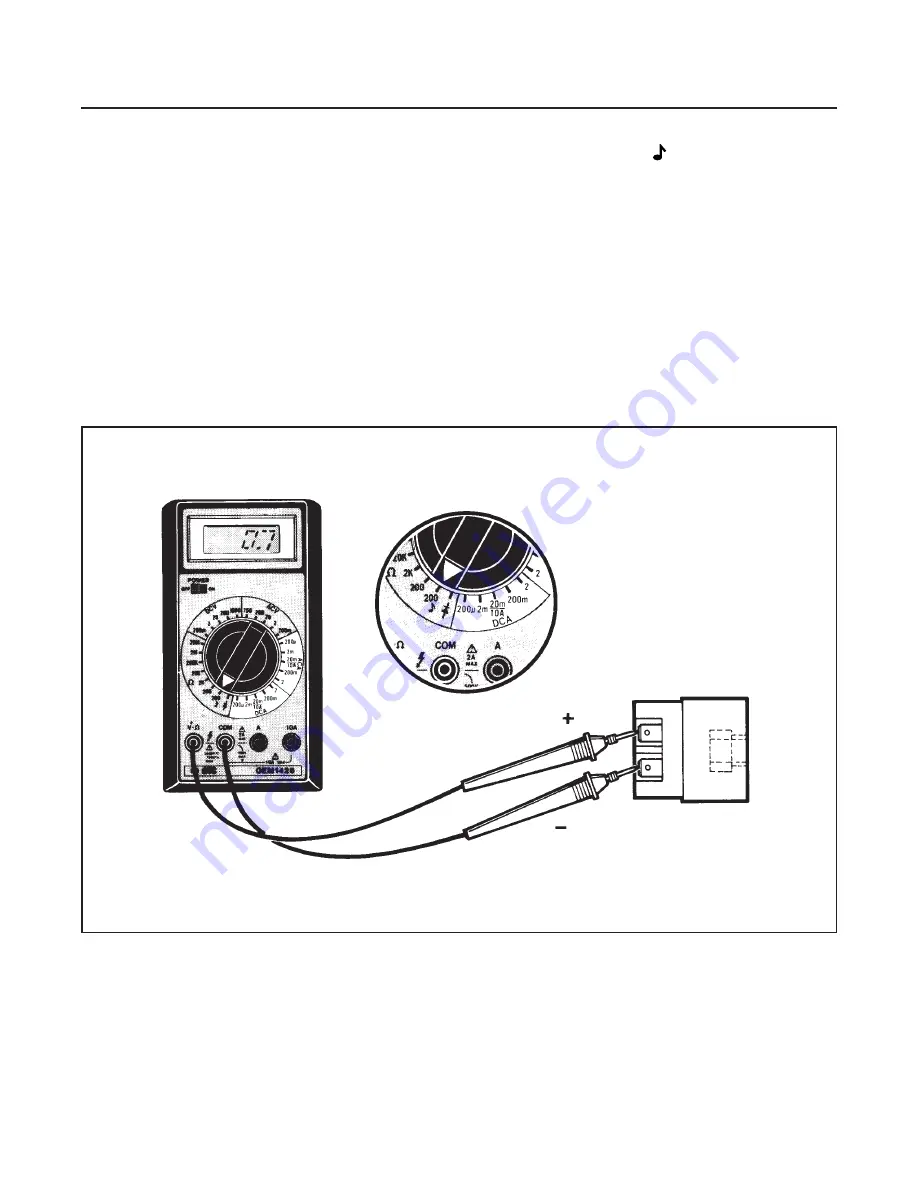
AIR CLEANER SERVICE INDICATOR
SWITCH TEST (See Figure 10G-22)
The air cleaner service indicator switch is a normally
OPEN (NO) switch. When the air filter becomes re-
stricted and 25" H2O of vacuum is reached, the switch
will close.
FIELD TEST
Using a jumper wire, remove both the BLU/WHT and
BLK wire and connect them together.
•
Air filter light comes ON, proceed with switch test,
Step 1.
•
Air filter light does not come on, check circuit wiring
and/or bulb.
SWITCH TEST
1. Set multimeter to 200
Ω
(ohms) scale.
2. Connect test leads as shown.
•
There should be no continuity through switch.
3. Draw 25" H2O vacuum on switch, switch contacts
should close, there should be a reading of 0–0.5
Ω
(ohms).
Replace a switch that does not meet all the above
test results or has resistance of 0.5
Ω
(ohms) or more.
ELECTRICAL SYSTEM
SECTION 10G. SWITCHES
10G-22
Figure 10G-22. Air Cleaner Service Indicator Switch Test
Summary of Contents for HR 5111
Page 2: ......
Page 4: ......
Page 6: ......
Page 12: ......
Page 14: ......
Page 26: ......
Page 28: ......
Page 30: ......
Page 32: ......
Page 40: ......
Page 42: ......
Page 44: ......
Page 46: ......
Page 49: ...GENERAL See Figure 4E 1 DRIVE TRAIN SECTION 4E AXLE 4E 1 4E Figure 4E 1 Axle Assembly...
Page 60: ......
Page 62: ......
Page 64: ......
Page 66: ......
Page 68: ......
Page 70: ......
Page 72: ......
Page 74: ......
Page 76: ......
Page 88: ......
Page 90: ......
Page 94: ...STEERING SECTION 6E STEERING CYLINDER 6E 4 Figure 6E 4 Steering Cylinder Assembly...
Page 96: ......
Page 98: ......
Page 100: ......
Page 102: ......
Page 106: ......
Page 108: ...HYDRAULICS SECTION 8A REPAIR AND SERVICE TOOLS AND MATERIALS 8A 2 Figure 8A 1 Wheel Restraint...
Page 116: ......
Page 120: ......
Page 124: ......
Page 126: ......
Page 128: ......
Page 136: ......
Page 137: ...REPAIR HYDRAULICS SECTION 8J REAR TRACTION MOTOR 8J 1 8J Figure 8J 1 Rear Traction Motor...
Page 138: ...HYDRAULICS SECTION 8J REAR TRACTION MOTOR 8J 2 Figure 8J 2 Seal Assembly...
Page 139: ...HYDRAULICS SECTION 8J REAR TRACTION MOTOR 8J 3 8J Figure 8J 3 O Rings and Seals...
Page 140: ......
Page 142: ......
Page 145: ...HYDRAULICS SECTION 8L LIFT CYLINDER 8L 3 8L Figure 8L 3 Lift Cylinder Assembly...
Page 148: ...HYDRAULICS SECTION 8L LIFT CYLINDER 8L 6 Figure 8L 6 Wing Cylinder Assembly...
Page 154: ......
Page 156: ......
Page 160: ...HYDRAULICS SECTION 8Q HYDRAULIC FIELD TEST PROCEDURES 8Q 4...
Page 163: ...HYDRAULICS SECTION 8Q HYDRAULIC FIELD TEST PROCEDURES 8Q 7 Figure 8Q 5 Reel System 8Q...
Page 185: ...HYDRAULICS SECTION 8R INSTRUMENT TEST 8R 21 8R Figure 8R 19 Left Wing Motor Circuit Tests...
Page 186: ...HYDRAULICS SECTION 8R INSTRUMENT TEST 8R 22 THIS PAGE INTENTIONALLY LEFT BLANK...
Page 191: ...HYDRAULICS 8S 1 8S Figure 8S 1 Flow Diagram...
Page 192: ...HYDRAULICS 8S 3 Figure 8S 2 Schematic Early...
Page 193: ...HYDRAULICS 8S 5 8S Figure 8S 3 Schematic Later...
Page 202: ...HYDRAULICS 8S 7 Figure 8S 4 Traction System 1 of 4...
Page 203: ...HYDRAULICS 8S 9 8S Figure 8S 5 Power Steering System 2 of 4...
Page 204: ...HYDRAULICS 8S 11 Figure 8S 6 Lift System 3 of 4...
Page 205: ...HYDRAULICS 8S 13 8S Figure 8S 7 Mower System 4 of 4...
Page 206: ......
Page 208: ......
Page 210: ......
Page 212: ......
Page 214: ......
Page 216: ......
Page 218: ......
Page 226: ......
Page 249: ...ELECTRICAL SYSTEM SECTION 10G SWITCHES 10G 5 10G Figure 10G 5 Ignition Switch Test Step 4...
Page 268: ......
Page 272: ......
Page 280: ......
Page 284: ......
Page 286: ......
Page 288: ......
Page 292: ......
Page 302: ......
Page 310: ......
Page 312: ......
Page 314: ......
Page 316: ......
Page 318: ......
Page 323: ...ATTACHMENTS SECTION 12D MOWERS 12D 5 12D Figure 12D 5 Motor Rotation By Code Letter...
Page 328: ...ATTACHMENTS SECTION 12F CASTER WHEELS 12F 2 Figure 12F 2 Caster Wheel Repair...
Page 329: ...13 THIS SECTION INTENTIONALLY LEFT BLANK SECTION 13 OPTIONS...
Page 330: ......
Page 332: ......
Page 335: ...MISCELLANEOUS SECTION 14A PRECAUTION DECAL LOCATIONS 14A 3 14A MOWER Part No J T338141 1...
Page 336: ......
Page 337: ...MISCELLANEOUS SECTION 14B CONVERSION CHARTS 14B 1 14B MILLIMETERS TO DECIMALS...