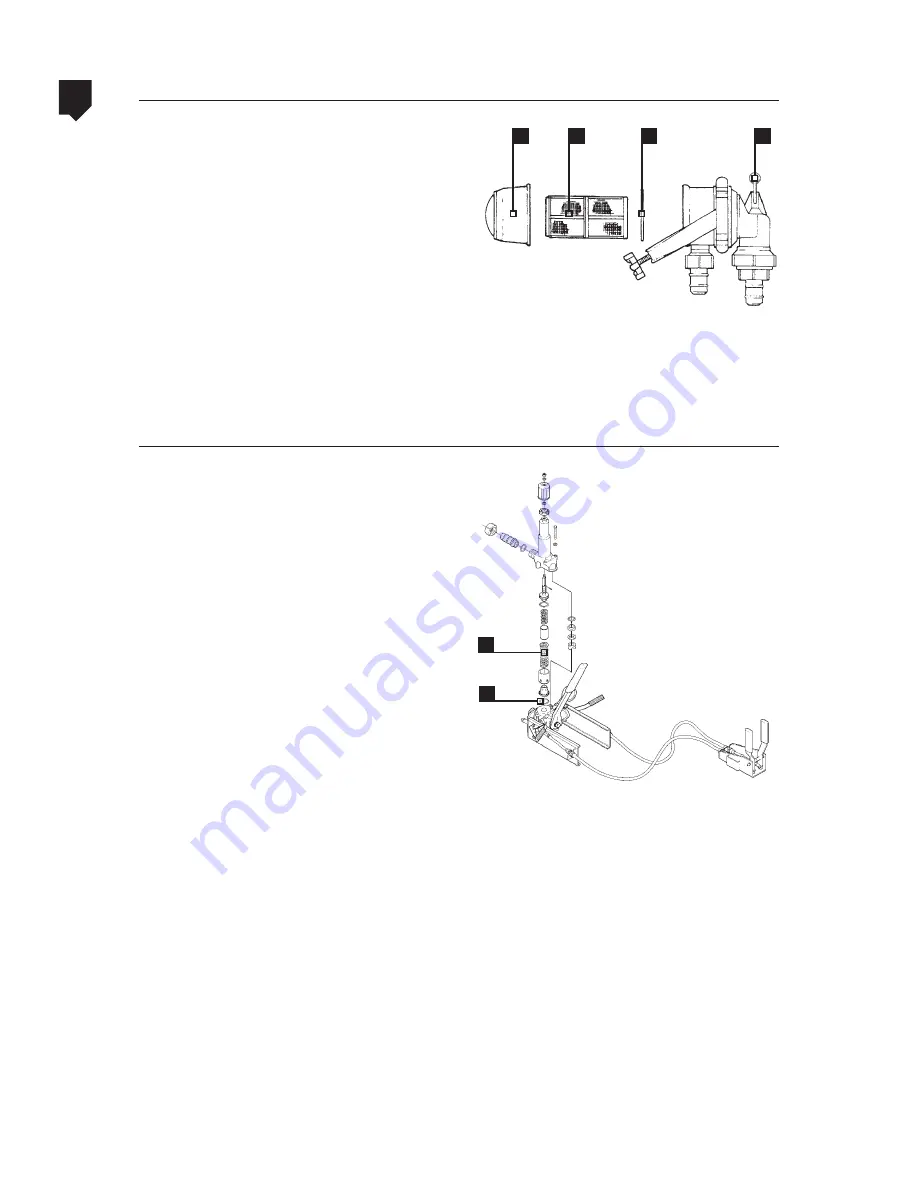
5-108
5
M
A
INTE
NAN
CE
ARBUS 1000
• The filter cleaning intervals depend on
the quality of the water employed and the
type of chemical used for that purpose.
• Clean the filters as necessary or every time
you supply the sprayer with chemical.
• Valve (A), filters elements (B) and ring (C)
Main filter
Pressure regulator (VAR)
• Disassemble the pressure regulator every
100 working hours.
• Check for wear on the valve seat (E) and
patches (F).
• Replace the parts if necessary.
D
B
C
A
E
F