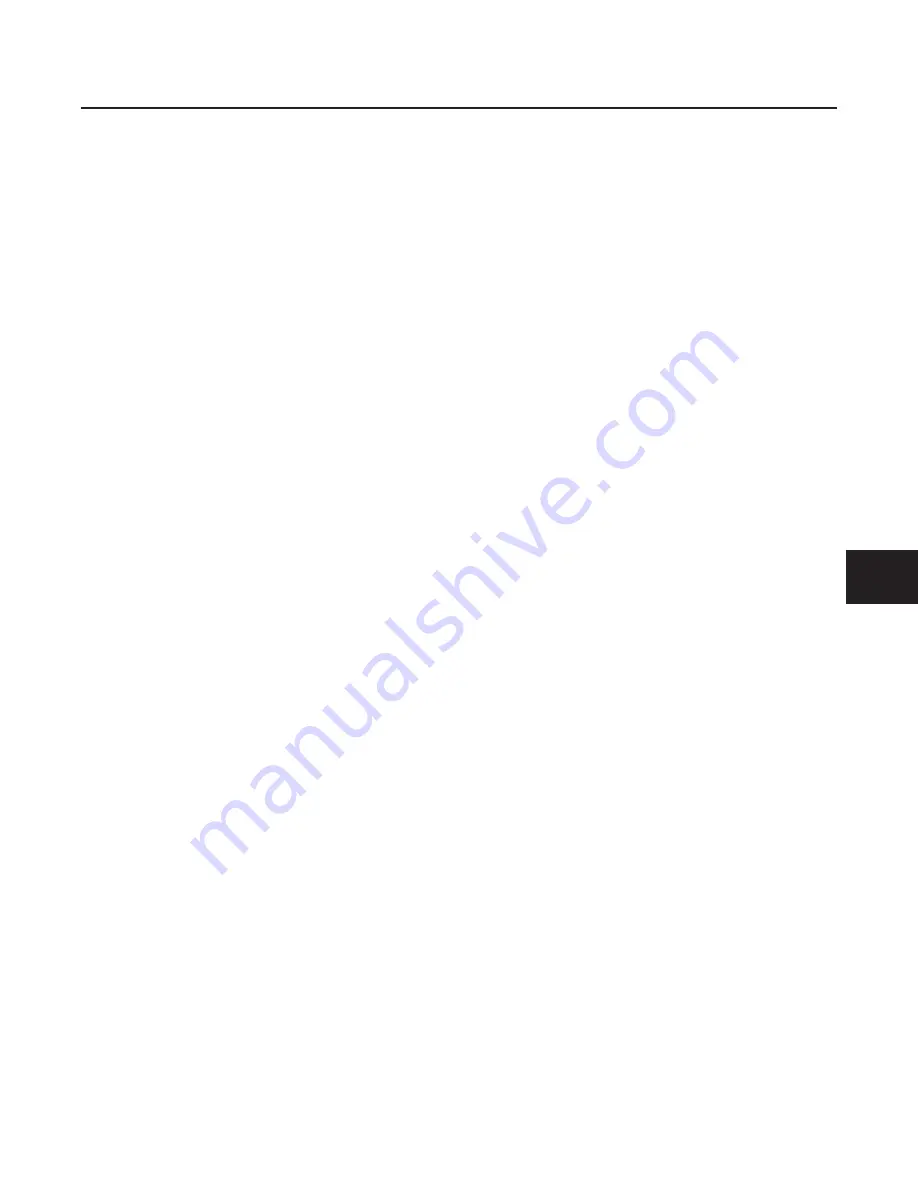
GENERAL
Tires are subject to damage from sharp objects. If large
punctures or tears occur, it is advisable to take the tire
(installed on the wheel) to a qualified tire repair shop.
The front drive wheels are bolted directly to the wheel
hub which is part of the front axle assembly. See
Section 4 for bearing repair.
The rear drive wheels are bolted directly to the wheel
hub mounted to the motor. There are no wheel bear-
ings to repair or service.
SERVICE
Tires are inflated to 20 to 24 psi (1.4 to 1.6 bars) front,
and 6 to 10 psi (.41 to .68 bars) rear. This pressure
gives the best results for average use. Tire pressure
should be equal for each set of tires.
If a tire is removed from the rim it should be inflated to
approximately 30 to 35 psi (2.0 to 2.4 bars), when it is
replaced. This assures proper seating of the tire bead
to the rim. Then reduce the pressure to the desired
level before using.
NOTE
Never use grease or oil on the rim when mount-
ing a tire.
Bead sealing of the tires may be repaired by using tire
sealants available from tire repair shops. Always use
non-hardening tire sealant. Hardening type tire seal-
ants eliminate the cushioning effect from the pneu-
matic tire and can result in axle, differential, hydraulic
motor and frame failure. To apply sealant:
1. Break one bead from seal on rim and pull out past
rim flange at bottom or install through valve stem.
2. Pour sealant into tire cavity.
3. Reseat bead on rim by inflating the tire to 20 to 24
psi (1.4 to 1.6 bars).
4. Rotate tire slowly to spread compound.
5. Reduce tire pressure to specified pressure.
6. Torque front wheel nuts to 100–120 ft-lbs. (135–
162 N.m). Check torque daily until torque is main-
tained.
WHEELS & TIRES
SECTION 7C. TIRE SERVICE
7C-1
7C
Summary of Contents for HR 5111
Page 2: ......
Page 4: ......
Page 6: ......
Page 12: ......
Page 14: ......
Page 26: ......
Page 28: ......
Page 30: ......
Page 32: ......
Page 40: ......
Page 42: ......
Page 44: ......
Page 46: ......
Page 49: ...GENERAL See Figure 4E 1 DRIVE TRAIN SECTION 4E AXLE 4E 1 4E Figure 4E 1 Axle Assembly...
Page 60: ......
Page 62: ......
Page 64: ......
Page 66: ......
Page 68: ......
Page 70: ......
Page 72: ......
Page 74: ......
Page 76: ......
Page 88: ......
Page 90: ......
Page 94: ...STEERING SECTION 6E STEERING CYLINDER 6E 4 Figure 6E 4 Steering Cylinder Assembly...
Page 96: ......
Page 98: ......
Page 100: ......
Page 102: ......
Page 106: ......
Page 108: ...HYDRAULICS SECTION 8A REPAIR AND SERVICE TOOLS AND MATERIALS 8A 2 Figure 8A 1 Wheel Restraint...
Page 116: ......
Page 120: ......
Page 124: ......
Page 126: ......
Page 128: ......
Page 136: ......
Page 137: ...REPAIR HYDRAULICS SECTION 8J REAR TRACTION MOTOR 8J 1 8J Figure 8J 1 Rear Traction Motor...
Page 138: ...HYDRAULICS SECTION 8J REAR TRACTION MOTOR 8J 2 Figure 8J 2 Seal Assembly...
Page 139: ...HYDRAULICS SECTION 8J REAR TRACTION MOTOR 8J 3 8J Figure 8J 3 O Rings and Seals...
Page 140: ......
Page 142: ......
Page 145: ...HYDRAULICS SECTION 8L LIFT CYLINDER 8L 3 8L Figure 8L 3 Lift Cylinder Assembly...
Page 148: ...HYDRAULICS SECTION 8L LIFT CYLINDER 8L 6 Figure 8L 6 Wing Cylinder Assembly...
Page 154: ......
Page 156: ......
Page 160: ...HYDRAULICS SECTION 8Q HYDRAULIC FIELD TEST PROCEDURES 8Q 4...
Page 163: ...HYDRAULICS SECTION 8Q HYDRAULIC FIELD TEST PROCEDURES 8Q 7 Figure 8Q 5 Reel System 8Q...
Page 185: ...HYDRAULICS SECTION 8R INSTRUMENT TEST 8R 21 8R Figure 8R 19 Left Wing Motor Circuit Tests...
Page 186: ...HYDRAULICS SECTION 8R INSTRUMENT TEST 8R 22 THIS PAGE INTENTIONALLY LEFT BLANK...
Page 191: ...HYDRAULICS 8S 1 8S Figure 8S 1 Flow Diagram...
Page 192: ...HYDRAULICS 8S 3 Figure 8S 2 Schematic Early...
Page 193: ...HYDRAULICS 8S 5 8S Figure 8S 3 Schematic Later...
Page 202: ...HYDRAULICS 8S 7 Figure 8S 4 Traction System 1 of 4...
Page 203: ...HYDRAULICS 8S 9 8S Figure 8S 5 Power Steering System 2 of 4...
Page 204: ...HYDRAULICS 8S 11 Figure 8S 6 Lift System 3 of 4...
Page 205: ...HYDRAULICS 8S 13 8S Figure 8S 7 Mower System 4 of 4...
Page 206: ......
Page 208: ......
Page 210: ......
Page 212: ......
Page 214: ......
Page 216: ......
Page 218: ......
Page 226: ......
Page 249: ...ELECTRICAL SYSTEM SECTION 10G SWITCHES 10G 5 10G Figure 10G 5 Ignition Switch Test Step 4...
Page 268: ......
Page 272: ......
Page 280: ......
Page 284: ......
Page 286: ......
Page 288: ......
Page 292: ......
Page 302: ......
Page 310: ......
Page 312: ......
Page 314: ......
Page 316: ......
Page 318: ......
Page 323: ...ATTACHMENTS SECTION 12D MOWERS 12D 5 12D Figure 12D 5 Motor Rotation By Code Letter...
Page 328: ...ATTACHMENTS SECTION 12F CASTER WHEELS 12F 2 Figure 12F 2 Caster Wheel Repair...
Page 329: ...13 THIS SECTION INTENTIONALLY LEFT BLANK SECTION 13 OPTIONS...
Page 330: ......
Page 332: ......
Page 335: ...MISCELLANEOUS SECTION 14A PRECAUTION DECAL LOCATIONS 14A 3 14A MOWER Part No J T338141 1...
Page 336: ......
Page 337: ...MISCELLANEOUS SECTION 14B CONVERSION CHARTS 14B 1 14B MILLIMETERS TO DECIMALS...